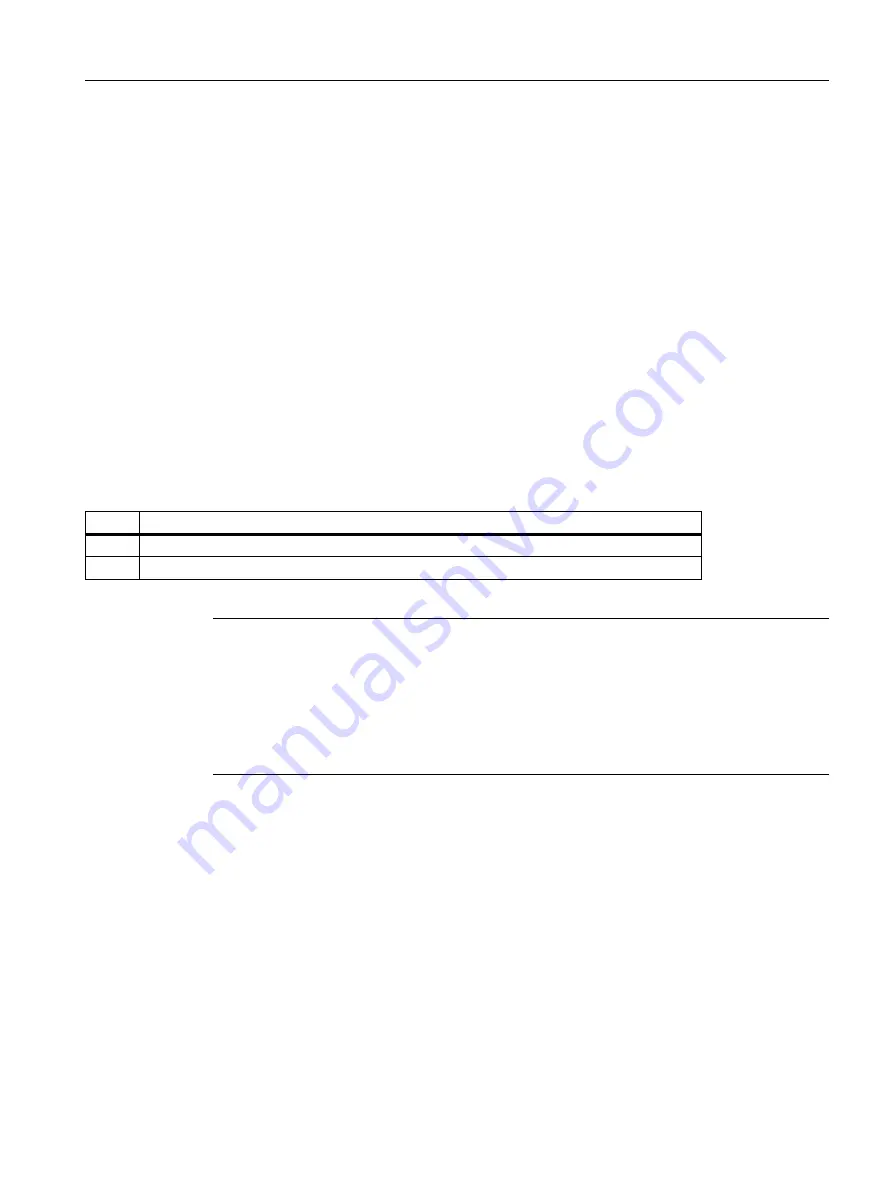
R1: Reference point approach
15.5 Referencing with incremental measurement systems
Basic Functions
Function Manual, 09/2011, 6FC5397-0BP40-2BA0
1211
Phase 2: Start
Phase 2 is automatically started when phase 1 has been completed without an alarm.
Initial situation:
The machine axis is positioned on the reference cam.
Zero mark search direction:
The zero mark is searched for in the parameterized direction and approached:
MD34050 $MA_REFP_SEARCH_MARKER_REVERSE (direction reversal on reference cam)
Phase 2: Sequence
Synchronization in Phase 2 can occur in two ways:
• Synchronization with falling reference cam signal edge
• Synchronization with rising reference cam signal edge
The type of synchronization is determined with the machine data:
MD34050 $MA_REFP_SEARCH_MARKER_REVERSE (direction reversal on reference cam)
Case 1: Synchronization with falling reference cam signal edge
During synchronization with falling reference cam signal edge, the machine axis accelerates to the
parameterized reference point creep velocity against the parameterized reference point approach direction
(traversing direction of Phase 1):
MD34040 $MA_REFP_VELO_SEARCH_MARKER (reference point creep velocity)
MD34010 $MA_REFP_CAM_DIR_IS_MINUS (Reference point approach in minus direction)
After the reference cam is exited (DB31, ... DBX12.7 = 0), the next encoder zero mark is awaited.
As soon as the encoder zero mark is detected, Phase 2 comes to an end. The machine axis continues at
constant velocity and reference point approach is continued with phase 3.
Value
Meaning
0
Synchronization with falling reference cam signal edge
1
Synchronization with rising reference cam signal edge
Note
If the actual velocity of the machine axis at appraoch of the reference cam has not yet
reached the target velocity of Phase 2 within the parameterized tolerence limits, Phase 1 will
be re-started:
MD35150 $MA_SPIND_DES_VELO_TOL (spindle speed tolerance)
This will be the case, for example, if the machine axes are positioned at the reference cam
when reference point approach starts.
Содержание SINUMERIK 828D Turning
Страница 34: ...Basic Functions 34 Function Manual 09 2011 6FC5397 0BP40 2BA0 ...
Страница 146: ...A3 Axis Monitoring Protection Zones 2 6 Data lists Basic Functions 146 Function Manual 09 2011 6FC5397 0BP40 2BA0 ...
Страница 328: ...F1 Travel to fixed stop 6 5 Data lists Basic Functions 328 Function Manual 09 2011 6FC5397 0BP40 2BA0 ...
Страница 816: ...K2 Axis Types Coordinate Systems Frames 10 9 Data lists Basic Functions 816 Function Manual 09 2011 6FC5397 0BP40 2BA0 ...
Страница 1198: ...P4 PLC for SINUMERIK 828D 14 6 Function interface Basic Functions 1198 Function Manual 09 2011 6FC5397 0BP40 2BA0 ...
Страница 1752: ...Appendix 20 2 Overview Basic Functions 1752 Function Manual 09 2011 6FC5397 0BP40 2BA0 ...
Страница 1774: ...Glossary Basic Functions 1774 Function Manual 09 2011 6FC5397 0BP40 2BA0 ...