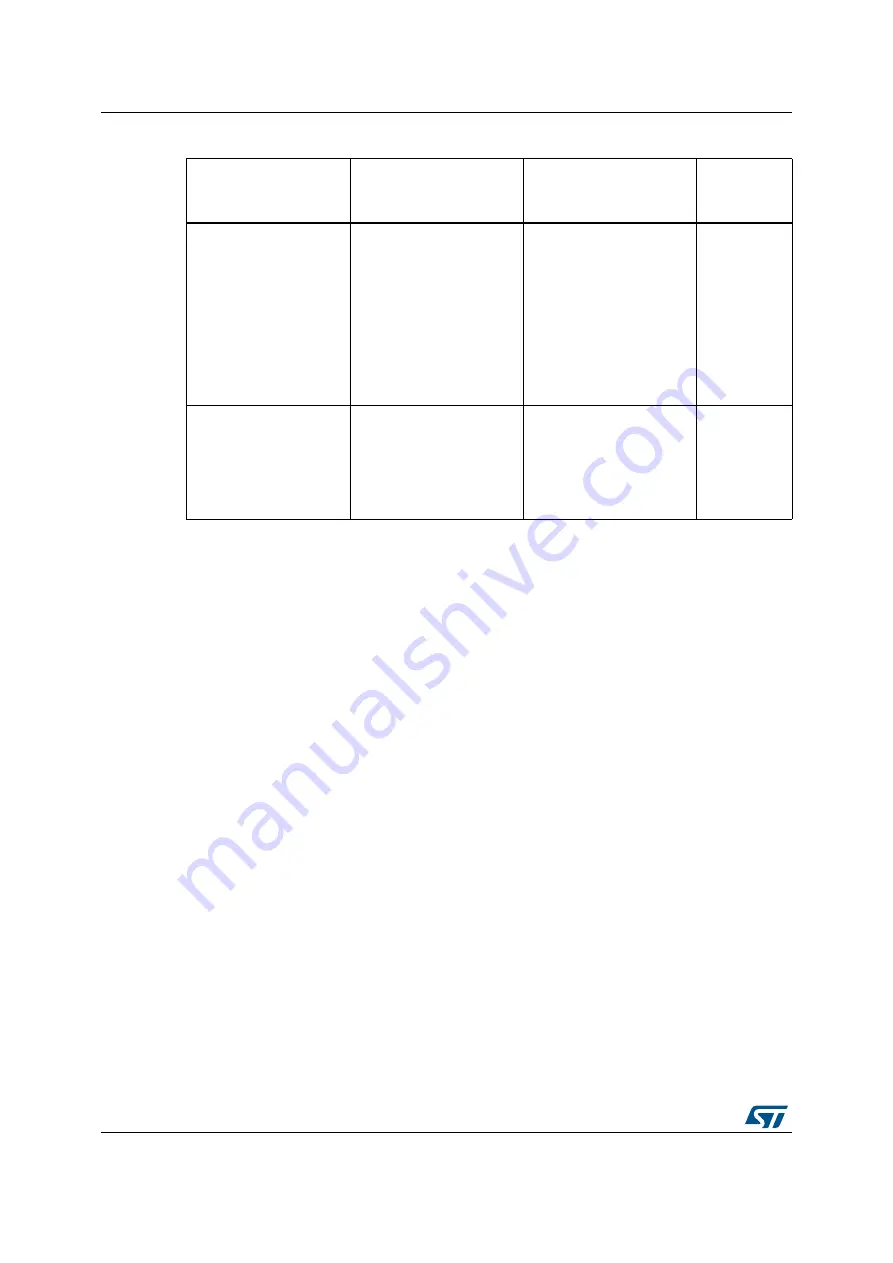
Analog-to-digital converters (ADC)
RM0365
289/1080
DocID025202 Rev 7
•
Start-of-conversion can be initiated:
–
by software for both regular and injected conversions
–
by hardware triggers with configurable polarity (internal timers events or GPIO
input events) for both regular and injected conversions
•
Conversion modes
–
Each ADC can convert a single channel or can scan a sequence of channels
–
Single mode converts selected inputs once per trigger
–
Continuous mode converts selected inputs continuously
–
Discontinuous mode
•
Dual ADC mode (STM32F302xB/C/D/E only)
•
Interrupt generation at the end of conversion (regular or injected), end of sequence
conversion (regular or injected), analog watchdog 1, 2 or 3 or overrun events
•
3 analog watchdogs per ADC
•
ADC supply requirements: 1.80 V to 3.6 V
•
ADC input range: V
REF
–
≤
V
IN
≤
V
REF+
shows the block diagram of one ADC.
Table 82. ADC internal channels summary
Product
ADC1
ADC2
Total of
internal ADC
channels
STM32F302xB/C/D/E
– 1 channel connected to
temperature sensor.
– 1 channel connected to
VBAT/2
– 1 channel connected to
VREFINT
– 1 channel connected to
OPAMP1 reference
voltage output
(VREFOPAMP1).
– 1 channel connected to
temperature sensor.
– 1 channel connected to
VBAT/2
– 1 channel connected to
VREFINT.
– 1 channel connected to
OPAMP2 reference
voltage output
(VREFOPAMP2).
5
STM32F302x6/8
– 1 channel connected to
temperature sensor.
– 1 channel connected to
VBAT/2
– 1 channel connected to
VREFINT
-
3