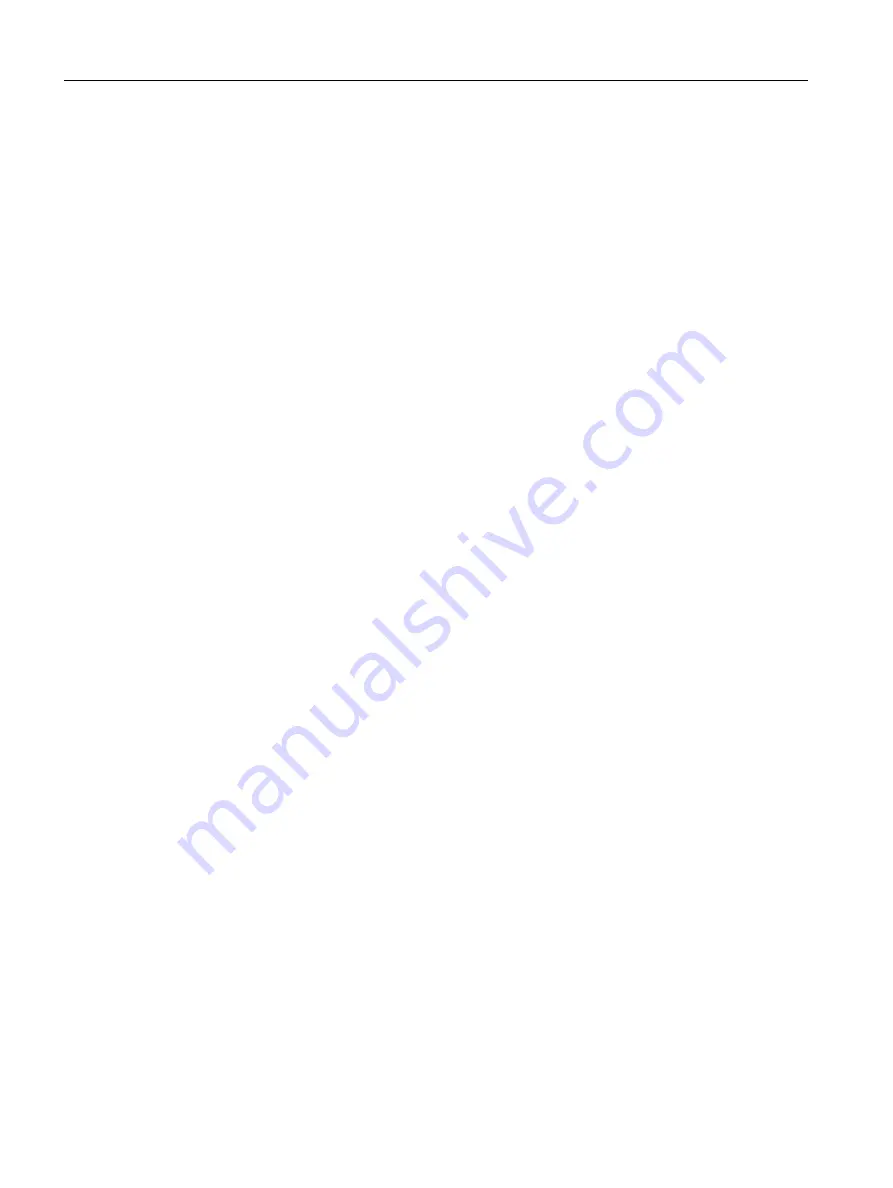
G2: Velocities, setpoint / actual value systems, closed-loop control
7.3 Metric/inch measuring system
Basic Functions
344
Function Manual, 09/2011, 6FC5397-0BP40-2BA0
NC-specific conversion factor
The default conversion factor in the machine data is:
MD10250 $MN_SCALING_VALUE_INCH (conversion factor for switchover to inch system)
set to 25.4 for converting from the metric to the inch measuring system. By changing the conversion factor, the
control system can also be adapted to customerspecific measuring systems.
Axis-specific conversion factor
The default conversion factor in the axis-specific machine data is:
MD31200 $MA_SCALING_FACTOR_G70_G71 (conversion factor when
G70
/
G71
is active)
set to 25.4 for converting from the metric to the inch measuring system. By changing the conversion factor, the
control system can also be adapted to customerspecific measuring systems on an axis-specific basis.
7.3.2
Manual switchover of the basic system
General
The control system can operate with the metric or inch measuring system. The initial setting of the measuring
system (basic system) is defined using the following machine data:
MD10240 $MN_SCALING_SYSTEM_IS_METRIC (basic system metric).
Depending on the basic system, all length-related data is interpreted either as metric or inch measurements.
The relevant softkey on the HMI in the "Machine" operating area is used to change the measuring system of the
controller.
The change in the measuring system occurs only under the following boundary conditions:
• MD10260 $MN_CONVERT_SCALING_SYSTEM=1
• Bit 0 of MD20110 $MC_RESET_MODE_MASK is set in every channel.
• All channels are in the Reset state.
• Axes doe not traverse with JOG, DRF or PLC.
• Constant grinding wheel peripheral speed (GWPS) is not active.
Actions such as part program start or mode change are disabled for the duration of the measuring system
changeover.
If the measuring system cannot be changed, this is indicated by a message to that effect on the user interface.
These measures ensure that a consistent set of data is always used for a running program with reference to the
measuring system.
The actual change in the measuring system is made by writing all the necessary machine data and subsequently
activating them with a
RESET
.
Содержание SINUMERIK 828D Turning
Страница 34: ...Basic Functions 34 Function Manual 09 2011 6FC5397 0BP40 2BA0 ...
Страница 146: ...A3 Axis Monitoring Protection Zones 2 6 Data lists Basic Functions 146 Function Manual 09 2011 6FC5397 0BP40 2BA0 ...
Страница 328: ...F1 Travel to fixed stop 6 5 Data lists Basic Functions 328 Function Manual 09 2011 6FC5397 0BP40 2BA0 ...
Страница 816: ...K2 Axis Types Coordinate Systems Frames 10 9 Data lists Basic Functions 816 Function Manual 09 2011 6FC5397 0BP40 2BA0 ...
Страница 1198: ...P4 PLC for SINUMERIK 828D 14 6 Function interface Basic Functions 1198 Function Manual 09 2011 6FC5397 0BP40 2BA0 ...
Страница 1752: ...Appendix 20 2 Overview Basic Functions 1752 Function Manual 09 2011 6FC5397 0BP40 2BA0 ...
Страница 1774: ...Glossary Basic Functions 1774 Function Manual 09 2011 6FC5397 0BP40 2BA0 ...