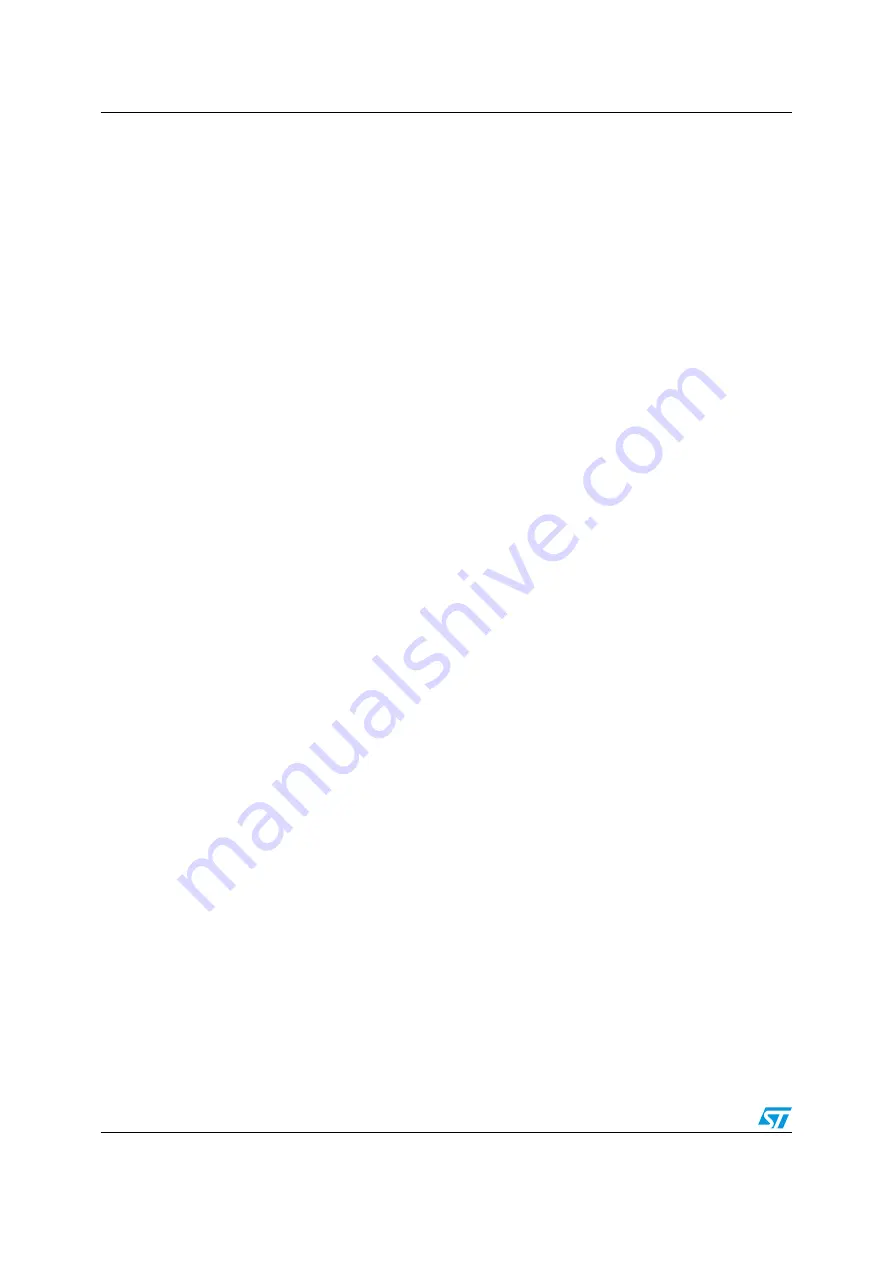
Safety and operating instructions
UM0933
10/16
Doc ID 17386 Rev 1
implemented using two ceramic thermostats, one mounted on the power switches heatsink
and one on the output power diodes heatsinks.
●
Features
–
Welding machine based on asymmetric forward double switch converter
–
Power stage based on IGBT or MOSFET
–
185 VAC
rms
< VINAC
rms
<265 VAC
rms
–
Lout max 135, regulated from 50 A
–
Auxiliary flyback power supply based on the VIPer16
–
L6386E gate driver
–
Analog control based on the TSM102 op amps + comparators
–
Output short-circuit protection
–
Hot start function
2.7 STEVAL-ISW001V1
circuital
description
In
the electronic schematic of the power board is shown.
Starting from the main supply input, a common mode filter and a power diode bridge can be
found. After the bridge, a DC bus, filtered by the electrolytic capacitor C35 and C36, is
available.
The auxiliary power supply, based on the VIPer16, is based on a flyback topology and can
supply two galvanic insulated low voltage supplies. One of these two low voltage sources is
connected to the common ground and used to supply all the logic and analog circuit present
on the control board, plus the gate driver. The insulated output (+15 V) is used to supply the
bootstrap section of the L6386 driver. In this way, a safe high side supply is assured.
The gate driver section is based on the L6386 chip. Using the internal comparator of the
L6386, also a hardware current protection has been implemented. The current, on the
primary side of the insulation transformer, measured by the current transformer on the
power board, after a partition through R48 and R49, is connected to pin 6. Pin 6 (Cin) is the
input of the internal comparator. If the voltage level on this pin rises to 0.5 V, the comparator
triggers, pulling down the DIAG pin. This pin is connected to the pin shutdown of the driver,
so a valid and fast current protection is implemented. In order to have a good current
capability and noise immunity on the gate of the power switches, the two outputs of the
driver (Hvg and Lvg) are buffered by two push-pulls. Two STS01DTP06s are used for this
purpose. The expected maximum peak current on the primary side is about 45 A at 135 A at
welding current. In these conditions two paralleled power switches are required. Two ultra
fast power diodes D25 and D32 are used to freewheel the magnetization current of the
transformer during the T
OFF
of the PWM. For this reason the maximum duty cycle cannot
surpass 50 % on this topology.
The power rectifier can be found on the secondary side of the power transformer made up of
ultra fast power diodes. An insulated sensing of the output voltage is implemented to identify
a short-circuit condition. In fact, during a normal arc condition a voltage between 18 and 25
V should be present on the output. The optocoupler senses the output voltage and gives
information to the control board. The trimmer R60 is useful to set a proper voltage threshold
to the optocoupler according to length and cross section of the cable used to connect the
board to the torch and clamp.
www.BDTIC.com/ST