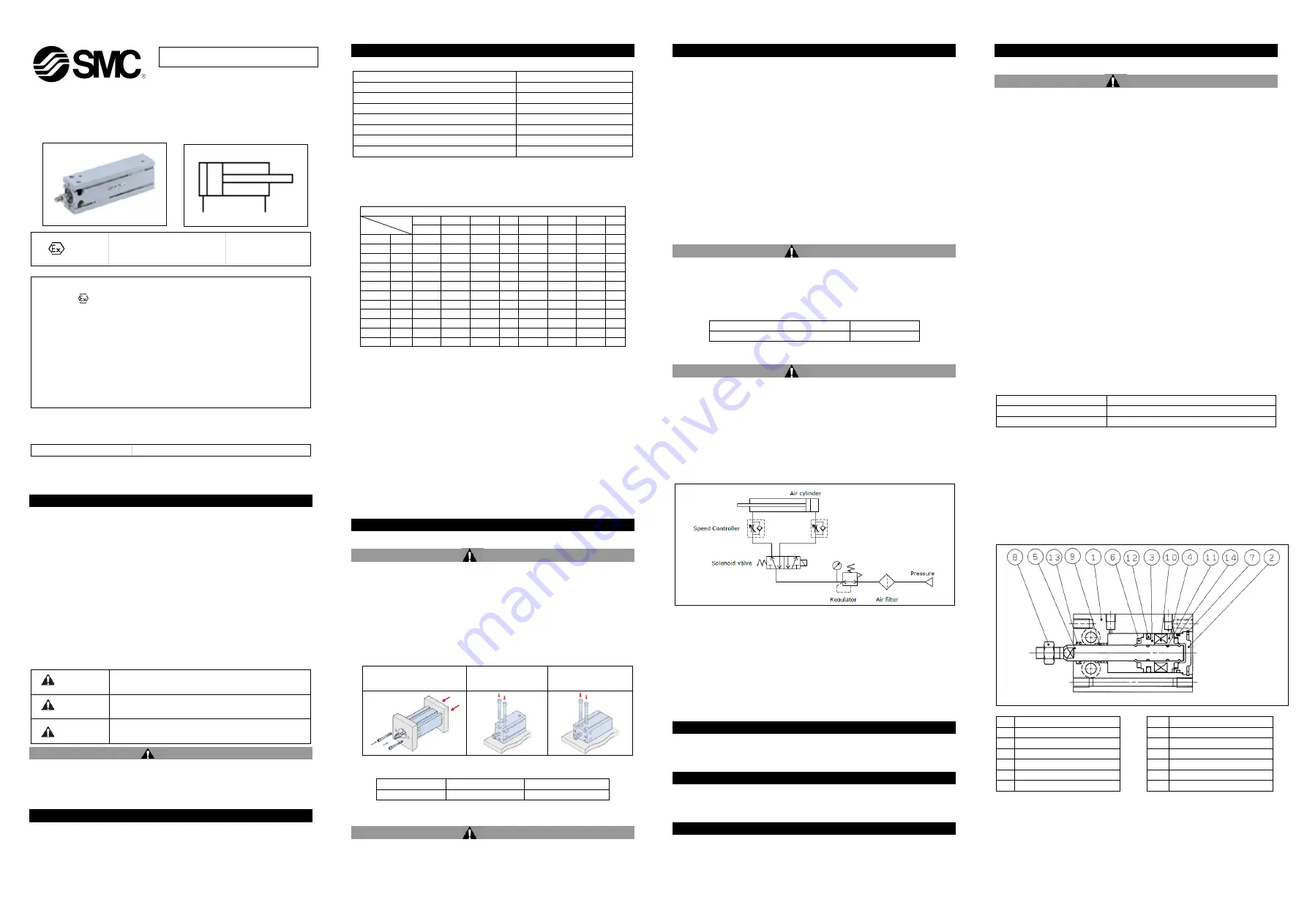
55-CU##-TF222-129EN
Page 1 of 2
Instruction Manual
Free Mount Cylinder
55-CDU25-*-DCW3726W
II 2GD
Ex h IIC T4/T4 Gb
-10°C
≤Ta≤ +60°C
Ex h IIIC T101°C/T121°C Db
Marking Description:
Specific Marking for Explosion Protection
II
Equipment Group
2
Equipment Category
GD
Environment (Gas and Dust)
Ex h
Type of Protection
– Constructional Safety ‘c’
IIC
Gas Sub-Division
IIIC
Dust Sub-Division
T
Temp. Classification
Gb / Db Equipment Protection Level
X
Special Conditions of Use
Ta
Ambient Temperature Range
The intended use of this actuator is to convert the potential energy
provided by compressed air into a force which causes mechanical linear
motion.
Certifcate Number:
SMC22.0032X
Note:
The X at the end of the certificate number represents that this product is
subject to “Special Conditions of Use”, please see Section 2.3.
1 Safety Instructions
These safety instructions are intended to prevent hazardous situations
and/or equipment damage. These instructions indicate the level of
potential hazard with the labels of “Caution,” “Warning” or “Danger.”
They are all important notes for safety and must be followed in addition
to International Standards (ISO/IEC)
*1)
, and other safety regulations.
*1)
ISO 4414: Pneumatic fluid power - General rules relating to systems.
ISO 4413: Hydraulic fluid power - General rules relating to systems.
IEC 60204-1: Safety of machinery - Electrical equipment of machines.
(Part 1: General requirements)
ISO 10218-1: Robots and robotic devices - Safety requirements for
industrial robots - Part 1: Robots.
•
Refer to product catalogue, Operation Manual and Handling
Precautions for SMC Products for additional information.
•
Keep this manual in a safe place for future reference.
Caution
Caution indicates a hazard with a low level of risk which, if
not avoided, could result in minor or moderate injury.
Warning
Warning indicates a hazard with a medium level of risk
which, if not avoided, could result in death or serious injury.
Danger
Danger indicates a hazard with a high level of risk which, if
not avoided, will result in death or serious injury.
Warning
•
Always ensure compliance with relevant safety laws and
standards.
•
All work must be carried out in a safe manner by a qualified person in
compliance with applicable national regulations.
2 Specifications
This product is suitable for use in Zones 1, 2, 21 and 22 only.
2.1 Product Specifications:
Refer to the operation manual for this product;
2 Specifications (continued)
Fluid
Air
Max. Operating Pressure
0.7 MPa
Min. Operating Pressure
0.05 MPa
Ambient & Fluid Temperature
-10°C to +60°C
Lubrication
Not Required
Operating Piston Speed
50 to 500 mm/s
Cushion
Rubber Bumper
Allowable Kinetic Energy
0.2 J
2.2 Production Batch Code:
The batch code printed on the label indicates the month and the year of
production as per the following table;
Production Batch Codes
Year
Month
2021
2022
2023
…
2027
2028
2029
…
Z
A
B
…
F
G
H
…
Jan
o
Zo
Ao
Bo
…
Fo
Go
Ho
…
Feb
P
ZP
AP
BP
…
FP
GP
HP
…
Mar
Q
ZQ
AQ
BQ
…
FQ
GQ
HQ
…
Apr
R
ZR
AR
BR
…
FR
GR
HR
…
May
S
ZS
AS
BS
…
FS
GS
HS
…
Jun
T
ZT
AT
BT
…
FT
GT
HT
…
Jul
U
ZU
AU
BU
…
FU
GU
HU
…
Aug
V
ZV
AV
BV
…
FV
GV
HV
…
Sep
W
ZW
AW
BW
…
FW
GW
HW
…
Oct
X
ZX
AX
BX
…
FX
GX
HX
…
Nov
y
Zy
Ay
By
…
Fy
Gy
Hy
…
Dec
Z
ZZ
AZ
BZ
…
FZ
GZ
HZ
…
2.3 Special Conditions of Use:
•
Products are suitable for sub-divisions IIC and IIIC.
•
Products are suitable for Zone 1, 2, 21 and 22 only.
2.3.1 Temperature Marking:
2.3.1.1 Standard Product:
•
In the normal ambient temperature range (-10°C to +40°C) the product
is rated to temperature class T4 and has a maximum surface
temperature of 101°C.
•
In the special ambient temperature range (+40°C to +60°C) the product
is rated to temperature class T4 and has a maximum surface
temperature of 121°C.
3 Installation
3.1 Installation
Warning
•
Do not install the product unless the safety instructions have been read
and understood.
•
Do not twist or bend the cylinder, or mount the product when subject
to tension.
•
Do not use in an application where the product is stopped mid-stroke,
via an external stop.
•
Do not use where cylinders are being synchronised to move a single
load.
•
The product can be mounted in one of the following orientations.
Axial Mounting
(Body Tapped)
Vertical Mounting
(Body Through-hole)
Lateral Mounting
(Body Through-hole)
•
When mounting the product use the hexagon socket head cap screw
and tightening torque defined below;
Bore [mm]
Screw Dia.
Tightening Torque
Ø 25
M5
5.10 ± 10%
3.2 Environment
Warning
•
Do not use in an environment where corrosive gases, chemicals, salt
water or steam are present.
•
Do not use in an explosive atmosphere.
3 Installation - continued
•
Do not expose to direct sunlight. Use a suitable protective cover.
•
Do not install in a location subject to vibration or impact in excess of
the product’s specifications.
•
Do not mount in a location exposed to radiant heat that would result in
temper
atures in excess of the product’s specifications.
•
Do not install in a location subject to vibration or impact in excess of
the product’s specifications.
•
Do not use in a place subject to heavy vibration and/or shock.
•
Do not use in wet environments, where water can remove the presence
of the lubrication.
•
Do not use in case of heavy dusty environments where dust can
penetrate into the cylinder and dry the grease.
•
Do not allow dust layers to build up on the cylinder surface and insulate
the product.
3.3 Piping
Caution
•
Before connecting piping make sure to clean up chips, cutting oil, dust
etc.
•
When installing piping or fittings, ensure sealant material does not
enter inside the port. When using seal tape, leave 1 thread
exposed
on the end of the pipe/fitting.
•
Tighten fittings to the specified tightening torque.
PPN
Port Size
55-CDU25-*-DCW3726W
M5 x 0.8
3.4 Lubrication
Caution
•
SMC products have been lubricated for life at manufacture, and do not
require lubrication in service.
•
If a lubricant is used in the system, refer to catalogue for details.
3.5 Basic Circuit
•
Plugging one of the ports on the actuator is considered a non-intended
use, and could relate to an increase in maximum surface temperature
above what the product specification declares.
3.6 Electrical Connection
•
The product should be grounded by the piston rod and the body in
order to create an electrically conductive path to the system/application.
•
Ground the product in accordance with applicable regulations.
•
Do not pass an electrical current through the product.
4 Settings
Refer to the standard product operation manual for settings.
5 How to Order
Refer to customer drawing
for ‘How to Order’.
6 Outline Dimensions
Refer to
customer drawing
for outline dimensions.
7 Maintenance
7.1 General maintenance
Caution
•
Not following proper maintenance procedures could cause the product
to malfunction and lead to equipment damage.
•
If handled improperly, compressed air can be dangerous.
•
Maintenance of pneumatic systems should be performed only by
qualified personnel.
•
Before performing maintenance, turn off the power supply and be sure
to cut off the supply pressure. Confirm that the air is released to
atmosphere.
•
After installation and maintenance, apply operating pressure and
power to the equipment and perform appropriate functional and
leakage tests to make sure the equipment is installed correctly.
•
If any electrical connections are disturbed during maintenance, ensure
they are reconnected correctly and safety checks are carried out as
required to ensure continued compliance with applicable national
regulations.
•
Do not make any modification to the product.
•
Do not disassemble the product, unless required by installation or
maintenance instructions.
•
Do not use a product which looks or contains damage, this will
invalidate the certification. If damage is seen, please replace the
product immediately.
•
Periodically check the product for any damage or rust appearing. This
could result in an increase in friction and lead to dangerous conditions.
Replace the whole actuator if any of these conditions appear.
•
Periodically check the condition of the rod seal and for the presence of
lubrication, where possible. If these areas appear to be dry, please
follow the lubrication procedure.
•
The seals should be replaced when the air leakage is above the
allowable value given in the table below;
Allowable Leakage
Internal Leakage
10 cm
3
/ min (ANR)
External Leakage
5 cm
3
/ min (ANR)
7.2 Disassembly Procedure
•
Disassemble the cylinder, remove the old grease and place all the
parts on a clean cloth in a clean environment. Use a set of snap ring
pliers to remove the retaining ring (7) and then remove the head cover
(2). Remove the old piston seal (12), rod seal (13) and gasket (14),
using a fine screwdriver where necessary.
1
Cylinder Tube
8
Rod End Nut
2
Head Cover
9
Bushing
3
Piston
10
Magnet
4
Magnet Holder
11
Piston Gasket (NBR)
5
Piston Rod
12
Piston Seal (NBR)
6
Bumper
13
Rod Seal (NBR)
7
Retaining Ring
14
Gasket (NBR)
ORIGINAL INSTRUCTIONS