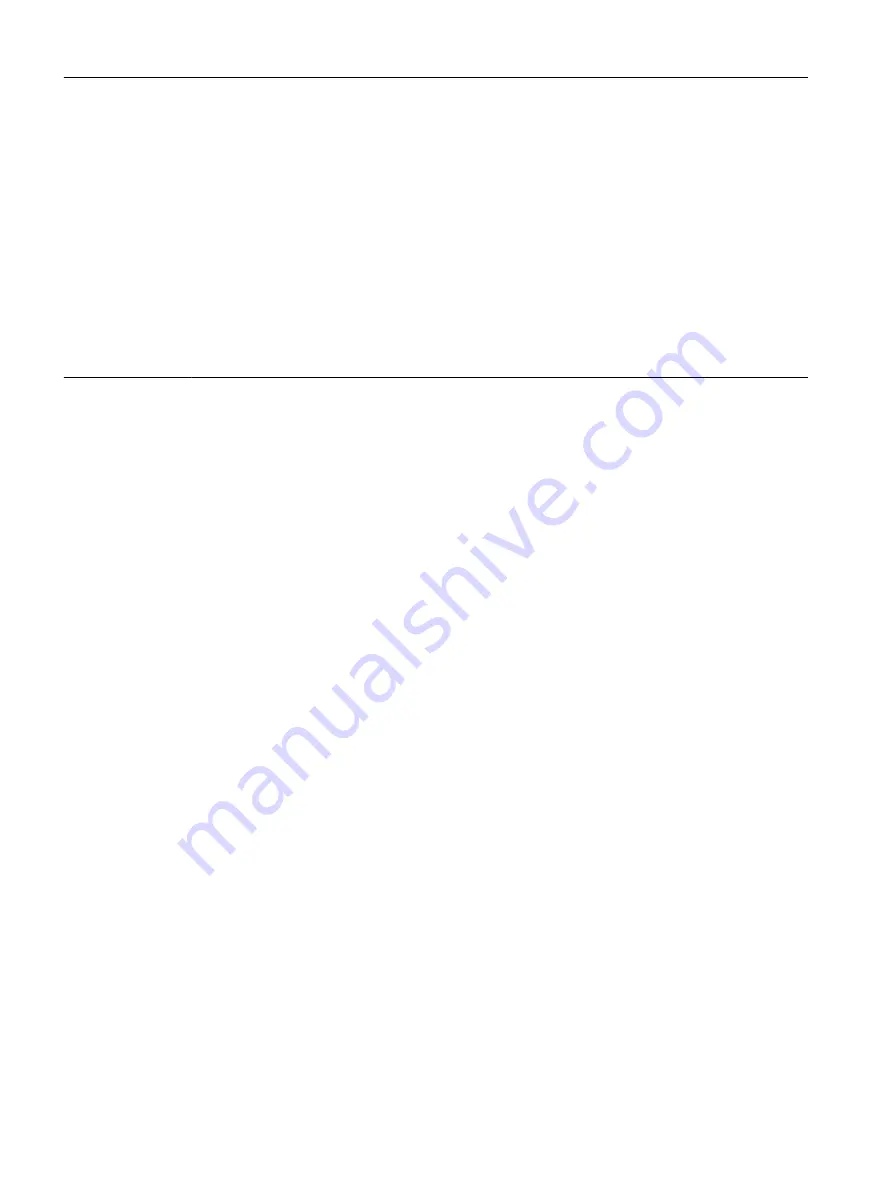
04
Switch-off signal path STO_A
Inactive
Active
-
05
Gating unit mode bit 1
ON
OFF
-
06
Gating unit mode bit 2
ON
OFF
-
07
Brake state
ON
OFF
-
08
Brake diagnostics
ON
OFF
-
09
Armature short-circuit braking
Active
Not active
-
10
Gating unit state bit 0
ON
OFF
-
11
Gating unit state bit 1
ON
OFF
-
12
Gating unit state bit 2
ON
OFF
-
13
Alarm status bit 0
ON
OFF
-
14
Alarm status bit 1
ON
OFF
-
15
Diagnostics 24 V
ON
OFF
-
p1900
Motor data identification and rotating measurement / MotID and rot meas
Access level: 2
Calculated: -
Data type: Integer16
Can be changed: C2(1), T
Scaling: -
Dynamic index: -
Unit group: -
Unit selection: -
Function diagram: -
Min:
0
Max:
12
Factory setting:
0
Description:
Sets the motor data identification and speed controller optimization.
The motor identification should first be performed with the motor stationary (p1900 = 1, 2; also refer to p1910). Based
on this, additional motor and control parameters can be determined using the motor data identification with the motor
rotating (p1900 = 1, 3; also refer to p1960; not for p1300 < 20).
p1900 = 0:
Function inhibited.
p1900 = 1:
Sets p1910 = 1 and p1960 = 0, 1 depending on p1300
When the drive enable signals are present, a motor data identification routine is carried out at standstill with the next
switch-on command. Current flows through the motor which means that it can align itself by up to a quarter of a
revolution.
With the following switch-on command, a rotating motor data identification routine is carried out - and in addition, a
speed controller optimization by making measurements at different motor speeds.
p1900 = 2:
Sets p1910 = 1 and p1960 = 0
When the drive enable signals are present, a motor data identification routine is carried out at standstill with the next
switch-on command. Current flows through the motor which means that it can align itself by up to a quarter of a
revolution.
p1900 = 3:
Sets p1960 = 0, 1 depending on p1300
This setting should only be selected if the motor data identification was already carried out at standstill.
When the drive enable signals are present, with the next switch-on command, a rotating motor data identification
routine is carried out - and in addition, speed controller optimization by taking measurements at different motor speeds.
p1900 = 11, 12:
The same as p1900 = 1, 2 with the difference, that after the measurement, the system immediately goes into operation.
For this purpose, p1909.18 is set = p1959.13 is set = 1 .
Value:
0:
Inhibited
1:
Identifying motor data and optimizing the speed controller
2:
Identifying motor data (at standstill)
3:
Optimizing the speed controller (in rotating operation)
11:
Motor data ident. and speed controller opt., switch to operation
12:
Motor data identification (at standstill), switch to operation
Parameters
7.3 Parameters
SINAMICS G120XA converter
540
Operating Instructions, 03/2019, FW V1.0, A5E44751205B AB
Содержание SINAMICS G120XA
Страница 2: ......
Страница 12: ...Table of contents SINAMICS G120XA converter 10 Operating Instructions 03 2019 FW V1 0 A5E44751205B AB ...
Страница 104: ...Wiring 4 2 Control interfaces SINAMICS G120XA converter 102 Operating Instructions 03 2019 FW V1 0 A5E44751205B AB ...
Страница 916: ...Index SINAMICS G120XA converter 914 Operating Instructions 03 2019 FW V1 0 A5E44751205B AB ...
Страница 917: ......