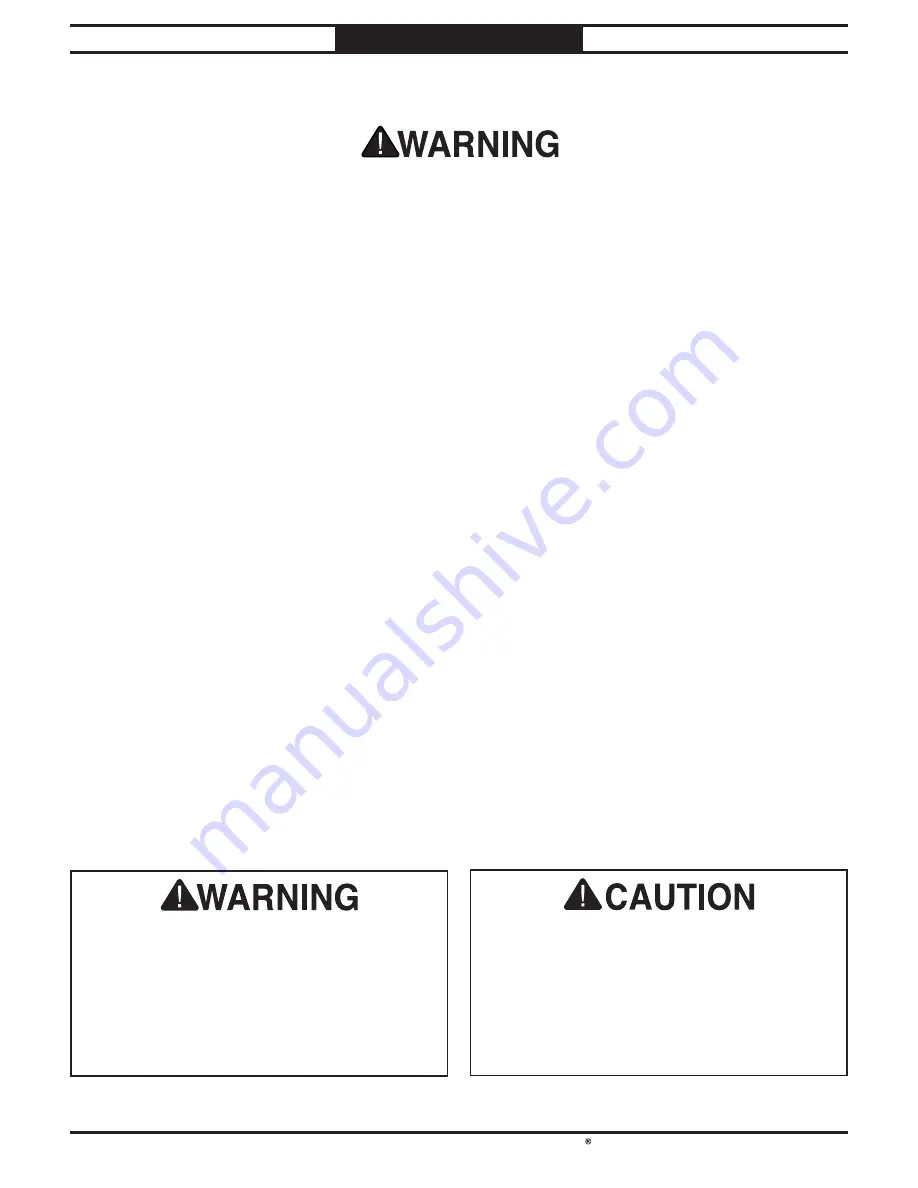
South Bend Tools
For Machines Mfd. Since 11/21
Model SB1125
-9-
S A F E T Y
Additional Drill Press Safety
Drilling Preparation.
To avoid loss of drilling control
or bit breakage, only drill into a flat surface
that is approximately perpendicular to bit.
Clear table of all objects before starting spindle.
Never start spindle with bit pressed against
workpiece.
Securing Table and Headstock.
To avoid loss of
control leading to accidental contact with tool/
bit, tighten all table and headstock locks before
operating drill press.
Correct Spindle Speed.
Using wrong spindle speed
can cause bits/cutting tools to break and strike
operator or bystanders. Follow recommended
speeds and feeds for each size/type of bit/cutting
tool and workpiece material.
Securing Bit/Cutting Tool.
Firmly secure bit/
cutting tool in chuck so it cannot fly out of
spindle during operation or startup.
Inspecting Bit/Cutting Tool.
Damaged bits/cutting
tools may break apart during operation and
hit operator or bystanders. Dull bits/cutting
tools increase cutting resistance and are more
likely to grab and spin/throw workpiece. Always
inspect bits/cutting tools for sharpness, chips, or
cracks before each use. Replace dull, chipped, or
cracked bits/cutting tools immediately.
Eye/Face/Hand Protection.
Flying chips
created by drilling can cause eye injuries
or blindness. Always wear a face shield
in addition to safety glasses. Always keep
hands and fingers away from drill bit/cutting
tool. Avoid awkward hand positions, where
a sudden slip could cause hand to move into
bit/cutting tool.
Avoiding Entanglement.
DO NOT wear loose
clothing, gloves, or jewelry. Tie back long hair.
Keep all guards in place and secure. Always
allow spindle to stop on its own. DO NOT stop
spindle using your hand or any other object.
Removing Adjustment Tools.
Chuck key,
wrenches, and other tools left in spindle chuck
or on machine can become deadly projectiles if
thrown by rotating spindle. Remove all loose
items or tools used on spindle immediately after
use.
Workpiece Control.
An unsecured workpiece
may unexpectedly shift, spin out of control,
or be thrown if bit/cutting tool “grabs” during
operation. Clamp workpiece to table or in
table-mounted vise, or brace against column
to prevent rotation. NEVER hold workpiece by
hand during operation. NEVER start machine
with bit/cutting tool touching workpiece; allow
spindle to gain full speed before drilling.
Serious injury or death can occur from getting clothing, jewelry, or long hair entangled in rotating
spindle or bit/cutting tool. Contact with rotating bit/cutting tool can result in severe cuts or
amputation of fi ngers. Flying metal chips can cause blindness or eye injuries. Broken bits/cutting
tools, unsecured workpieces, chuck keys, or other adjustment tools thrown from rotating spindle
can strike nearby operator or bystanders with deadly force. To reduce the risk of these hazards,
operator and bystanders MUST completely heed hazards and warnings below.
Like all machinery there is a potential danger
when operating this machine. Accidents are
frequently caused by lack of familiarity or
failure to pay attention. Use this machine with
respect and caution to decrease the risk of
operator injury. If normal safety precautions
are overlooked or ignored, serious personal
injury may occur.
No list of safety guidelines can be complete.
Every shop environment is different. Always
consider safety first, as it applies to your
individual working conditions. Use this and
other machinery with caution and respect.
Failure to do so could result in serious
personal injury, damage to equipment, or poor
work results.
Содержание SB1125
Страница 56: ...southbendtools com Printed In Taiwan CS22121...