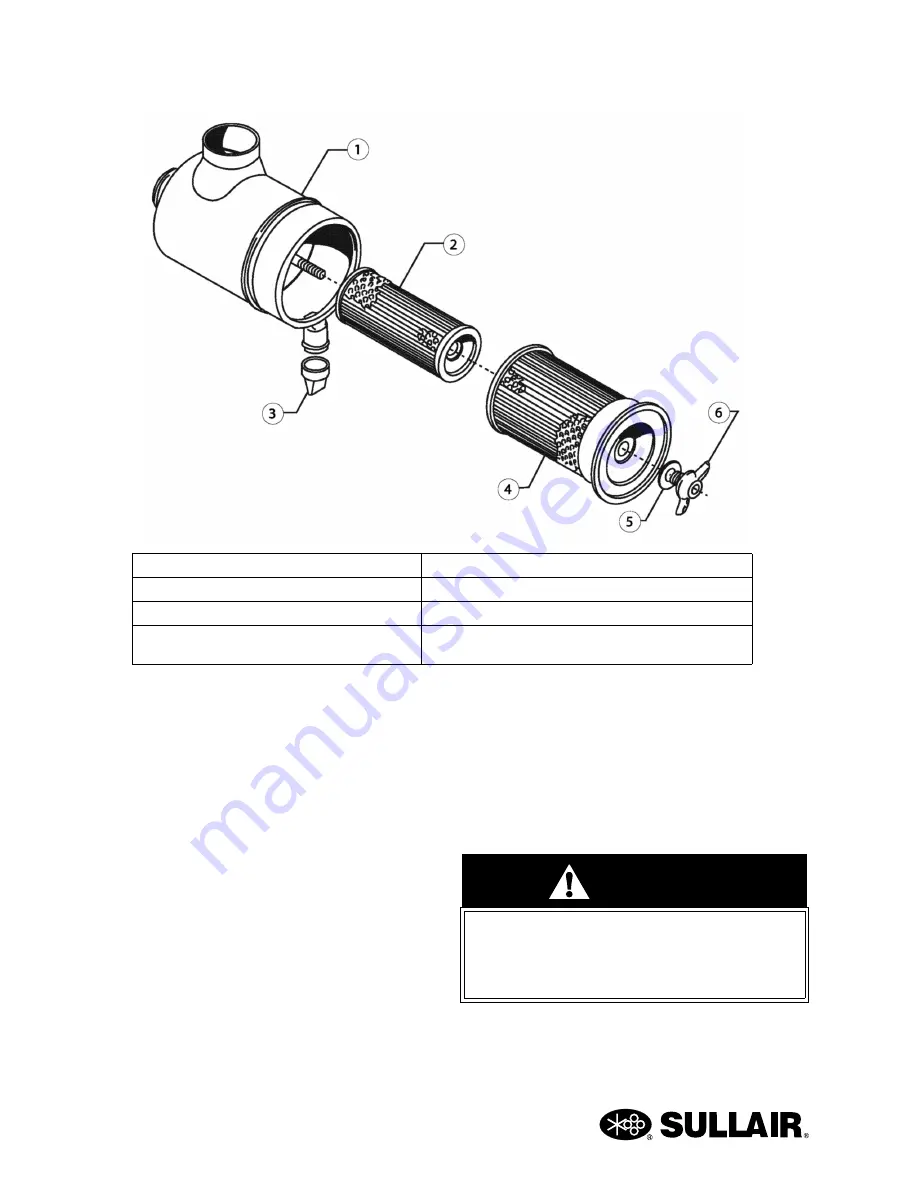
1600C LP USER MANUAL
SECTION 5
62
ELEMENT INSPECTION
1. Place a bright light inside the element to
inspect for damage or leak holes. Concen-
trated light will shine through the element
and disclose any holes.
2. Inspect all gaskets and gasket contact sur-
faces of the housing. Should faulty gaskets
be evident, correct the condition immedi-
ately.
3. If the clean element is to be stored for later
use, it must be stored in a clean container.
4. After the element has been installed, inspect
and tighten all air inlet connections prior to
resuming operation.
PRIMARY ELEMENT REPLACEMENT
1. Place the element in position over the sec-
ondary element.
2. Install the cover with clean-out port pointing
down. Clamp in place using all latches
located on canister.
Figure 5-4: Air Filter Assembly
1. Housing
4. Primary Element*
2. Secondary Element**
5. Sealing Washer
3. Dust Collector
6. Wing Nut
** Secondary replacement element, P/N
11
02250051-239
* Primary replacement element, P/N 02250051-238
CAUTION
DO NOT strike elements against any hard
surface to dislodge dust. This will damage
the sealing surfaces and possibly rupture
the elements.
Содержание 02250175-949 R01
Страница 2: ......
Страница 20: ...SECTION 1 20 ...
Страница 30: ...1600C LP USER MANUAL SECTION 2 30 2 9 PIPING INSTRUMENTATION DIAGRAM COMPRESSOR 02250176 713 R03 S1 ...
Страница 32: ...1600C LP USER MANUAL SECTION 2 32 2 10 PIPING INSTRUMENTATION DIAGRAM ENGINE 02250176 713 R03 S2 ...
Страница 42: ...42 NOTES ...
Страница 46: ...1600C LP USER MANUAL SECTION 3 46 3 6 ID TANDEM AXLE 02250175 070 r00 ...
Страница 48: ...1600C LP USER MANUAL SECTION 3 48 3 8 ID 4 WHEEL 02250175 073 r00 ...
Страница 50: ...1600C LP USER MANUAL SECTION 3 50 3 9 ID WITHOUT RUNNING GEAR 02250175 075 r01 ...
Страница 52: ...NOTES 52 ...
Страница 56: ...NOTES 56 ...
Страница 68: ...68 NOTES ...
Страница 73: ...NOTES ...