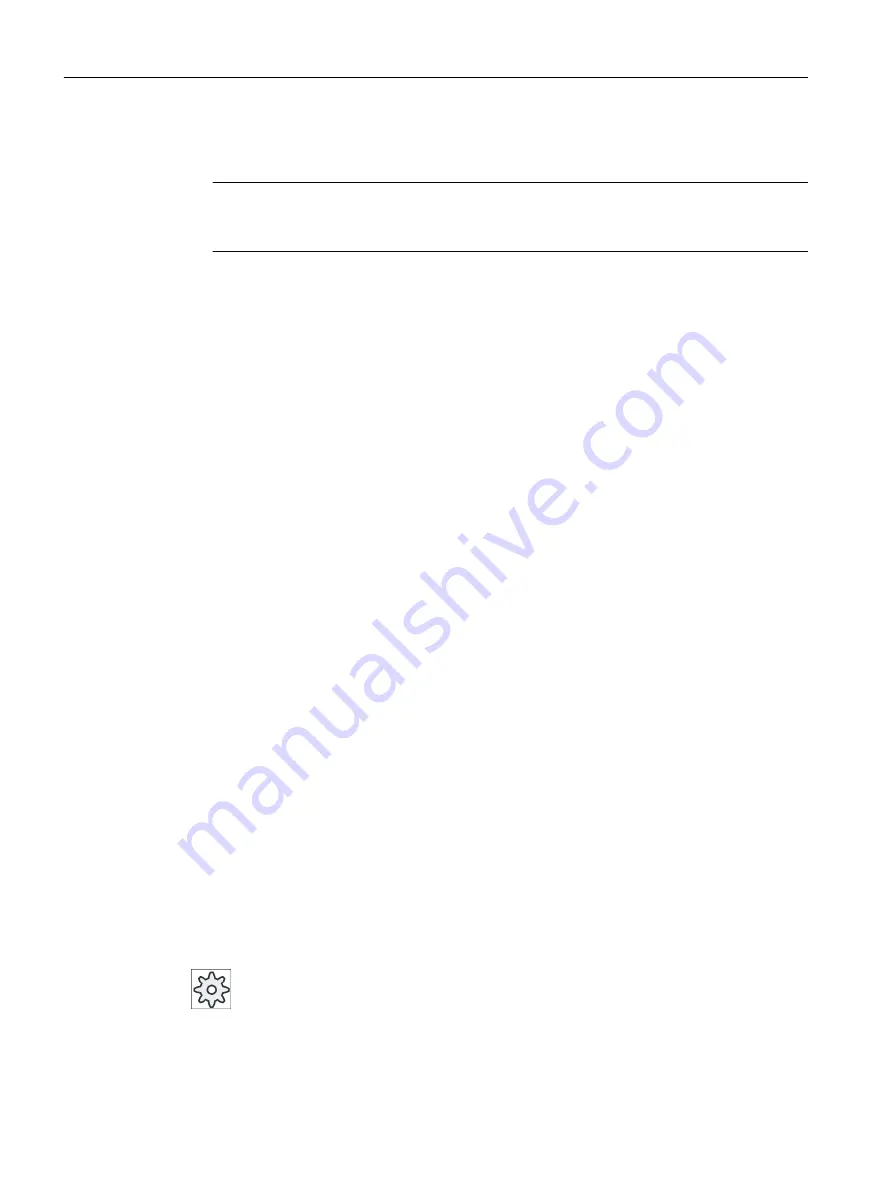
● 3500 operating steps max. per clamping
● Max. 49 clampings
Note
You can bypass the markers or repetitions, which must not be included in programs for
multiple clampings, by using subprograms.
14.20.2
Program header setting, "Clamping"
During the generation of a multiple clamping program, data from the program header of a
source program are transferred to a settings step of the multiple clamping program after every
clamping change. The setting of the clamping in the program header is also part of this data.
The clampings in the program header designate the name of the rotary axis in which the blank
is clamped.
A distinction is made between the following multiple clamping programs:
● Program type 1, in which the same program is assigned to several clampings.
● Program type 2, in which a different program is assigned to each clamping.
A distinction is made between the following systems:
● System type Α
All clampings of the multiple clamping are mounted on a table or on a rotary axis.
● System type B
The clampings are distributed over different rotary axes (rotary tables).
Multiple clamping programs of program type 1 cannot be executed on installations of type B
and are therefore not permitted.
Reason:
The program header contains the axis name of one clamping. Since this axis name is entered
in each setting step at a clamping change, the assignment to the actual rotary axis of the
respective clamping is missing in the generated multiple clamping program.
Example:
The installation has two rotary tables C1 and C2. The same blank is clamped on both tables.
Both blanks are to be machined with the same program. The rotary table must be addressed
for the machining.
The original program designates clamping C1 in the program header. The resulting multiple
clamping program uses the axis name C1 for both rotary tables, because the other axis name
is not known to the program.
The other combinations of multiple clamping programs and installation types are permitted
and supported.
Machine manufacturer
Please observe the information provided by the machine manufacturer.
Managing programs
14.20 Multiple clamping
Milling
806
Operating Manual, 08/2018, 6FC5398-7CP41-0BA0
Содержание SINUMERIK 828D Turning
Страница 68: ...Introduction 2 4 User interface Milling 68 Operating Manual 08 2018 6FC5398 7CP41 0BA0 ...
Страница 162: ...Setting up the machine 4 12 MDA Milling 162 Operating Manual 08 2018 6FC5398 7CP41 0BA0 ...
Страница 270: ...Machining the workpiece 6 17 Setting for automatic mode Milling 270 Operating Manual 08 2018 6FC5398 7CP41 0BA0 ...
Страница 278: ...Swivel combination 45 90 Simulating machining 7 1 Overview Milling 278 Operating Manual 08 2018 6FC5398 7CP41 0BA0 ...
Страница 294: ...Simulating machining 7 9 Displaying simulation alarms Milling 294 Operating Manual 08 2018 6FC5398 7CP41 0BA0 ...
Страница 316: ...Generating a G code program 8 10 Measuring cycle support Milling 316 Operating Manual 08 2018 6FC5398 7CP41 0BA0 ...
Страница 684: ...Collision avoidance 12 2 Set collision avoidance Milling 684 Operating Manual 08 2018 6FC5398 7CP41 0BA0 ...
Страница 746: ...Tool management 13 16 Working with Multitool Milling 746 Operating Manual 08 2018 6FC5398 7CP41 0BA0 ...
Страница 830: ...Alarm error and system messages 15 9 Remote diagnostics Milling 830 Operating Manual 08 2018 6FC5398 7CP41 0BA0 ...
Страница 846: ... Working with Manual Machine 16 7 More complex machining Milling 846 Operating Manual 08 2018 6FC5398 7CP41 0BA0 ...
Страница 870: ...HT 8 840D sl only 18 5 Calibrating the touch panel Milling 870 Operating Manual 08 2018 6FC5398 7CP41 0BA0 ...
Страница 890: ...Easy Message 828D only 20 7 Making settings for Easy Message Milling 890 Operating Manual 08 2018 6FC5398 7CP41 0BA0 ...
Страница 924: ...Edit PLC user program 828D only 23 8 Searching for operands Milling 924 Operating Manual 08 2018 6FC5398 7CP41 0BA0 ...
Страница 925: ...Appendix A A 1 840D sl 828D documentation overview Milling Operating Manual 08 2018 6FC5398 7CP41 0BA0 925 ...