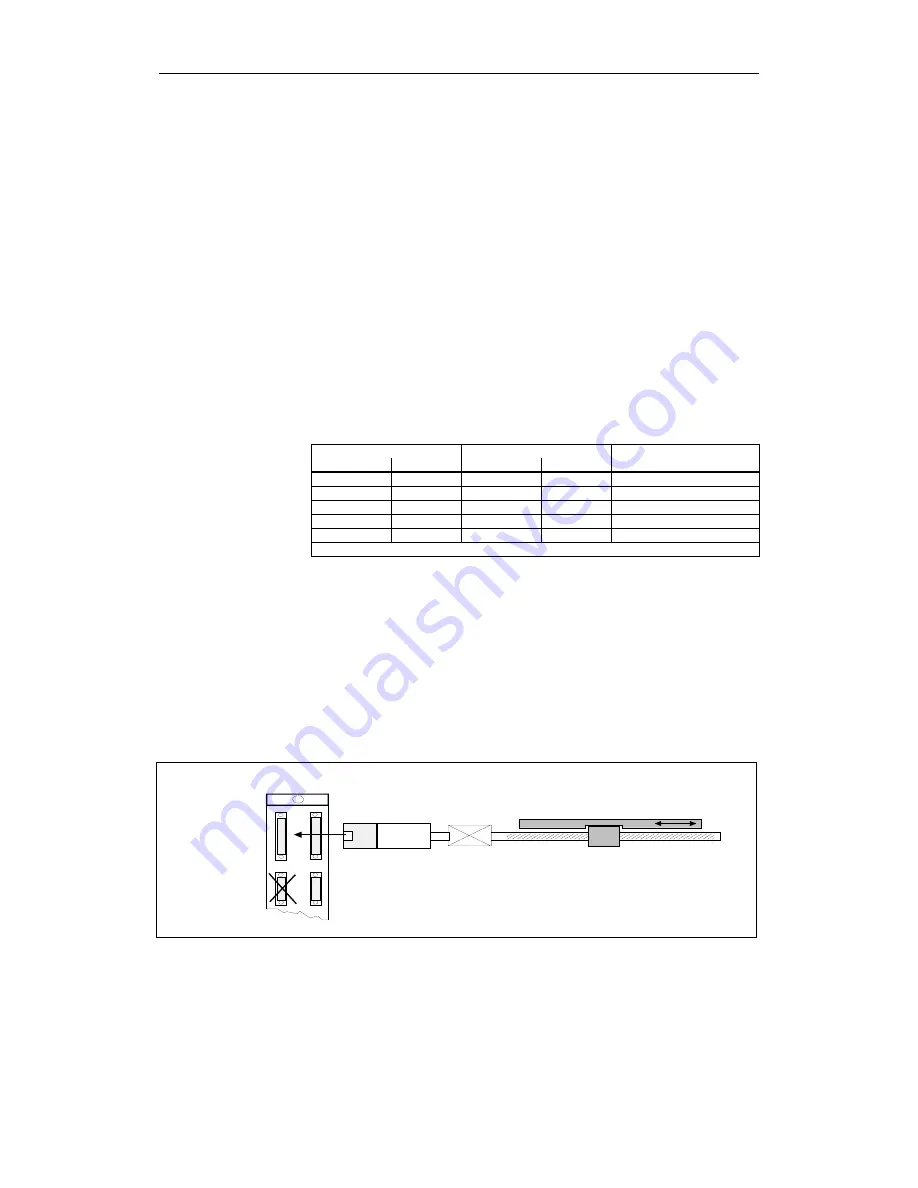
3 Safety-Related Functions
11.03
3.11 Encoder mounting arrangements
© Siemens AG 2003 All Rights Reserved
3-168
SINUMERIK 840D/SIMODRIVE 611 digital SINUMERIK Safety Integrated (FBSI) - Edition 11.03
3.11 Encoder mounting arrangements
3.11.1 Encoder
types
The following basic types of encoder can be used on a drive module for the
purpose of safe operation:
•
Incremental encoder
with sinusoidal voltage signals A and B (signal A is in quadrature with
signal B) and a reference signal R
e.g.: ERN 1387, LS 186, SIZAG2
•
Absolute encoder
with EnDat interface and incremental, sinusoidal voltage signals A and B
(signal A is in quadrature with signal B)
e.g.: EQN 1325, LC 181
Various combinations can be derived from the basic types.
Table 3-64
Combinations of encoder types
Incremental encoder
Absolute encoder
at the motor at the load at the motor at the load Comments
x 1-encoder
system
x
1-encoder
system
x x
2-encoder
system
x x
2-encoder
system
x x
2-encoder
system
Note: x Encoder connection
For a 1-encoder system, the incremental or absolute encoder at the motor is
used for the actual values of the NC and drive.
The 611 digital control module supplies one actual value to the NCK and drive
via 2 separate actual value channels..
Special feature for linear motors:
For linear motors, the motor encoder (linear scale) is also the measuring
system at the load. IMS and DMS are one measuring system. The connection
is made at the IMS input of the 611 digital control module.
G e b e r
G e tr ie b e
L o se
G E B E R _ 0 2 . D S F
A n sc h lu ß
d e s
M o to rg e b e rs
(IM S )
M o to r
(V S A )
M a s ch in e n tisc h
V S A
A n sc h lu ß
d e s d ire kte n
L a g e g e b e rs
(D M S )
Fig. 3-39
1-encoder system for a feed drive
Basic types
Combinations of
encoder types
1-encoder system