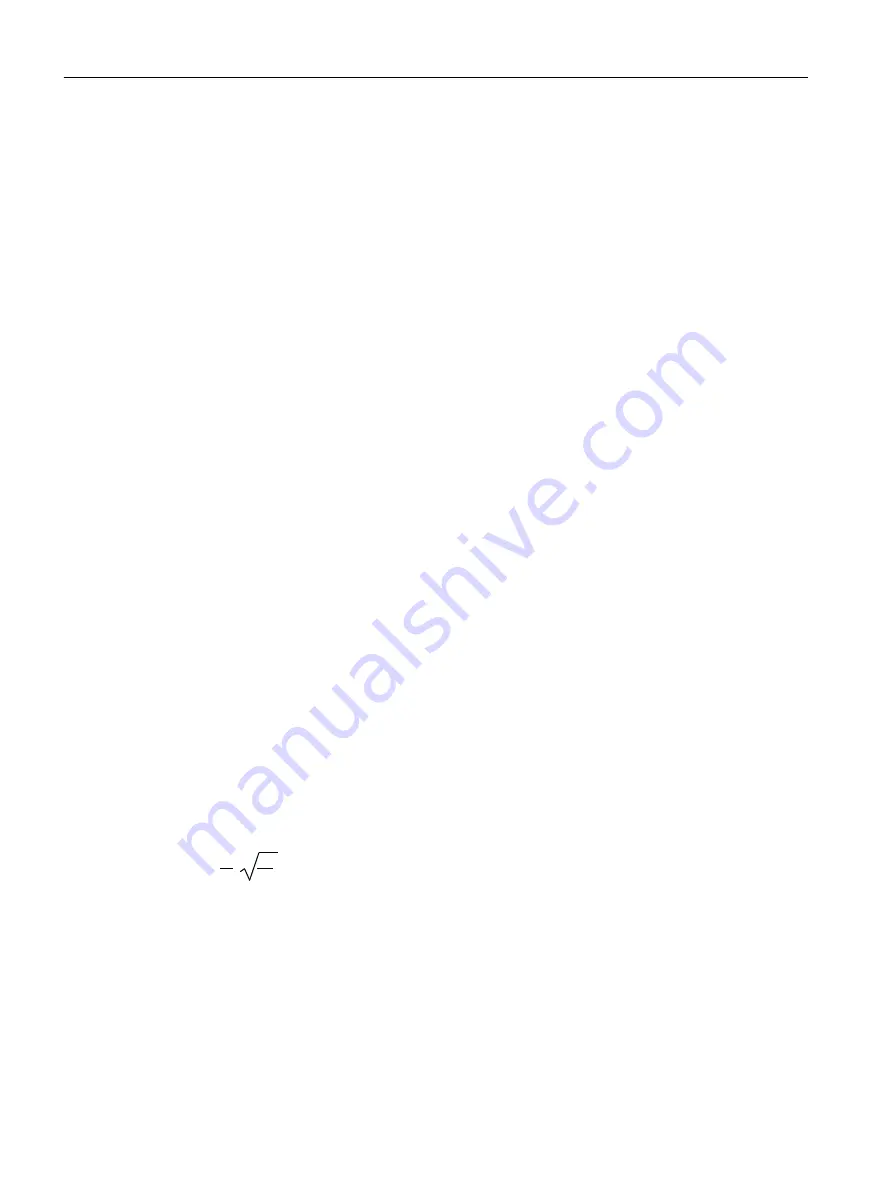
6.12.3
Time-optimized control
6.12.3.1
General information
The time-optimized algorithm calculates the ramps in such a way that, on reaching the desired
set velocity, oscillation is eliminated.
External influences that result in deviations are eliminated in the conventional way. This applies
particularly during stopping.
If time-optimized control is selected, the drive accelerates and decelerates with set
acceleration to the set velocity. The deceleration sections integrated in the acceleration
operations can be uncomfortable for the crane driver.
The time-optimized control method is based on the "optimum control theory". Short
deceleration ramps are inserted during acceleration and short acceleration ramps during
deceleration. This achieves the quickest possible suppression of a swaying motion. The
acceleration and deceleration times depend on the available drive power. The time restrictions
of the conventional control method do not apply.
6.12.3.2
Relaxation oscillations with GSU
Use of the time-optimized control method can excite relaxation oscillations at the grab,
especially with GSU cranes. Possible ways of reducing these are described below.
Reducing relaxation oscillations using a PT1 element (P38)
A PT1 element can be activated using parameter P38. This effect of this PT1 element is to
smooth the output velocity ramp.
Reducing relaxation oscillations using an input shaper (P39)
An input shaper can be used as an alternative for reducing relaxation oscillations.
The input shaper must be exactly matched to the grab-oscillation frequency. The grab-
oscillation frequency must be determined empirically.
To ensure correct operation of the input shaper, the grab frequency must not equal the load-
oscillation frequency. The load-oscillation frequency can be calculated as follows:
I
g
l
∏
g
Acceleration due to gravity
l
Effective pendulum length
Frequencies for typical grab oscillations at GSU cranes are between 0.4 Hz and 1 Hz. The
effective pendulum lengths typically vary between 5 m and 30 m, resulting in load pendulum
frequencies between 0.22 Hz and 0.091 Hz. This ensures the correct operation of the input
shaper because it can never match the grab frequency.
If, however, both frequencies are unexpectedly equal, the input shaper should not be deployed.
Sway Control function description
6.12 Selection of the control method
SC integrated STS, GSU
194
Operating Instructions, 07/2019, A5E48271265B AA