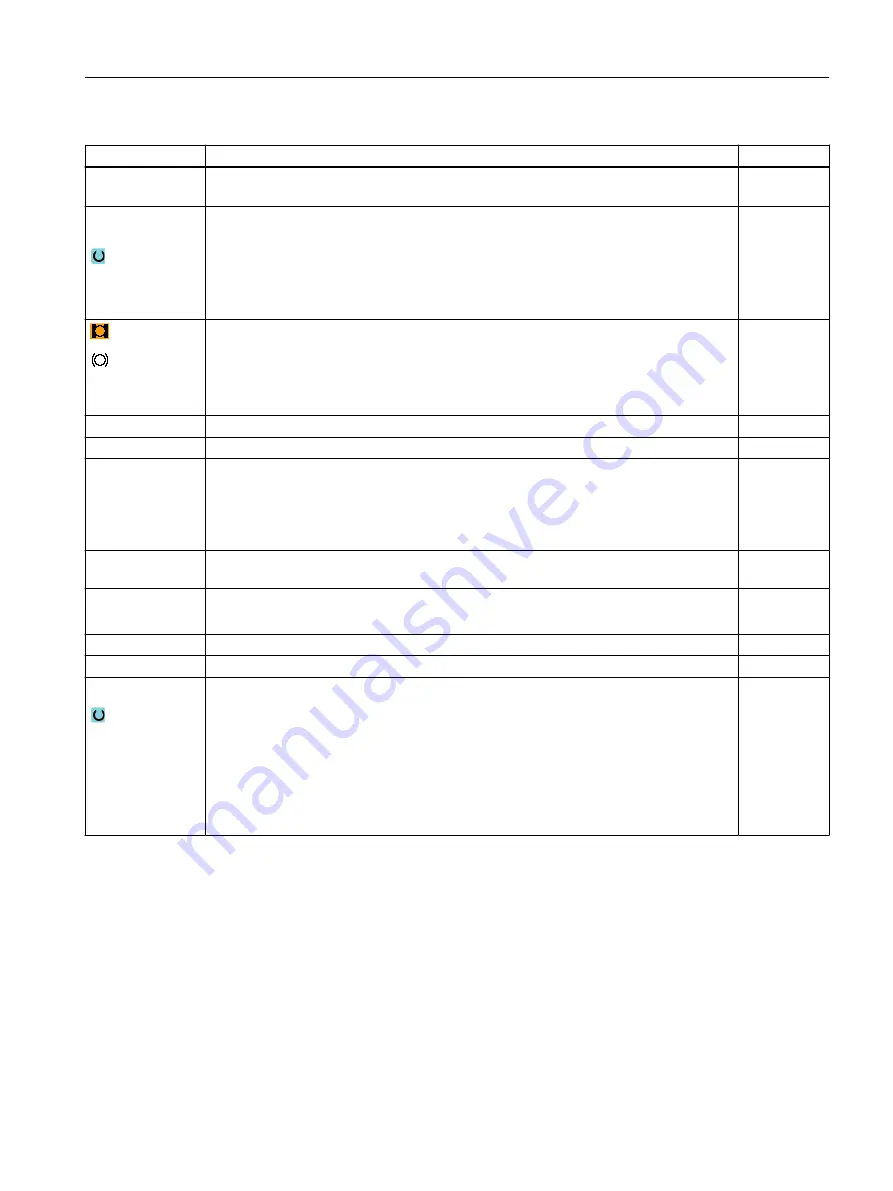
Parameter
Description
Unit
TR
Reference tool Tool, which is used in the "stock removal" machining step. This is used to
determine the plunge position.
Machining
surface
(only for Shop‐
Turn)
● Face C
● Face Y
● Face B
● Peripheral surface C
● Peripheral surface Y
(only for Shop‐
Turn)
Clamp/release spindle (only for end face Y/B and peripheral surface Y)
The function must be set up by the machine manufacturer.
Z0
Reference point in the tool axis Z
mm
Z1
Pocket depth (abs) or depth referred to Z0 or X0 (inc)
mm
CP
Positioning angle for machining area
- (only for ShopTurn, machining surface, face Y)
Angle CP does not have any effect on the machining position in relation to the workpiece.
It is only used to position the workpiece with the rotary axis C in such a way that machining
is possible on the machine.
Degrees
C0
Positioning angle for machining surface
- (only for ShopTurn, machining surface, peripheral surface Y)
Degrees
DXY
● Maximum plane infeed
● Maximum plane infeed as a percentage of the milling cutter diameter
mm
%
UXY
Finishing allowance, plane
mm
UZ
Finishing allowance, depth
mm
Lift mode
Lift mode before new infeed
If the machining operation requires several points of insertion, the retraction height can be
programmed:
● To retraction plane
● Z0 + safety clearance
When making the transition to the next insertion point, the tool returns to this height. If
there are no elements larger than Z0 (X0) in the pocket area, then Z0 (X0) + safety
clearance can be programmed as the lift mode.
mm
mm
10.5.10
Milling contour pocket (CYCLE63)
Function
You can use the "Mill pocket" function to mill a pocket on the face or peripheral surface.
Before you remove stock from the pocket, you must first enter the contour of the pocket and, if
applicable, the contour of an island. Stock is removed from the pocket parallel to the contour
Programming technology functions (cycles)
10.5 Contour milling
Turning
Operating Manual, 06/2019, A5E44903486B AB
587
Содержание SINUMERIK 840D sl
Страница 8: ...Preface Turning 8 Operating Manual 06 2019 A5E44903486B AB ...
Страница 70: ...Introduction 2 4 User interface Turning 70 Operating Manual 06 2019 A5E44903486B AB ...
Страница 274: ... Creating a G code program 8 8 Selection of the cycles via softkey Turning 274 Operating Manual 06 2019 A5E44903486B AB ...
Страница 275: ... Creating a G code program 8 8 Selection of the cycles via softkey Turning Operating Manual 06 2019 A5E44903486B AB 275 ...
Страница 282: ...Creating a G code program 8 10 Measuring cycle support Turning 282 Operating Manual 06 2019 A5E44903486B AB ...
Страница 344: ...Creating a ShopTurn program 9 19 Example Standard machining Turning 344 Operating Manual 06 2019 A5E44903486B AB ...
Страница 716: ...Collision avoidance 12 2 Set collision avoidance Turning 716 Operating Manual 06 2019 A5E44903486B AB ...
Страница 774: ...Tool management 13 15 Working with multitool Turning 774 Operating Manual 06 2019 A5E44903486B AB ...
Страница 834: ...Managing programs 14 19 RS 232 C Turning 834 Operating Manual 06 2019 A5E44903486B AB ...
Страница 856: ...Alarm error and system messages 15 9 Remote diagnostics Turning 856 Operating Manual 06 2019 A5E44903486B AB ...
Страница 892: ...Working with two tool carriers 18 2 Measure tool Turning 892 Operating Manual 06 2019 A5E44903486B AB ...
Страница 912: ...HT 8 840D sl only 20 5 Calibrating the touch panel Turning 912 Operating Manual 06 2019 A5E44903486B AB ...
Страница 927: ...Appendix A A 1 840D sl 828D documentation overview Turning Operating Manual 06 2019 A5E44903486B AB 927 ...