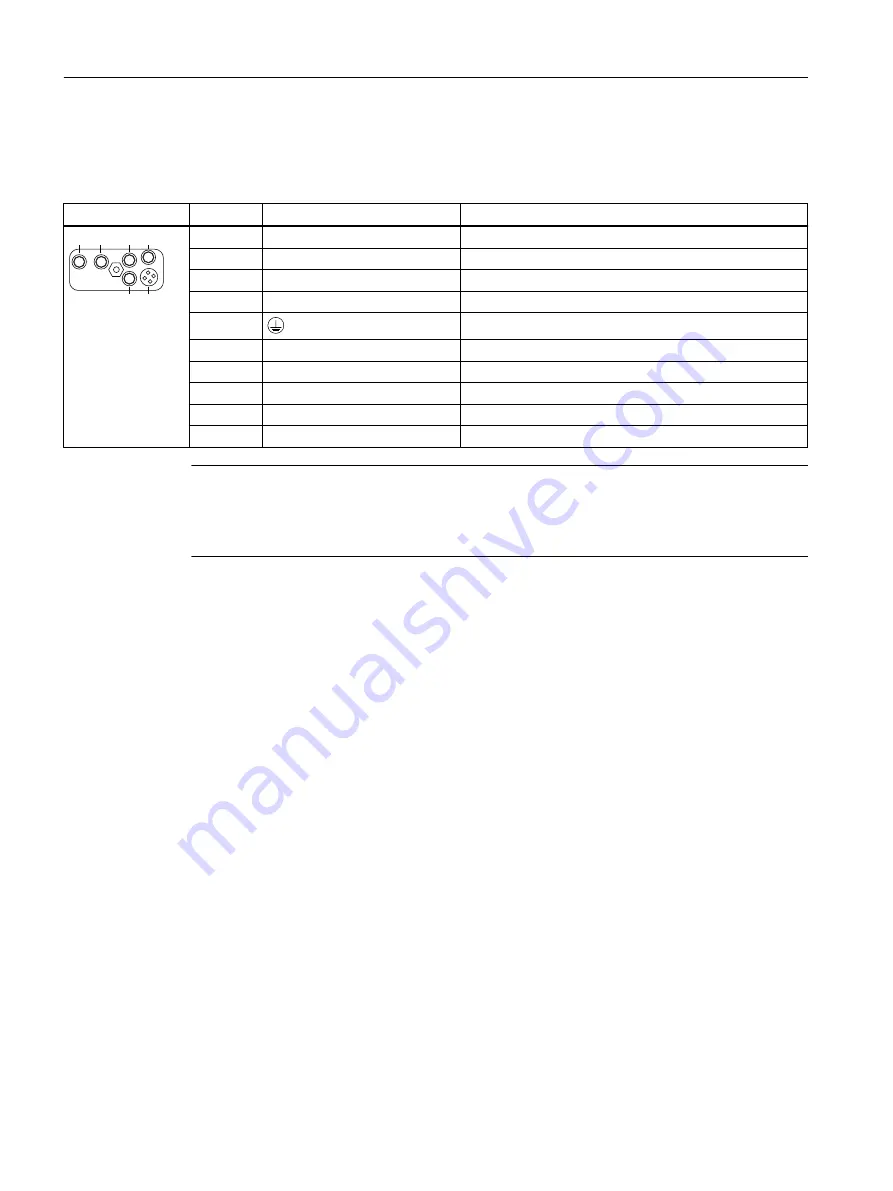
4.3.2
X1 hybrid connector
Table 4-1
X1 hybrid connector
Terminal
Signal name
Technical data
1
1 (TXP)
Transmit data +
2
2 (RXP)
Receive data +
3
3 (TXN)
Transmit data -
4
4 (RXN)
Receive data -
5
Protective conductor
6
M
Electronics ground
7
+
48 V power supply
8
DCN
DC link voltage - (M600)
9
DCP
DC link v (P600)
-
DQ_SHIELD
Shield
Note
Mounting the hybrid connector
You can screw on the hybrid connector by hand. For operation, tighten it with an Allen key (3.0
Nm / 26.6 lbf in).
Adapter Module 600
4.3 Interface description
60
Manual, 06/2019, 6SL3097-5AW00-0BP1
Содержание Sinamics S120M
Страница 1: ...Equipment Manual Distributed drive technology Edition www siemens com drives 06 2019 S120M SINAMICS ...
Страница 2: ......
Страница 20: ...Introduction 1 8 General Data Protection Regulation 18 Manual 06 2019 6SL3097 5AW00 0BP1 ...
Страница 32: ...Fundamental safety instructions 2 4 Residual risks of power drive systems 30 Manual 06 2019 6SL3097 5AW00 0BP1 ...
Страница 56: ...System overview 3 5 System Data 54 Manual 06 2019 6SL3097 5AW00 0BP1 ...
Страница 110: ...S120M 5 11 Motor holding brake 108 Manual 06 2019 6SL3097 5AW00 0BP1 ...
Страница 118: ...DRIVE CLiQ Extension 6 6 Technical data 116 Manual 06 2019 6SL3097 5AW00 0BP1 ...
Страница 126: ...Hybrid Cabinet Bushing 7 6 Technical data 124 Manual 06 2019 6SL3097 5AW00 0BP1 ...
Страница 182: ...Appendix A 2 Documentation overview 180 Manual 06 2019 6SL3097 5AW00 0BP1 ...
Страница 185: ......