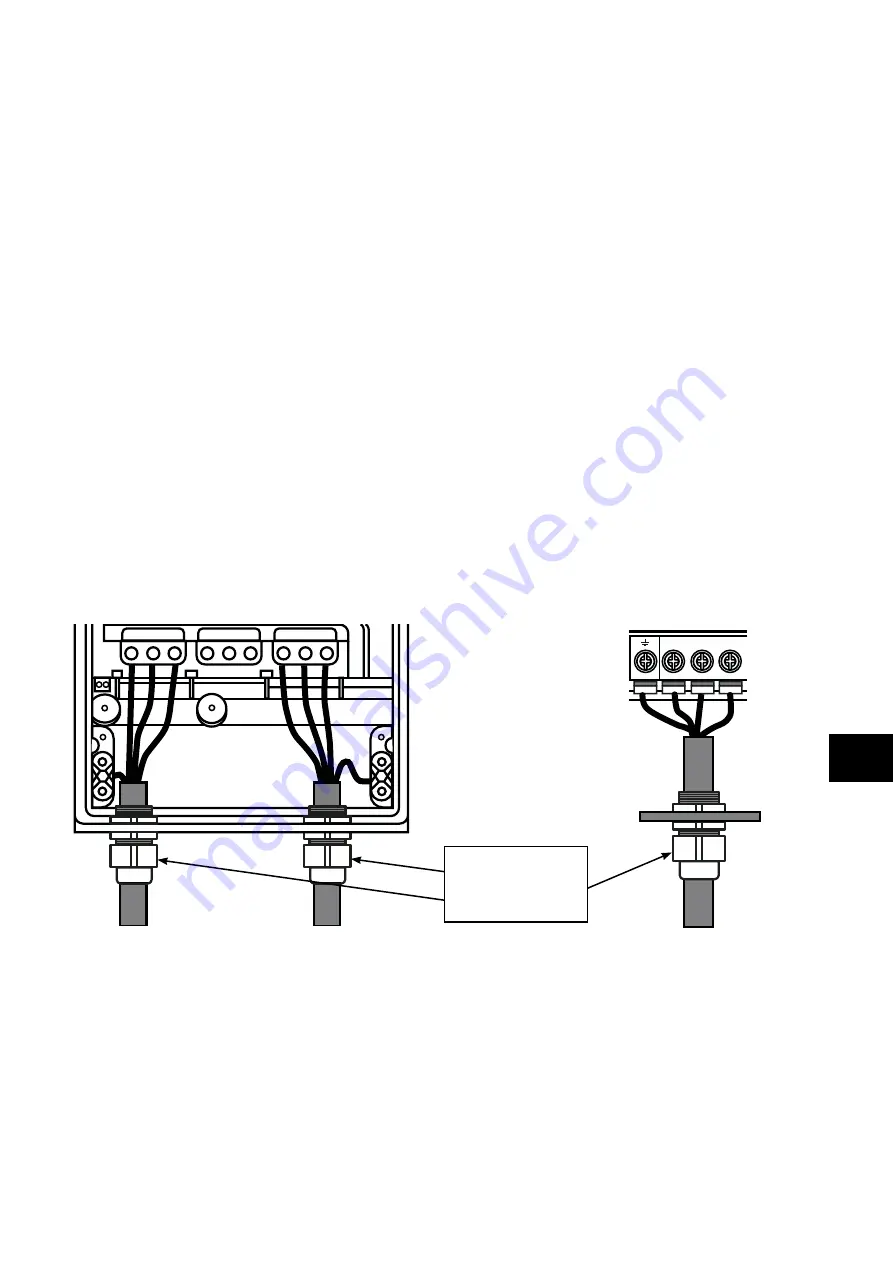
Version 3.07
| Optidrive P2 User Guide |
29
www.invertekdrives.com
General
1
Compliance with category C1 conducted emissions only is achieved.
Supply Cable
2
A screened (shielded) cable suitable for fixed installation with the relevant mains voltage in use. Braided or twisted type screened
cable where the screen covers at least 85% of the cable surface area, designed with low impedance to HF signals. Installation of
a standard cable within a suitable steel or copper tube is also acceptable.
3
A cable suitable for fixed installation with relevant mains voltage with a concentric protection wire. Installation of a standard cable
within a suitable steel or copper tube is also acceptable – in this case, ensure that metal tube is adequately grounded..
4
A cable suitable for fixed installation with relevant mains voltage. A shielded type cable is not necessary.
Motor Cable
5
A screened (shielded) cable suitable for fixed installation with the relevant voltage in use. Braided or twisted type screened
cable where the screen covers at least 85% of the cable surface area, designed with low impedance to HF signals. Installation
of a standard cable within a suitable steel or copper tube is also acceptable - in this case, ensure that metal tube is adequately
grounded.
6
The cable shield should be terminated at the motor end using an EMC type gland allowing connection to the motor body through
the largest possible surface area. The shield must also be terminated at the drive end, as close as practically possible to the drive
output terminals. Where drives are mounted in a steel control panel enclosure, the cable screen may be terminated directly to the
control panel backplate using a suitable EMC clamp or gland fitted as close to the drive as possible. The drive earth terminal must
also be connected directly to this point, using a suitable cable which provides low impedance to high frequency currents. For IP55
and IP66 drives, connect the motor cable shield to the gland plate or internal ground clamp.
7
A cable suitable for fixed installation with relevant mains voltage with a concentric protection wire. Installation of a standard cable
within a suitable steel or copper tube is also acceptable.
Control Cable
8
A shielded cable with low impedance shield. Twisted pair cable is recommended for analog signals.
4.13.3. Enclosed Drives Recommended Cable Connections
IP55
IP66
L1 L2 L3
U V W
+DC BR -DC
For Best-Practice use 360°
bonding IP66 (or higher)
EMC cable gland shielded
to drive chassis.
U V W
4.14. Safe Torque Off
Safe Torque OFF will be referred to as “STO” through the remainder of this section.
4.14.1. Responsibilities
The overall system designer is responsible for defining the requirements of the overall “Safety Control System” within which the drive
will be incorporated; furthermore the system designer is responsible for ensuring that the complete system is risk assessed and that the
“Safety control System” requirements have been entirely met and that the function is fully verified, this must include confirmation testing
of the “STO” function before drive commissioning.
The system designer shall determine the possible risks and hazards within the system by carrying out a thorough risk and hazard
analysis, the outcome of the analysis should provide an estimate of the possible hazards, furthermore determine the risk levels and
identify any needs for risk reduction. The “STO” function should be evaluated to ensure it can sufficiently meet the risk level required.
4
Elec
trical Installation