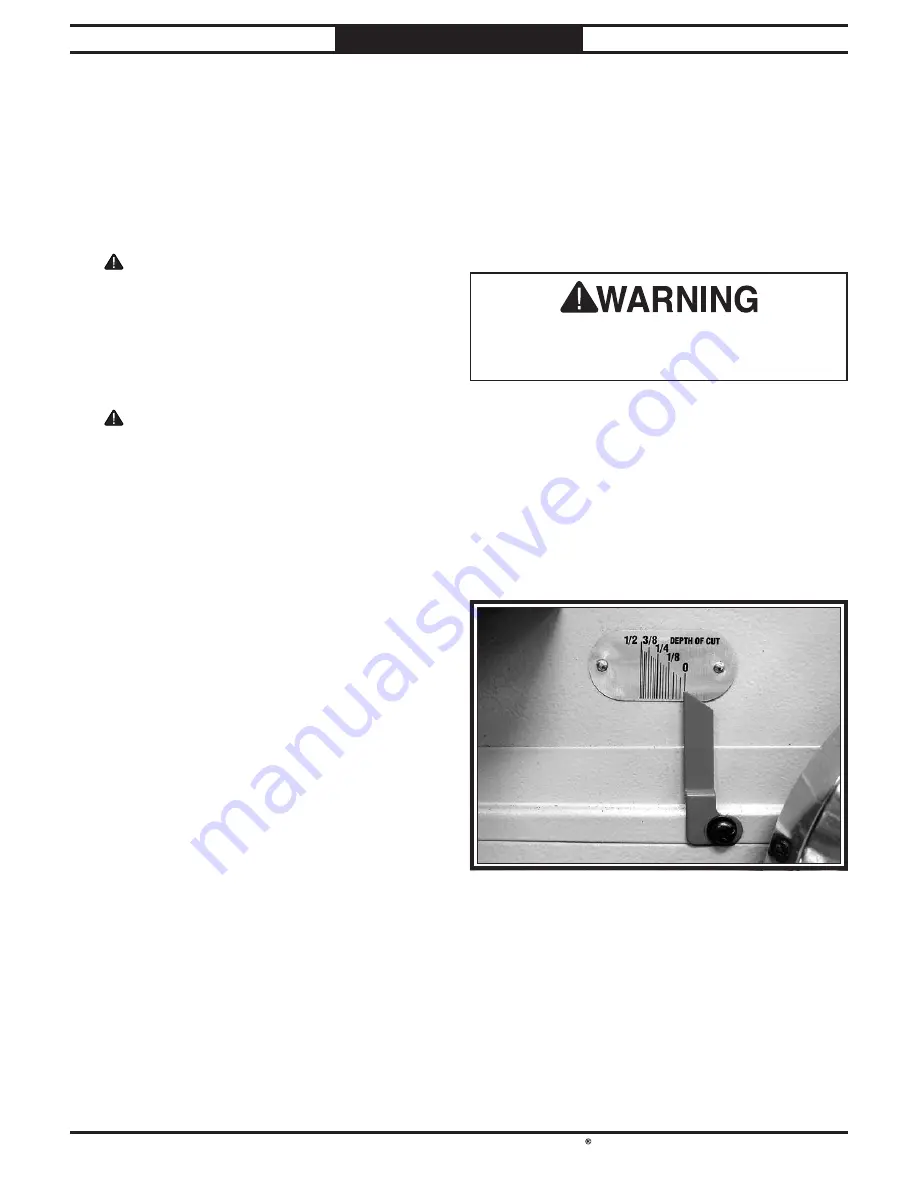
4.
Set fence to 90° and near front of jointer,
so amount of exposed cutterhead in front of
fence matches size of desired rabbet.
5.
Start jointer.
6.
Place workpiece firmly against fence and
infeed table.
CAUTION:
To ensure workpiece remains
stable during cut, concave sides of workpiece
must face toward table and fence.
7.
Feed workpiece completely across cutterhead
while keeping it firmly against fence and
tables during entire cut.
CAUTION:
Keep hands at least 4"
away from cutterhead during the entire
cut. Instead of allowing a hand to pass
directly over cutterhead, lift it up and
over cutterhead, and safely reposition it
on the outfeed side to continue supporting
workpiece. Use push blocks whenever
practical to further reduce risk of accidental
hand contact with cutterhead.
8.
Repeat
Step 7 until rabbet is cut to depth.
9.
Re-install cutterhead guard if removed in
Step 3.
DO NOT exceed
1
⁄
8
" cut per pass on this
machine or the risk of kickback and serious
injury will be greatly increased!
Figure 24. Model SB1091 depth scale.
South Bend Tools
For Machines Mfd. Since 10/20
Model SB1091
-29-
O P E R A T I O N
Setting Depth of Cut
The depth of cut on a jointer affects the amount
of material removed from the bottom of the
workpiece as it passes over the cutterhead.
The depth of cut is set by adjusting the height of
the infeed table relative to the outfeed table and
cutterhead inserts at top dead center (TDC).
To set depth of cut on jointer:
1.
Loosen infeed table lock and rotate
handwheel until depth scale on front of
jointer (see Figure 24) indicates desired
depth of cut.
Note:
The depth scale can be calibrated
or "zeroed" if it is not accurate. (Refer to
Calibrating Infeed Table on Page 40).
2.
Set infeed table positive stops according to
Setting Infeed Table on Page 40.
3.
Tighten infeed table lock before beginning
jointer operations.
Содержание SB1091
Страница 60: ...southbendtools com Printed In Taiwan KS21028 ...