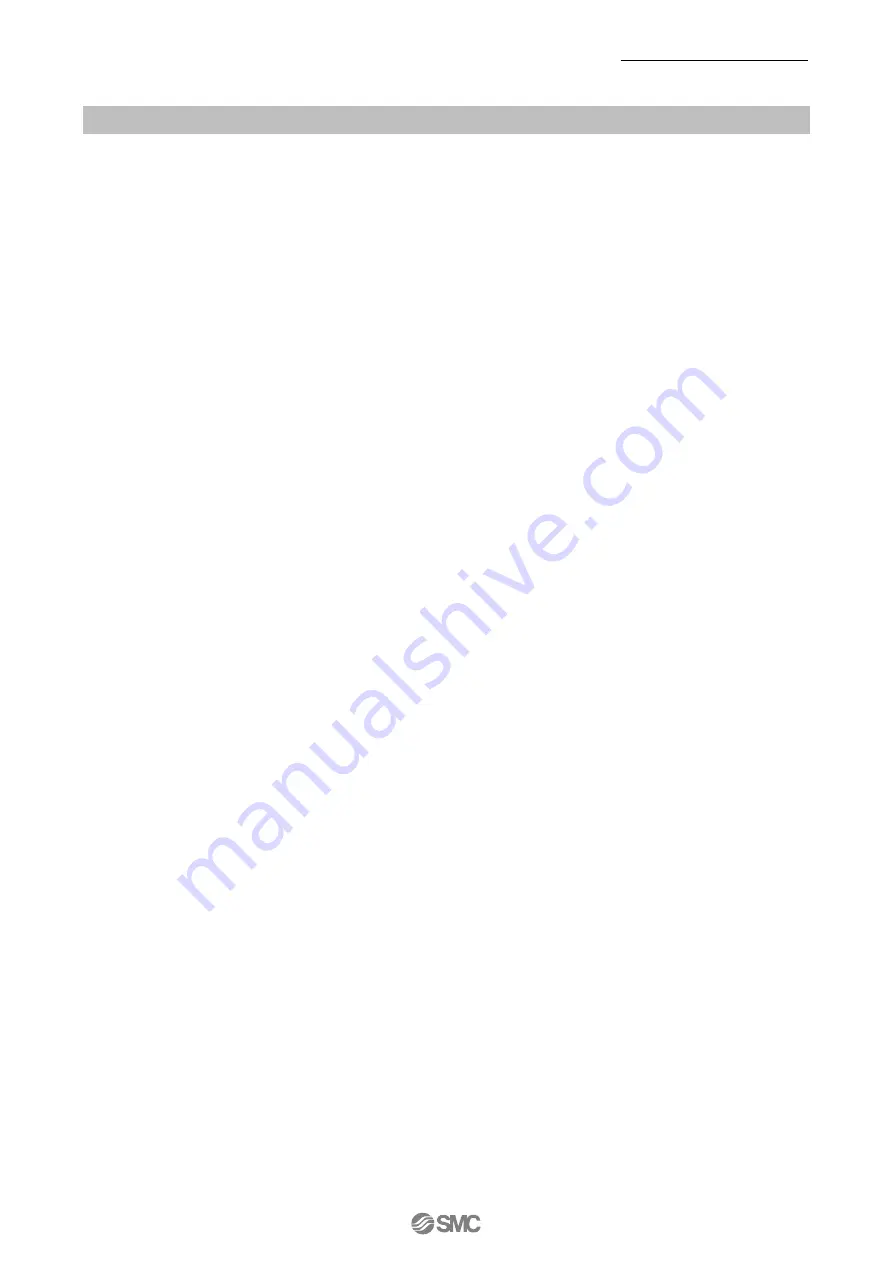
Doc. No. ZQ-OM01301-A
- 16 -
3.4.4 Precautions for air tubes
1) Route tubes to prevent twisting, tension, moment loads, vibration or impact from being
applied to the tubes. Failing to route correctly can cause damage to the fittings and will
crush or burst tubing, or it may come out.
2) Piping to the product is assumed to be static piping. If the tube moves, it may wear,
elongate, or tear due to tensile forces, or disconnect from the fitting. Ensure the tube is in a
static condition at all times before use.
3) Do not lift the product by holding the tubing after piping. This may lead to damage of the
filter case or One-touch fitting.
4) Before piping is connected, it should be thoroughly flushed with air, or washed to remove
chips, cutting oil and other debris from inside the pipe. Otherwise it can cause damage or
malfunction.
5) When connecting tubing, consider factors such as changes in the tubing length due to
pressure, and leave enough slack. Failure to do so may result in fitting breakage or
detachment of the tubing.
Refer to Fittings & Tubing Precautions from 1 to 4 shown in Best Pneumatics 6 on SMC’s
website (URL) for the recommended piping conditions.
3.5
Wiring
3.5.1 Precautions for Wiring
1) Do not pull the lead wire for the solenoid valve or pressure switch forcefully or lift the
product by the lead wire. Otherwise damage to the solenoid valve or internal parts can
result, causing malfunction or causing the connector to come out.
2) Avoid repeatedly bending or stretching the lead wires, or placing a heavy load or applying
force to them. Repetitive bending stress or tensile stress can cause the sheath of the wire to
peel off. If the lead wire can move, secure it near the body of the product. The
recommended bend radius of the lead wire is 6 times the outside diameter of the sheath, or
33 times the outside diameter of the insulation material, whichever is larger. Replace the
damaged lead wire with a new one.
3) Wire correctly. Incorrect wiring can cause malfunction or breakage of the solenoid valve or
pressure switch.
4) Do not perform wiring while the power is on. The internal parts of the solenoid valve or
pressure switch may get damaged and malfunction.
5) Do not route wires and cables together with power or high voltage cables. Route the wires
of the product separately from power or high voltage cables in order to avoid noise or surge
entering the signal line from the power or high voltage line.
6) Verify the insulation of wiring. Poor insulation (interference with other circuits, poor
insulation between terminals etc.) can apply excessive voltage or current to the pressure
switch, causing damage.
7) Design the product to prevent reverse current when the circuit is open or the product is
forced to operate for operational checks. Depending on the circuit used, insulation may not
be maintained when operation is forced, allowing reverse current to flow, which can cause
malfunction and damage to the solenoid valve and pressure switch.
8) Keep wiring as short as possible to prevent interference from electromagnetic noise and
surge voltage. Do not use a cable longer than 10m. Wire the DC (-) line as close as possible
to the power supply.