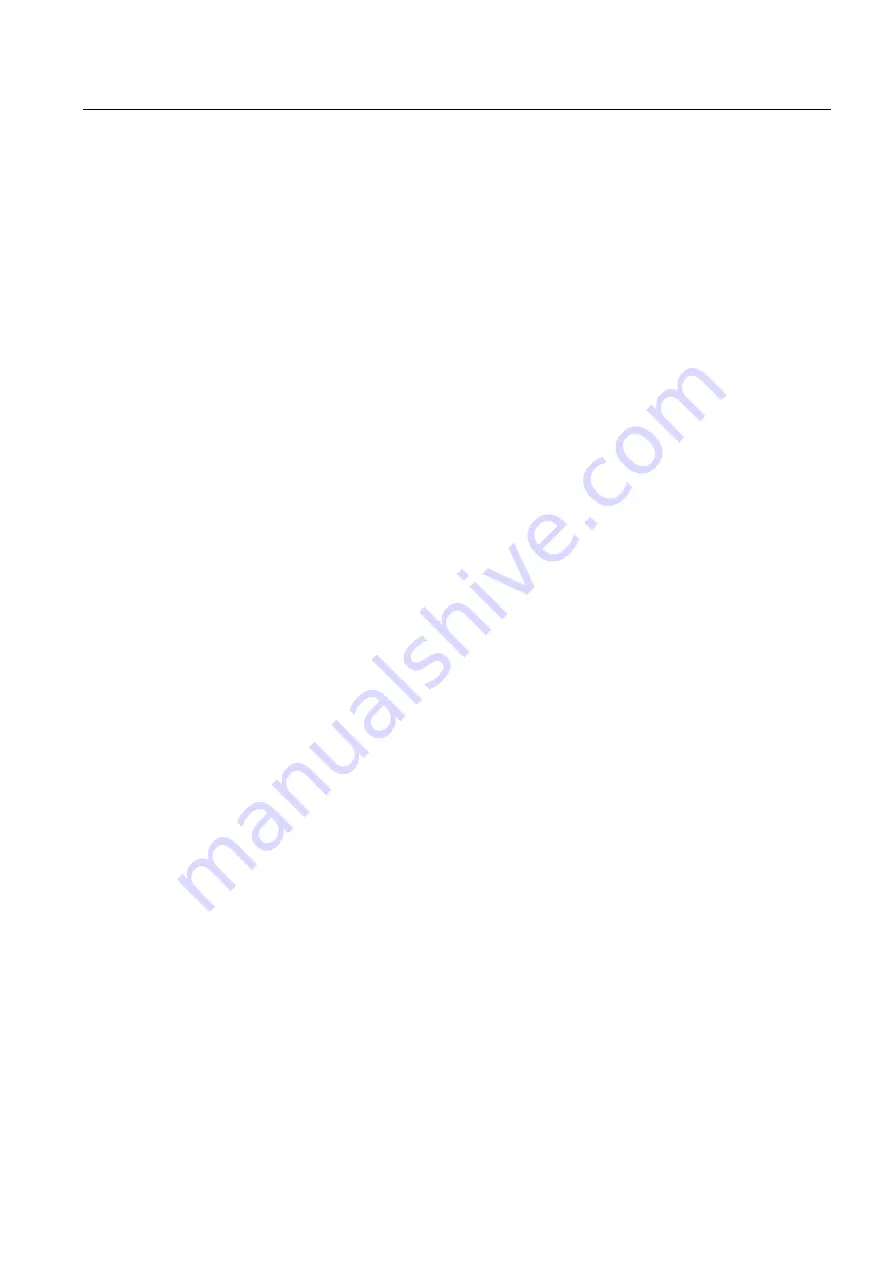
Safety in F-Systems
4.2 Safety Mode
Safety Engineering in SIMATIC S7
System Manual, 04/2006, A5E00109529-05
4-3
4.2
4.2
Safety Mode
Safety Mode
In safety mode, the safety functions for fault detection and fault reaction are activated in the
following:
•
Fail-safe I/O
•
Safety program of the F-CPU
Safety Mode of F-I/O
For S7-300 fail-safe signal modules, the "Safety mode" parameter setting in
HW Config
determines whether the modules are operated in standard mode (used as S7-300 standard
signal modules except for SM 326; DO 8 ☓ 24 VDC/2 A) or in safety mode.
ET 200S, ET 200pro and ET 200eco fail-safe modules can only be used in safety mode.
Safety Mode of Safety Program
The safety program runs in the F-CPU in safety mode. This means that all safety
mechanisms for fault detection and fault reaction are activated. The safety program cannot
be modified during operation in safety mode.
Safety mode of the safety program in the F-CPU can be deactivated and reactivated
occasionally. So-called "deactivated safety mode" enables the safety program to be tested
online and changed as needed while the F-CPU is in RUN mode.
For S7 Distributed Safety, you can switch back to safety mode only after an operating mode
change from RUN to STOP to RUN.
For S7 F/FH systems, an operating mode change is not needed to return to safety mode.
Safety Message Frame
In safety mode, data are transmitted consistently between the F-CPU and F-I/O in a safety
message frame. The safety message frame in accordance with PROFIsafe consists of the
following:
•
Process data (user data)
•
Status byte/control byte (coordination data for safety mode)
•
Sequence number
•
CRC signature
Safety-related CPU-CPU communication also takes place using a safety message frame
similar to PROFIsafe. The following information on monitoring time, sequence number, and
CRC signature is also applicable.