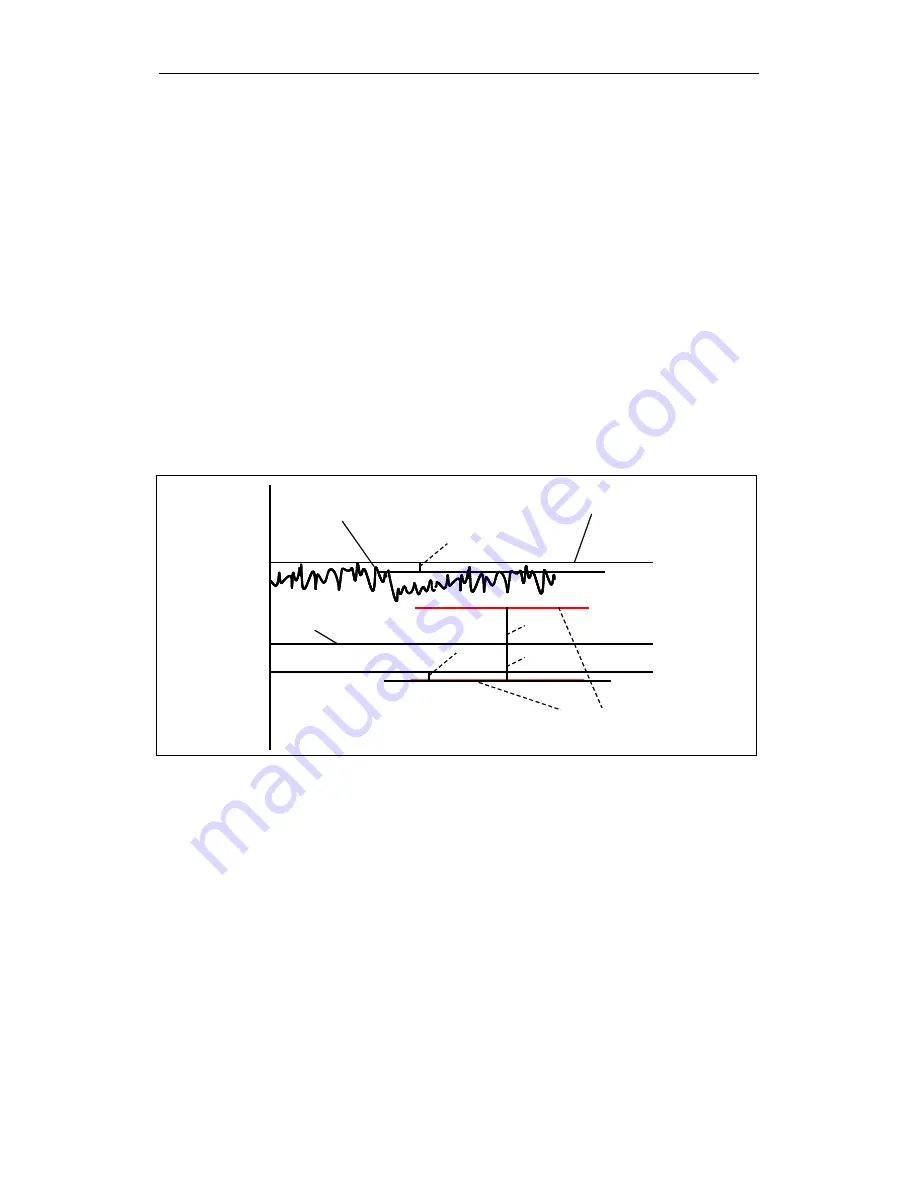
8 Application examples
11.03
8.3 Testing the function of the brake mechanical system
© Siemens AG 2003 All Rights Reserved
8-456
SINUMERIK 840D/SIMODRIVE 611 digital SINUMERIK Safety Integrated (FBSI) - Edition 11.03
The signal "PLC controlled axis" (DB "Axis".DBX28.7) must still be set to state 1
by the user program for the entire duration of the test. Prior to activating the
signal "PLC controlled axis", the axis must be set as "neutral axis", e.g. set
byte 8 in the axis DB to channel 0. Set the activating signal in the same byte.
The block may not be started until the NC checkback signal has been received
via the appropriate bit (DB Axis.DBX 63.1).
For PLC-controlled axis, also refer to:
References:
/FB2/ P2 "Autonomous single-axis processes (SW 6.3 and
higher)"
8.3.6 Examples
An example of incorrect parameterization that results in Alarm 20095, "Axis %1
impermissible holding torque, measured torque %2" is shown in the following
diagram: The torque due to weight in the drive machine data 1192 has been
parameterized considerably lower than the measured torque m
Act
. The
calculated torque limit m
FXS
symmetrically around this MD would mean that the
drive would not be able to produce the required holding torque for this axis
(m
FXS
is lower than m
Act
).
m
t
MD BRAKETEST_TORQUE
0
Measured torque on
selection of brake test
m
Torque limiting in current
controller:
611D-MD 1192
m
Act
Drive
MD 1192 + / - m
FXS
m
FXS
m
Drive
m
FXS
Fig. 8-6
Example of incorrect parameterization
To support start-up of the brake test, Alarm 20096, "Axis %1 Brake test
aborted, Additional info %2” can be enabled via bit 5 in machine data
$MN_ENABLE_ALARM_MASK. This alarm supplies detailed information if the
brake test is interrupted.
Commissioning