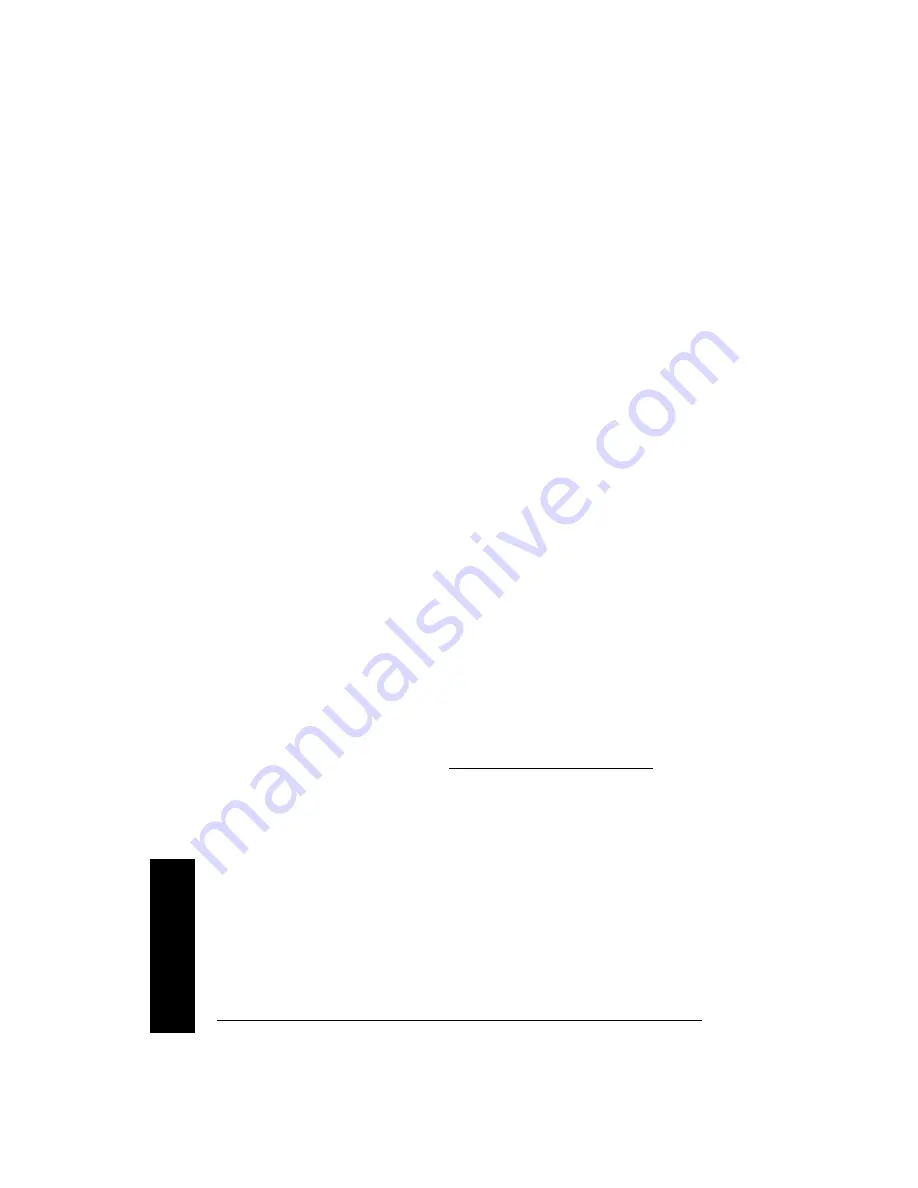
Page 16
Pointek CLS500 – INSTRUCTION MANUAL
7ML19985GG03
mmm
mm
P
robe Configur
at
io
n
High pressure and high temperature applications
For high temperature and pressure applications (greater than 200 bar) with conductive
liquids, contact your local Siemens representative.
For more details on configuration, see
Appendix E: Pointek CLS500, dimensions and
Electrode Assembly
Pointek CLS500 electrodes come in a variety of formats to provide the necessary
characteristics for correct mounting, chemical compatibility, temperature and pressure
requirements, and dielectric constant of the medium. The main body of the manual
discusses the standard configuration. Dimensions are shown in
CLS500, dimensions and application examples
Pointek CLS500: Standard Level Version
Available with the following features:
• Threaded flanges, welded flanges, and single-piece flanges
• HP series and HT series process seals
• Selections of standard ANSI and DIN flanges
• The most common electrode is insulated with PFA. Enamel (HP seal) is also
available.
• Various process connection materials
• Rod version only
Process Connections
The standard threaded process connection with PFA insulated electrode, including the
active shield, provides good results in all measurement situations within the temperature,
pressure, and corrosive capabilities of the materials and seals. This remains true over a
wide range of dielectric constants in both non-conducting and conducting materials.
Any standard process connection is available with Pointek CLS500, and special versions
can be fabricated to match the mounting and application requirements. A wide range of
threaded and flanged fittings is available. (Contact your local Siemens Milltronics
representative, or check our website at www. siemens.com/processautomation).
Seal Types
The basic internal seal for Pointek CLS500 has a conical-shaped, preloaded pressure/leak
resistant construction. Up to three levels of seal protection are implemented depending
on the integrity requirements of the application. A single or double cone internal seal
forms one or two barriers against leaking, and a third flange face gasket is also available
in the D and DD seal construction. The flange face seal also provides a design with no
metal wetted parts if required.