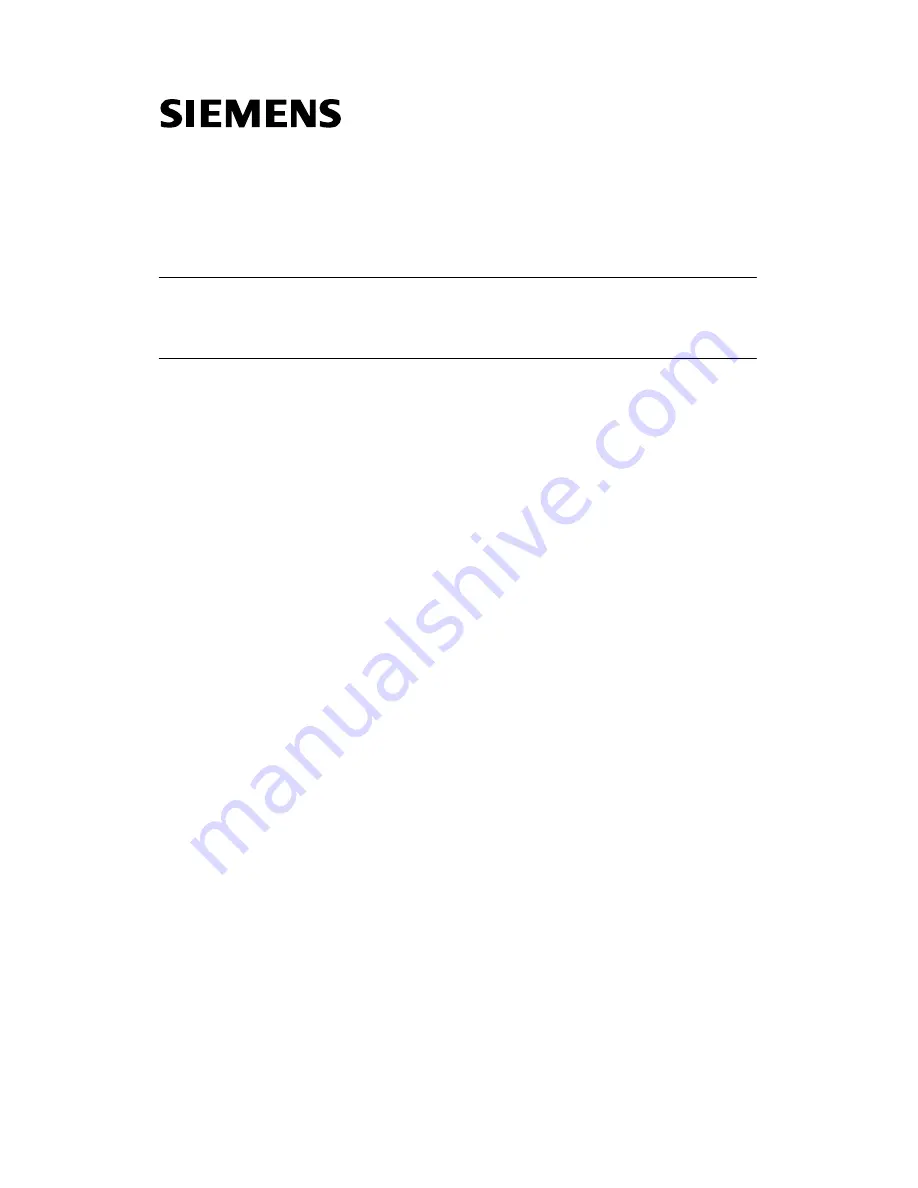
Copyright 2005 by Siemens AG
A5E00409892-01
Product Information on the Reference Manual
Programmable Logic Controllers S7-300 Module Data Release 3
1
Position Decoder Module SM 338; POS-INPUT;
(6ES7338-4BC01-0AB0)
Order number
6ES7338-4BC01-0AB0
Characteristics
The position decoder module SM 338; POS-INPUT is distinguished by the
following features:
•
3 inputs for the connection of maximum three absolute value encoders (SSI)
and 2 digital inputs to freeze the encoder values
•
Direct reaction possible to encoder values in moving systems
•
Processing of acquired encoder values of the SM 338 in user program
•
Supports clocked operation
•
Type of encoder value acquisition (see chapter 1.1.2.1) can be selected:
– Free running
– Clocked
•
24 VDC rated input voltage
•
Non-isolated against the CPU
•
Fast mode selectable; with faster encoder recording and compressed
checkback interface
Fast mode is available as of SM 338; POS-INPUT firmware version V2.0.0 and
as of STEP 7 V5.3+SP2 selectable.