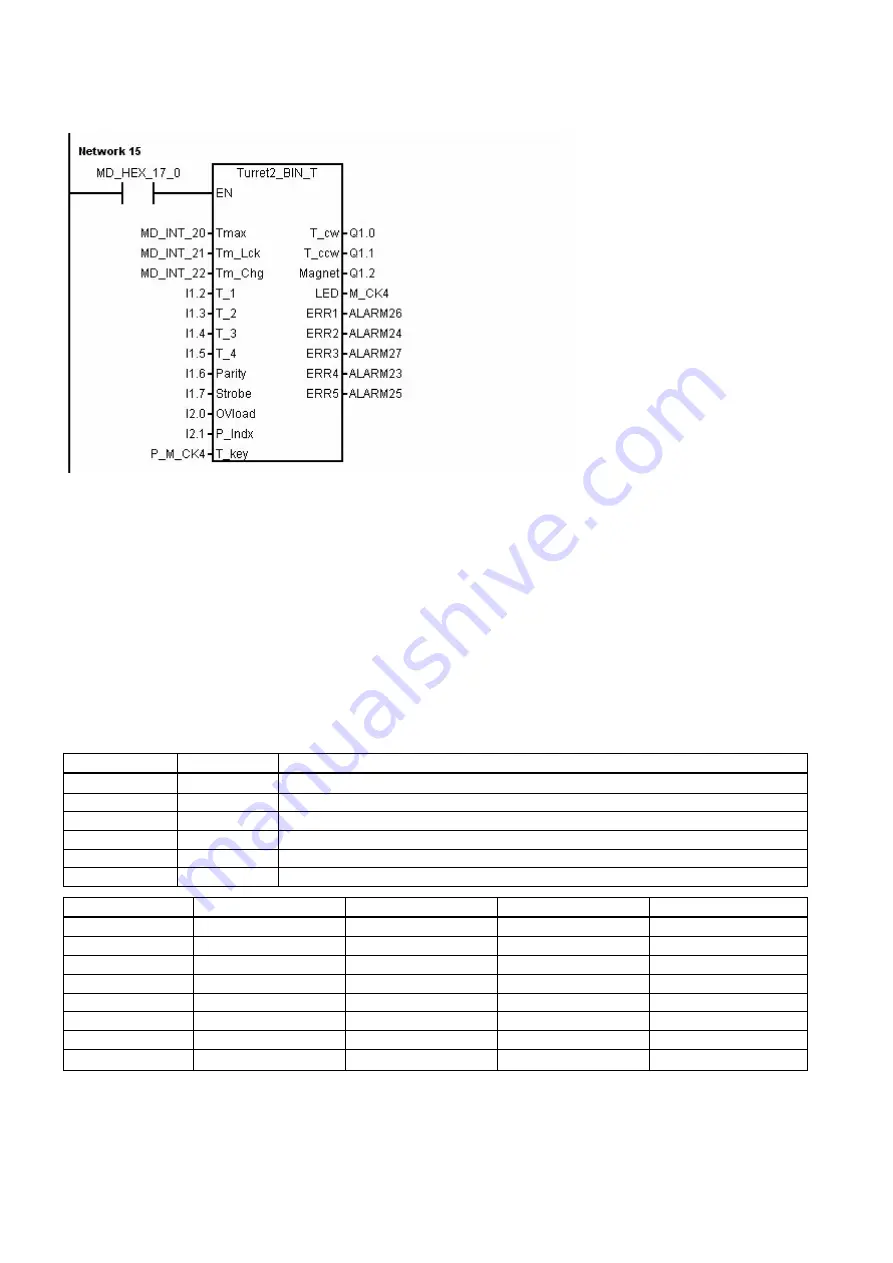
PLC Subroutines Manual
56
6FC5397-0FP40-0BA0, 08/2013
Example for calling subroutine 52
3.26
Subroutine 53 - Turret3_CODE_T (tool change control for turret with
coding function)
Purpose
Subroutine 53 is used to control the turret with coded tool positions and function of adjacent tool change. The difference
between the subroutine 52 and the subroutine 53 is that the subroutine 52 uses binary tool position codes while the
subroutine 53 uses tool position codes made according to a specific common turret.
During a tool change, the NC interface signal "Feedhold" (DB3200.DBX6.0) is set; this means that the part program can only
continue to run only after the tool change.
The turret positioning is prohibited in the case of an Emergency Stop, turret motor overload or program test/simulation.
Local variable definition
Table 3-30
Inputs
Name
Type
Description
M_time
WORD
Monitoring time for the tool change
T_key
BOOL
Manual tool change key (NO )
A to D
BOOL
Tool position code signals
Strobe
BOOL
Position strobe
Lock_i
BOOL
Position clamping
OVload
BOOL
Turret motor overload (NC)
Tool position
Tool position code A
Tool position code B
Tool position code C
Tool position code D
1
0
1
0
0
2
0
0
0
1
3
1
0
0
0
4
0
0
1
0
5
1
1
1
0
6
1
0
1
1
7
1
1
0
1
8
0
1
1
1