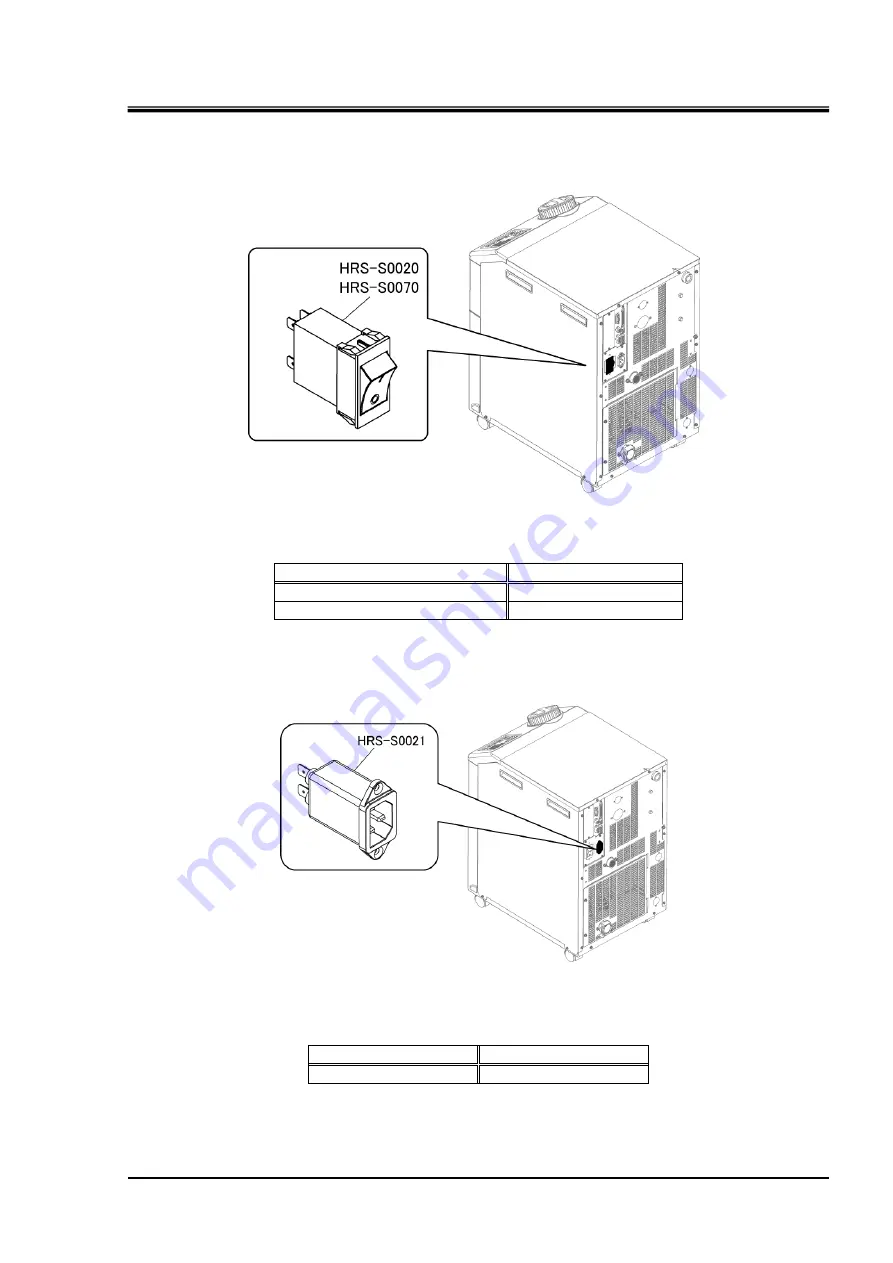
HRX-MM-N007
Chapter 5 Service Parts List
HRS Series
5.3 Illustration of Service Parts
5-9
5.3.9
Power switch
Fig. 5.3-9 Power switch
Table 5-10 Part number of service parts (Power switch)
Description
Part number
Power switch (For 10A type)
HRS-S0020
Power switch (For 20A type)
HRS-S0070
5.3.10 Inlet socket
Fig. 5.3-10 Inlet socket
Table 5-11 Part number of service parts (Inlet socket)
Description
Part number
Inlet socket
HRS-S0021
Содержание HRS012-A*-10-*
Страница 16: ...HRX MM N007 Chapter 2 Name of Parts 2 2 Component Parts HRS Series 2 4...
Страница 136: ...HRX MM N007 Chapter 3 Alarm Indication and Troubleshooting 3 3 Troubleshooting HRS Series 3 120...
Страница 200: ...HRX MM N007 Chapter 4 Service Procedure 4 5 Replacement Procedure HRS Series 4 64...
Страница 220: ...HRX MM N007 Chapter 6 Documents 6 4 Flow chart HRS Series 6 8...