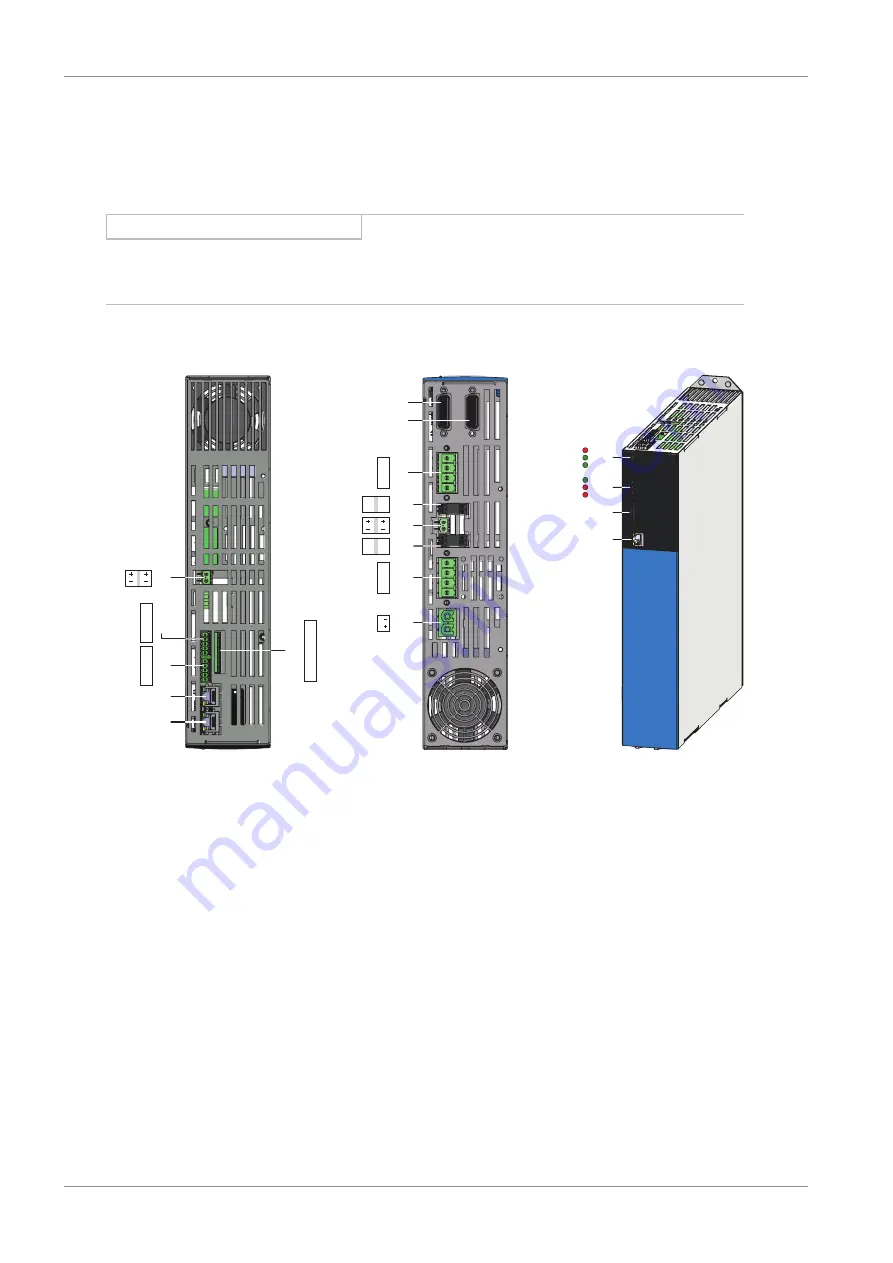
10 | Connection
STOBER
116
02/2019 | ID 442728.05
10.5
Drive controller
The following section contains detailed information about the terminals and the correct
connection of the drive controller.
Information
For UL-compliant operation: The connections marked with PE are intended solely for the
functional grounding.
10.5.1
Overview
1
3
2
4
5
7
6
8
5
3
4
2
1
X12
X103
X101
2
1
4
5
6
3
15
17
18
16
11
14
9
1 0
12
13
8
6
5
7
X22
X20A
X2A
X2B
X20B
8
7
7
8
D
D
X201
X200
X4A
X4B
PE
V
W
U
PE
V
W
U
5
3
4
2
1
6
5
X700
X9
X11
X300
Fig. 30: Connection overview using the example of the SI6A162
Top of the device
Bottom of the device
Front of the device
1
X11: 24 V
DC
supply
7
X4B: Encoder B (only for
double-axis controllers)
15
3 diagnostic
LEDs for communication
and safety technology
2
X103: BE6 – BE9
8
X4A: Encoder A
16
3 diagnostic LEDs for
drive controller
3
X12: STO via terminals
(only for SR6 option)
9
X20B: Motor B (only for double-
axis controllers)
17
X700: SD slot
4
X101: BE1 – BE4
10
X2B: Brake B (pin 5/6)
and temperature sensor B (pin
7/8); (only for double-axis
controllers)
18
X9: Ethernet service
interface
5
X201: EtherCAT Out /
PROFINET
11
X300: Brake 24 V
DC
supply
6
X200: EtherCAT In /
PROFINET
12
X2A: Brake A (pin 5/6)
and temperature sensor A (pin
7/8)
13
X20A: Motor A
14
X22: DC link connection