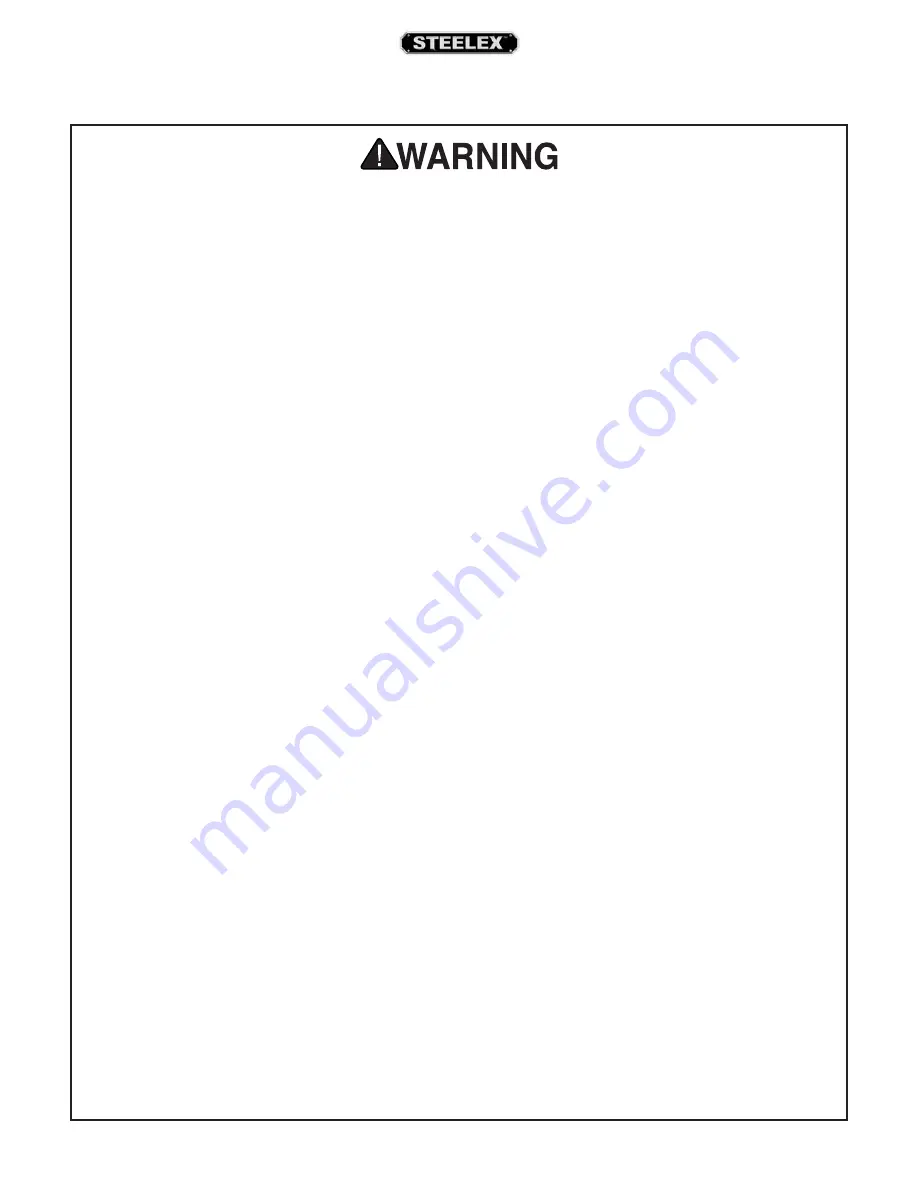
ST1008 Mini Wood Lathe
-9-
Additional Safety for Wood Lathes
MAIN INJURY HAZARDS: Death or crushing injury from getting entangled in rotating spindle or
workpiece; death, blindness, or broken bones from being struck by a workpiece that breaks apart
or comes loose during rotation, turning tool kickback, or flying wood chips. To minimize your risk of
these hazards, always heed the following warning information:
EYE/FACE PROTECTION. Always wear a face shield
and safety glasses when operating lathe.
PROPER APPAREL. Do not wear gloves, necktie or
loose clothing. Keep long hair away from rotating
spindle.
SPEED RATES. Select correct spindle speed for
workpiece size, type, shape, and condition. Use
low speeds when roughing or when turning large,
long, or non-concentric workpieces. Allow spindle to
reach full speed before turning.
NEW SETUPS. Test each new setup by starting spin-
dle rotation at the lowest speed and standing to the
side of the lathe until workpiece reaches full speed
and you can verify safe rotation.
ROUGHING. Use correct tool. Take light cuts, use
low speeds, and firmly support tool with both hands.
SHARP TOOLS. Only use sharp turning tools— they
cut with less resistance than dull tools. Dull turning
tools can catch or grab and pull your hands into the
rotating workpiece.
STOPPING SPINDLE. Always allow spindle to com-
pletely stop on its own. Never put hands or another
object on spinning workpiece.
ADJUSTMENT/MAINTENANCE. Make sure wood
lathe is turned OFF, disconnected from power, and
all moving parts are completely stopped before
doing adjustments or maintenance.
MEASURING WORKPIECE. Only measure
workpiece after it has stopped. Trying to measure
a spinning workpiece increases entanglement risk.
SANDING/POLISHING. To reduce entangle-
ment risk, remove tool rest before sanding. Never
completely wrap sandpaper around workpiece.
INTEGRITY OF STOCK. Verify each workpiece is free
of knots, splits, nails, or foreign material to ensure it
can safely rotate on spindle without breaking apart
or causing tool kickback.
WORKPIECE PREPARATION. Before mounting, cut
off waste portions with a bandsaw or other tool
to ensure workpiece has no large edges to catch
turning tool, and it will rotate without dangerous
wobbling.
SECURING LOCKS. Verify tool rest, headstock, and
tailstock are secure before turning lathe ON.
SECURE WORKPIECE. An improperly secured
workpiece can fly off spindle with deadly force.
Use proven setup techniques and always verify
workpiece is well-secured before starting lathe. Only
use high-quality fasteners with non-tapered heads
for faceplate attachment.
TOOL SUPPORT. An improperly supported tool
may be grabbed or ejected. Adjust tool rest approx-
imately
1
⁄
4
" away from workpiece and
1
⁄
8
" above
workpiece center line to provide proper support
for turning tool. Firmly hold turning tool with both
hands against tool rest.
TOOL KICKBACK. Occurs when turning tool is eject-
ed from workpiece with great force, striking operator
or bystanders. Commonly caused by tool usage, or
improper machine setup or tool rest adjustment.
ADJUSTMENT TOOLS. Remove all chuck keys,
wrenches, and adjustment tools before turning lathe
ON. A tool left on the lathe can become a deadly
projectile when spindle is started.
SAFE CLEARANCES. Before starting spindle, verify
workpiece has adequate clearance by hand-rotating
it through its entire range of motion.