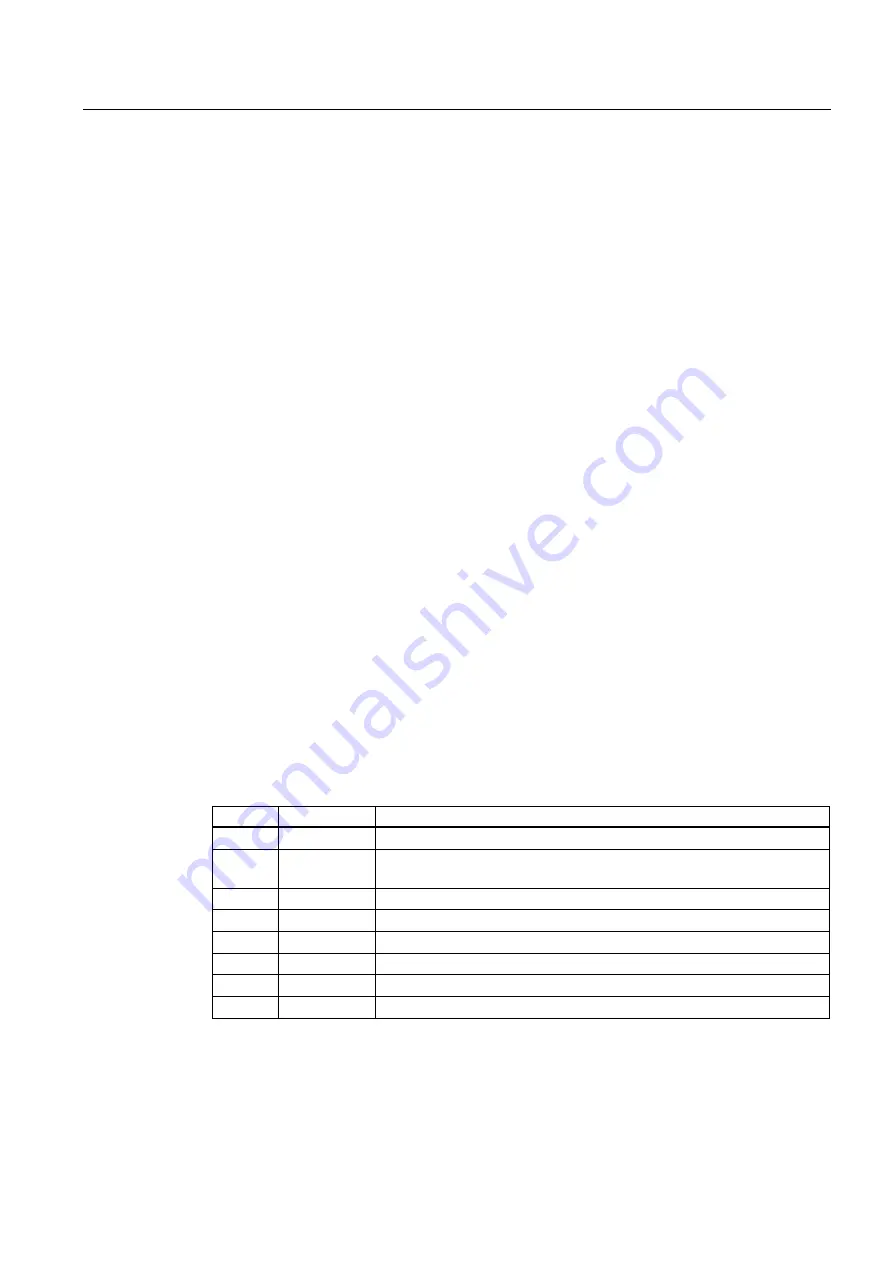
Functions
5.7 Closed-loop control
Frequency inverter
Operating Instructions, 08.10. 2008, t.b.d.
115
5.7.2.4
Using a speed encoder
Higher accuracy by using a speed encoder
A speed encoder increases the accuracy of the speed or the torque of the vector control for
speeds below approx. 10% of the rated motor frequency.
Commissioning the speed encoder
A speed encoder requires the following commissioning steps:
1.
Connect the speed encoder (refer below)
2.
Set the encoder voltage using the DIP switches on the CU (refer below)
3.
Set the speed encoder parameters (refer below)
4.
Set the frequency inverter to V/f control (P1300 = 0)
5.
Power-up the motor with an average speed
6.
Compare parameters r0061 (speed encoder signal in Hz) and r0021 (calculated speed in
Hz) regarding the sign and absolute value
7.
If the signs do not match, invert the speed encoder signal (P0410 = 1)
8.
If the absolute value of the two values do not correspond, check P0408, the speed
encoder wiring and the setting of the corresponding DIP switch
9.
Change over to vector control with speed encoder (P1300 = 21 or P1300 = 23)
Connect the speed encoder
An encoder can only be connected to CU240S, CU240S DP, CU240S DP-F, CU240S PN or
CU240S PN-F.
Only encoders with two pulse tracks A and B offset through 90° may be connected.
Table 5- 26 Terminals on the CU to connect the speed encoder
Terminal Designation
Function
28
U0V OUT
Reference potential of the power supply voltage (terminal 9)
33
ENC+
SUPPLY
Encoder power supply (5 V or 24 V set via DIP switch, max. 300 mA,
CU240S PN-F max. 200 mA)
70
ENC AP
Pulse track A, non-inverting input
71
ENC AN
Pulse track A, inverting input
72
ENC BP
Pulse track B, non-inverting input
73
ENC BN
Pulse track B, inverting input
74
ENC ZP
Zero signal, non-inverting input
75
ENC ZN
Zero signal, inverting input