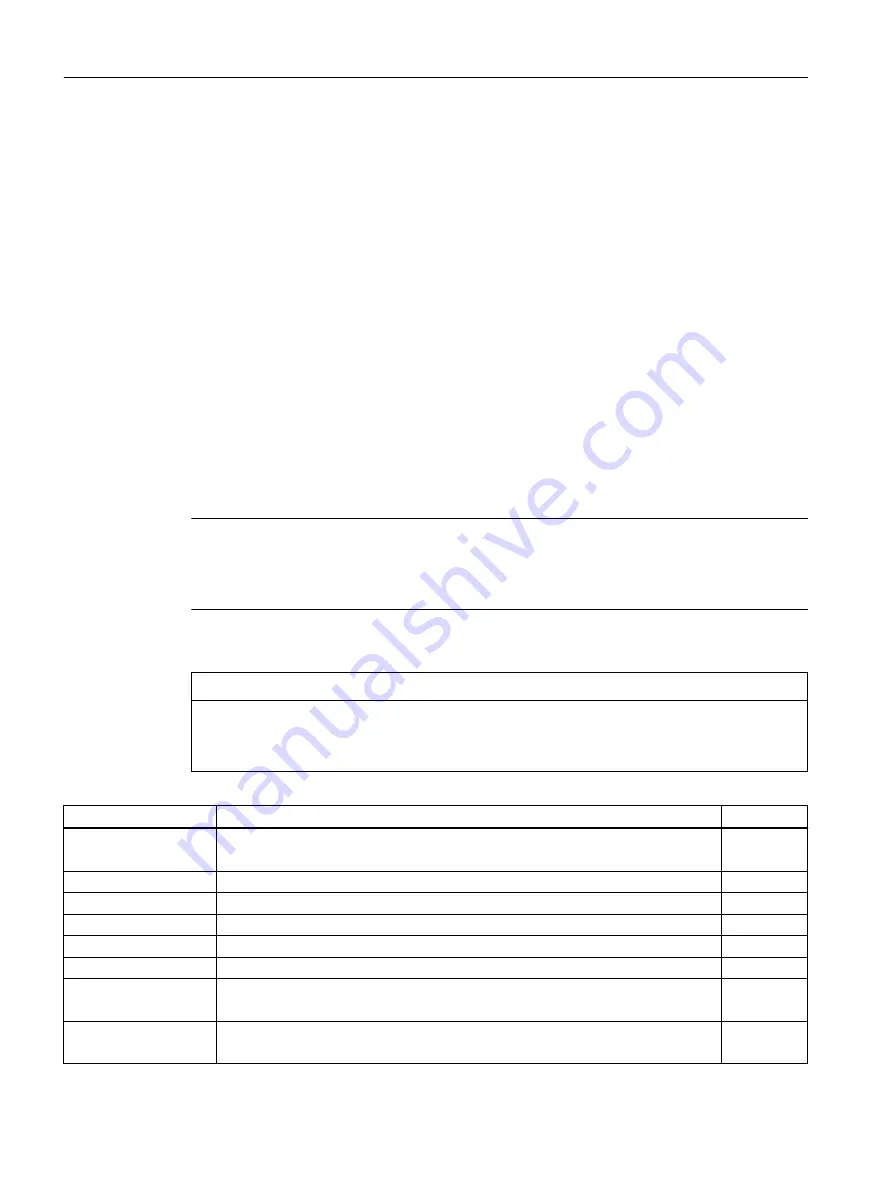
17.5
Approach/retraction
If you want to optimize approach/return for swiveling with the B axis, you can create a special
cycle that ignores the automatic approach/retraction strategy.
You can insert the approach/retraction cycle between any machining step program blocks, but
not within linked program blocks.
Sequence
The starting point for the approach/retraction cycle is the safety clearance approached after the
last machining operation.
If you want to perform a tool change, you can move the tool through a total of three positions
(P1 to P3) to the tool change point and through a maximum of three additional positions (P4 to
P6) to the next starting point.
The 1st, 3rd, 4th and 6th positions move the linear axes, while the 2nd and 5th positions move
the rotary axes.
If no tool change is needed you can generate no more than six motion blocks.
The numbers (1 - 6) represent the processing sequence.
Note
Programming additional positions
If three or six positions are not sufficient for the approach/retraction, you can call the cycle
several times in succession to program further positions.
NOTICE
Risk of collision
Note that the tool will move from the last position programmed in the approach/retraction cycle
directly to the starting point for the next machining operation.
Parameter
Description
Unit
F1
Feedrate to approach the first position
Alternatively, rapid traverse
mm/min
X1
1. position (inc or ∅ abs)
mm
Z1
1. position (inc or ∅ abs)
mm
Y1
Retraction to safety clearance
mm
β2
Beta angle for 1st swivel movement
Degrees
γ2
Gamma angle for 1st swivel movement
Degrees
Tracking
The position of the tool tip is maintained during swiveling.
Please refer to the machine manufacturer's instructions.
F3
Feedrate to approach the third position
Alternatively, rapid traverse
mm/min
Working with a B axis (only 840D sl)
17.5 Approach/retraction
Turning
882
Operating Manual, 06/2019, A5E44903486B AB
Содержание SINUMERIK 840D sl
Страница 8: ...Preface Turning 8 Operating Manual 06 2019 A5E44903486B AB ...
Страница 70: ...Introduction 2 4 User interface Turning 70 Operating Manual 06 2019 A5E44903486B AB ...
Страница 274: ... Creating a G code program 8 8 Selection of the cycles via softkey Turning 274 Operating Manual 06 2019 A5E44903486B AB ...
Страница 275: ... Creating a G code program 8 8 Selection of the cycles via softkey Turning Operating Manual 06 2019 A5E44903486B AB 275 ...
Страница 282: ...Creating a G code program 8 10 Measuring cycle support Turning 282 Operating Manual 06 2019 A5E44903486B AB ...
Страница 344: ...Creating a ShopTurn program 9 19 Example Standard machining Turning 344 Operating Manual 06 2019 A5E44903486B AB ...
Страница 716: ...Collision avoidance 12 2 Set collision avoidance Turning 716 Operating Manual 06 2019 A5E44903486B AB ...
Страница 774: ...Tool management 13 15 Working with multitool Turning 774 Operating Manual 06 2019 A5E44903486B AB ...
Страница 834: ...Managing programs 14 19 RS 232 C Turning 834 Operating Manual 06 2019 A5E44903486B AB ...
Страница 856: ...Alarm error and system messages 15 9 Remote diagnostics Turning 856 Operating Manual 06 2019 A5E44903486B AB ...
Страница 892: ...Working with two tool carriers 18 2 Measure tool Turning 892 Operating Manual 06 2019 A5E44903486B AB ...
Страница 912: ...HT 8 840D sl only 20 5 Calibrating the touch panel Turning 912 Operating Manual 06 2019 A5E44903486B AB ...
Страница 927: ...Appendix A A 1 840D sl 828D documentation overview Turning Operating Manual 06 2019 A5E44903486B AB 927 ...