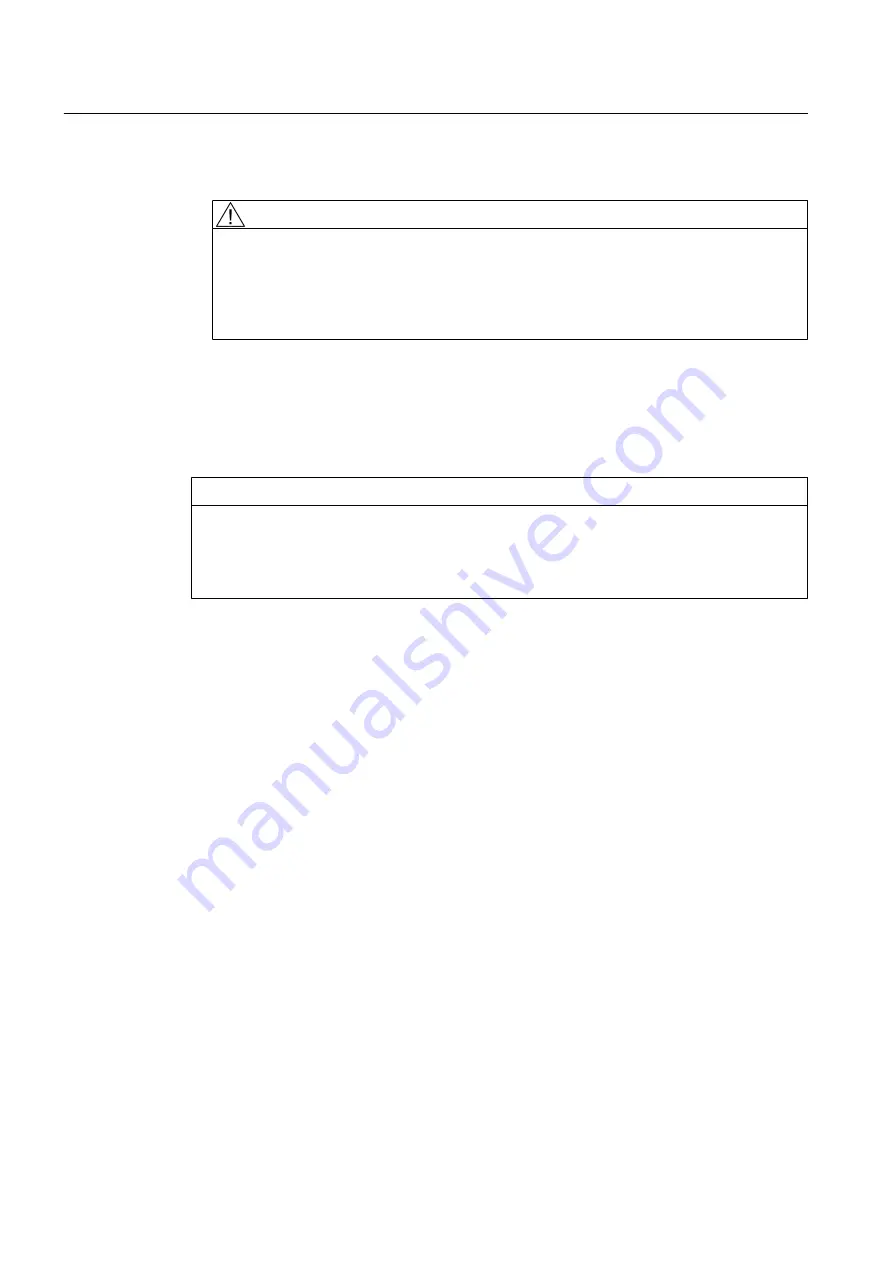
● Never remain under or in the immediate vicinity of the machine when it is lifted.
WARNING
Danger to life as a result of a machine falling
If the lifting gear or load handling attachments were to fail, the machine could fall. This
can result in death, serious injury or material damage.
● In order to gain easy and safe access to the underside of the machine, place it in a
secure and raised position.
4.12
Storage
You must correctly store the machine if you do not install and use it after it has been delivered.
NOTICE
Bearing seizure damage if incorrectly stored
If storage conditions are inappropriate there is a risk of bearing seizure damage. Resulting
damage can include scoring (brinelling) and corrosion.
● Follow the storage guidelines.
Preconditions and preparations
● Only store goods in undamaged packaging. Unpack the goods if the packaging is damaged.
Correctly store the goods corresponding to the type.
● Repair any damage to the packaging before putting the equipment into storage insofar as
this is necessary to ensure proper storage conditions.
Preparations for use
4.12 Storage
SIMOTICS HT Series HT-direct 1FW4...1......A
38
Operating Instructions 11/2018
Содержание SIMOTICS HT Series
Страница 2: ...13 11 2018 16 25 V5 00 ...
Страница 10: ...Table of contents SIMOTICS HT Series HT direct 1FW4 1 A 10 Operating Instructions 11 2018 ...
Страница 26: ...Description SIMOTICS HT Series HT direct 1FW4 1 A 26 Operating Instructions 11 2018 ...
Страница 62: ...Assembly 5 6 Insulated bearings SIMOTICS HT Series HT direct 1FW4 1 A 62 Operating Instructions 11 2018 ...
Страница 108: ...Maintenance 9 2 Corrective Maintenance SIMOTICS HT Series HT direct 1FW4 1 A 108 Operating Instructions 11 2018 ...
Страница 116: ...Disposal 11 7 Disposal of components SIMOTICS HT Series HT direct 1FW4 1 A 116 Operating Instructions 11 2018 ...
Страница 118: ...Service and Support SIMOTICS HT Series HT direct 1FW4 1 A 118 Operating Instructions 11 2018 ...
Страница 122: ...Quality documents SIMOTICS HT Series HT direct 1FW4 1 A 122 Operating Instructions 11 2018 ...
Страница 127: ......