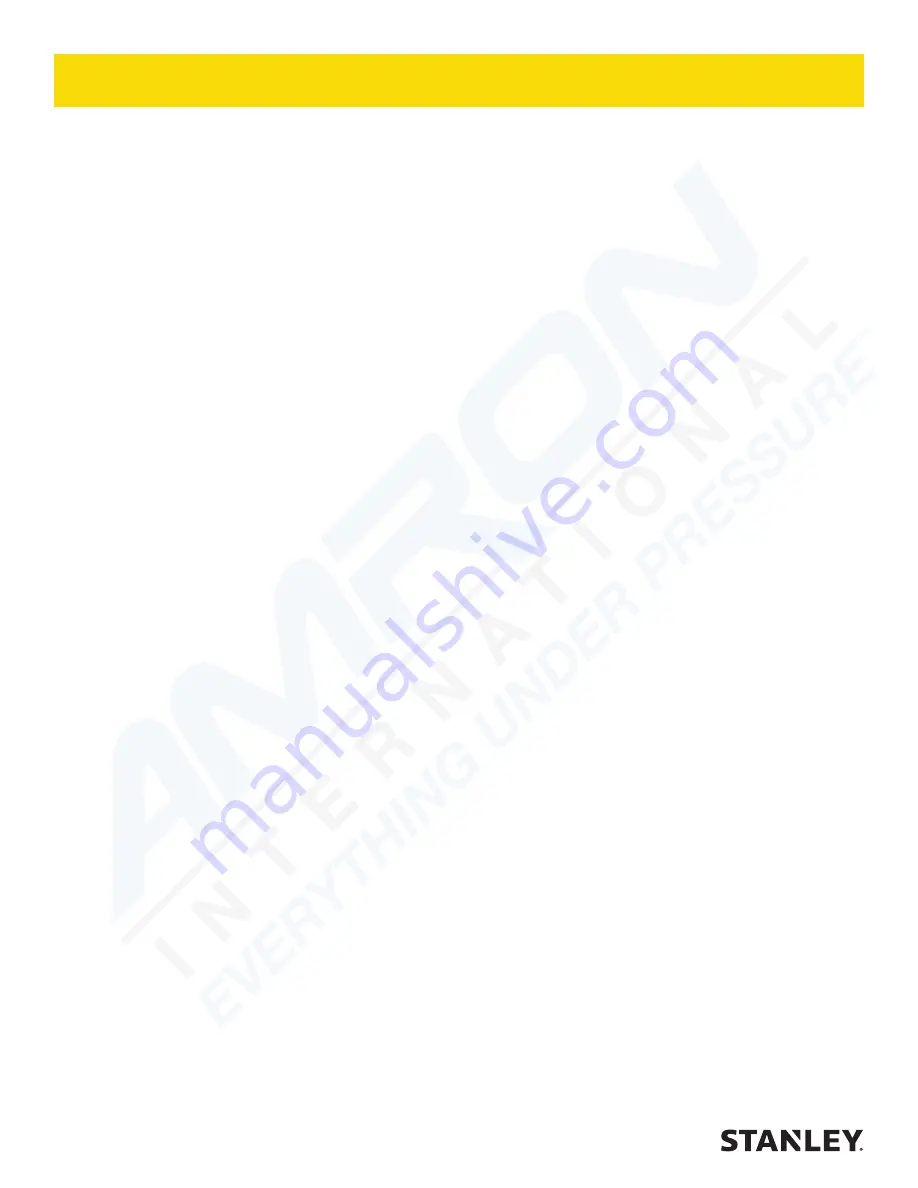
22 ► CS11
Service Manual
Good maintenance practice keeps the tool on the job
and increase its service life.
Keep the hydraulic fluid clean at all times. Contaminated
hydraulic fluid causes rapid wear and/or failure of
internal parts.
Follow the procedure contained in “HYDRAULIC
SYSTEM REQUIREMENTS” on page 13, to ensure
peak performance from the tool.
Never disassemble the tool unless proper troubleshooting
procedures have isolated the problem to an internal part.
Disassemble it only to the extent necessary to replace
the defective part.
KEEP CONTAMINANTS SUCH AS
DIRT AND GRIT AWAY FROM INTERNAL PARTS AT
ALL TIMES.
Always determine and correct the cause of the problem
prior to assembly. Further wear and tool failure can
result if the original cause is not corrected.
PRIOR TO ASSEMBLY
Clean exterior of the tool.
Obtain the seal kit (part number 21443 or 21444) so all
seals exposed during disassembly can be re placed.
Ensure that all seals that were exposed have been
replaced with new parts.
Apply clean grease or O-ring lubrication to all parts
during reassembly.
Note: For orientation of parts identified in
the following procedures, see “CS11 PARTS
1.
Check all parts for evidence of excessive wear,
scoring or obvious damage. Pay particular attention
to seal and other running surfaces, look ing for
scratches or other signs of fluid contami nation. Dirty
or water contami nated fluid can cause scratches on
running com ponent surfaces.
2.
Examine all exposed seals and O-rings for worn
spots or damage caused by overheating or ingestion
of contaminants. Although all exposed O-rings and
seals must be replaced during assembly of the unit,
this inspection should be performed to help identify
related faulty components and the cause of an
experienced or potential malfunction.
3. All components exhibiting excessive wear or deep
scratches can usually be touched up using an emery
cloth.
Thoroughly clean all parts before assembly.
4.
Apply clean grease or O-ring lubricant to all close
fitting parts and seals during assembly.
ON-OFF VALVE DISASSEMBLY AND
REASSEMBLY
DISASSEMBLY
1.
Drive out the 1/4-inch roll pin securing the trigger
to the valve handle assembly. Depress the safety
catch and remove the triggers through the bottom of
the valve handle.
Note: It is not always necessary to drive the roll pins
completely out of valve handle to allow re moval of
parts.
The safety catch can be removed at this time
by driving out the 3/16-inch roll pin with a 5 mm
diameter punch. It is not necessary to re move the
safety catch to service the On/Off valve.
2.
Remove the valve cap from the top of the handle.
Remove the O-ring from valve cap bore.
3. Pull the On/Off valve out through the top of the valve
handle.
4.
Remove the port plug from the bottom of the valve
handle. The coil spring will drop out in your hand.
5. Clean and inspect the valve and its bore in the
handle carefully. The valve and bore should have
a polished appearance without scoring or deep
scratches. Excessive wear indicates contaminated
oil in the system.
REASSEMBLY
1.
Lubricate and install the O-ring in the valve cap bore.
2.
Push the valve cap onto the valve stem, then
thread the assembly into the top of the valve handle
assembly.
3.
Install the coil spring and the port plug into the
bottom of the valve handle.
Note: Open and Closed Center valves are
interchangeable.
4.
Replace the safety catch (if removed previ ously).
Place the torsion spring on the boss of the safety
catch with the spring tab on the top of and facing
the back of the catch, as shown in “CS11 PARTS
5. Place the safety catch in the valve handle and align
the holes using a 3/16 inch/5 mm diameter punch.
6. Install the 3/16
×
1-3/8 inch roll pin.
7.
Push down on the spring tab until it snaps in place
under the safety catch.
8.
Depress the safety catch and slide the trigger
through the bottom of the handle.
9. Line up the trigger and manual oiler trigger with the
SERVICE