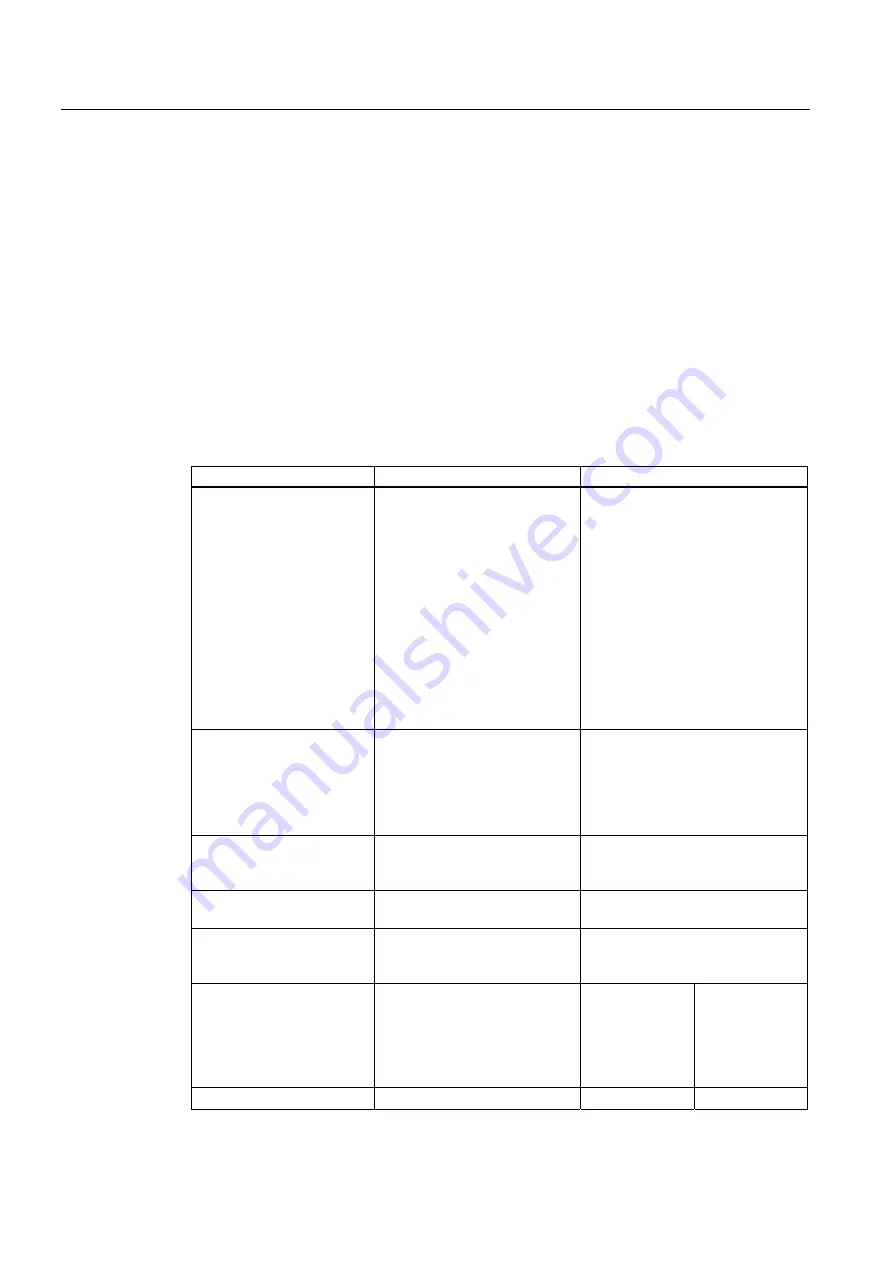
Configurations and Help with Selection
2.4 S7 Distributed Safety or S7 F/FH Systems – Selection Guide
Safety Engineering in SIMATIC S7
2-22
System Manual, 04/2006, A5E00109529-05
2.4
2.4
S7 Distributed Safety or S7 F/FH Systems – Selection Guide
The Automation Task
The right solution for every automation task – for the user, this means achieving the optimum
price-performance ratio.
S7 Distributed Safety or S7 F/FH Systems – Selection Criteria
The following table lists the principal F-system requirements that are critical for selection.
The last row of the table indicates which fail-safe system – S7 Distributed Safety, S7 F
Systems, or S7 FH Systems – is best suited for the automation task at hand.
Table 2-2
Selection Citeria for an F-system
Selection criteria
Applicable F-I/O on
PROFIBUS DP
•
F-signal modules in
ET 200M
•
F-signal modules in
S7-300 station (centralized
configuration with
CPU 315F-2 DP, for
example)
•
F-electronic modules in ET
200S
•
Fail-safe electronic modules
in ET 200pro
•
ET 200eco fail-safe I/O
module
•
Fail-safe DP standard slaves
•
F-signal modules in ET 200M
•
F-electronic modules in ET
200S
•
ET 200eco fail-safe I/O module
•
Fail-safe DP standard slaves
Applicable F-I/O on
PROFINET IO
•
F-electronic modules in
ET 200S
•
Fail-safe electronic modules
in ET 200pro
•
Fail-safe I/O standard
devices
-
Requirement for typical
response time of the F-
system
100 ms to 200 ms
200 ms to 500 ms
Integration in a control
system
Integration not required
Integration in a PCS 7 process
control system required
Requirement for
programming language
Standard programming
languages (LAD, FBD) in
STEP
7
must be used
CFC must be used for programming
(simple integration in a control
system possible)
Availability requirement for
the F-system
Normal availability of the
F-system is sufficient
Normal
availability is
sufficient
Increased
availability or
highest
level of
availability is
required
Solution...
S7 Distributed Safety
S7 F Systems
S7 FH Systems