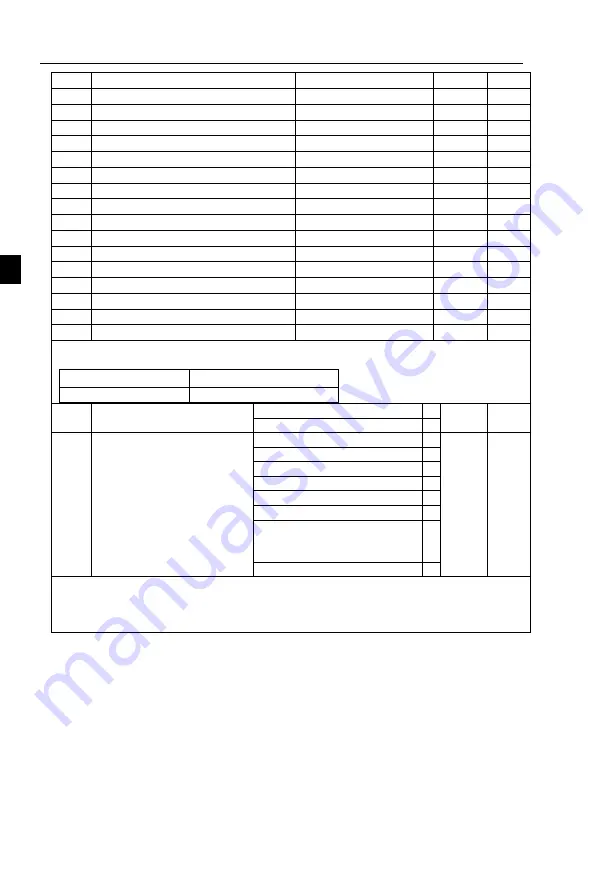
Chapter 5 Function parameter
110
Ch
ap
ter 5
E1.33 7 stage ac/deceleration time selection
0 to 3
0
☆
E1.34 8 stage running time T8
0.0s(h) to 6500.0s(h)
0.0s(h)
☆
E1.35 8 stage ac/deceleration time selection
0 to 3
0
☆
E1.36 9 stage running time T9
0.0s(h) to 6500.0s(h)
0.0s(h)
☆
E1.37 9 stage ac/deceleration time selection
0 to 3
0
☆
E1.38 10 stage running time T10
0.0s(h) to 6500.0s(h)
0.0s(h)
☆
E1.39 10 stage ac/deceleration time selection
0 to 3
0
☆
E1.40 11 stage running time T11
0.0s(h) to 6500.0s(h)
0.0s(h)
☆
E1.41 11 stage ac/deceleration time selection
0 to 3
0
☆
E1.42 12 stage running time T12
0.0s(h) to 6500.0s(h)
0.0s(h)
☆
E1.43 12 stage ac/deceleration time selection
0 to 3
0
☆
E1.44 13 stage running time T13
0.0s(h) to 6500.0s(h)
0.0s(h)
☆
E1.45 13 stage ac/deceleration time selection
0 to 3
0
☆
E1.46 14 stage running time T14
0.0s(h) to 6500.0s(h)
0.0s(h)
☆
E1.47 14 stage ac/deceleration time selection
0 to 3
0
☆
E1.48 15 stage running time T15
0.0s(h) to 6500.0s(h)
0.0s(h)
☆
E1.49 15 stage ac/deceleration time selection
0 to 3
0
☆
Multi-speed operation and ac-/deceleration time pair selection 0 to 3, corresponding to the
function codes:
0: F0.13, F0.14
2: F7.10, F7.11
1: F7.08, F7.09
3: F7.12, F7.13
E1.50 Simple PLC run-time unit
S(seconds)
0
0
☆
H(hours)
1
E1.51
Multi-stage command 0
reference manner
Function code E1.00 reference
0
0
☆
Analog AI1 reference
1
Analog AI2 reference
2
Panel potentiometer setting
3
High-speed pulse setting
4
PID control setting
5
Keyboard set frequency (F0.01)
setting, UP/DOWN can be
modified
6
Analog AI3 reference
7
This parameter determines the multi-stage command 0 reference channel.
The multi-stage command 0 not only can select E1.00, but also there are a variety of other
options so as to facilitate switching between the multi-stage command and the other reference
manner.
5-2-17.
PID function: E2.00-E2.32
PID control is a commonly used method of process control, a closed loop system is formed by
the proportional, integral and differential operation of difference between the controlled value
feedback signal and target value signal and by adjusting the inverter output frequency so as to
stabilize the controlled value at the position of the target value.Suitable for flow control, pressure
control and temperature control and other process control applications.