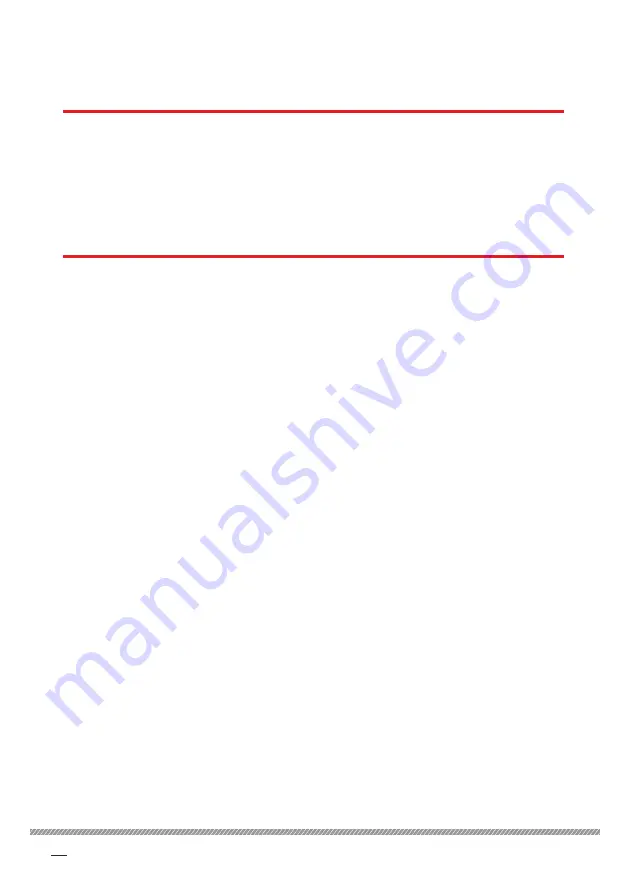
16
MAX preset adjustment
9
9 MAX preset adjustment
MAX preset adjustment
9.1 ARMATURE VOLTAGE control mode (speed control)
Refer to "Figure 18 Jumper and link positions" on page 14.
When using AV mode, the
MAX
preset operates as a speed control:
•
With the top and bottom proportional gain links fitted, the
MAX
preset range
adjustment is ±4 V to ±25 V for a 5 V speed demand.
•
With the top and bottom proportional gain links NOT fitted, the
MAX
preset
adjustment is from ±8 V to ±50 V.
9.2 PID feedback (gain control)
When using PID feedback, the
MAX
preset becomes a gain control.
Содержание 200XLV
Страница 6: ......