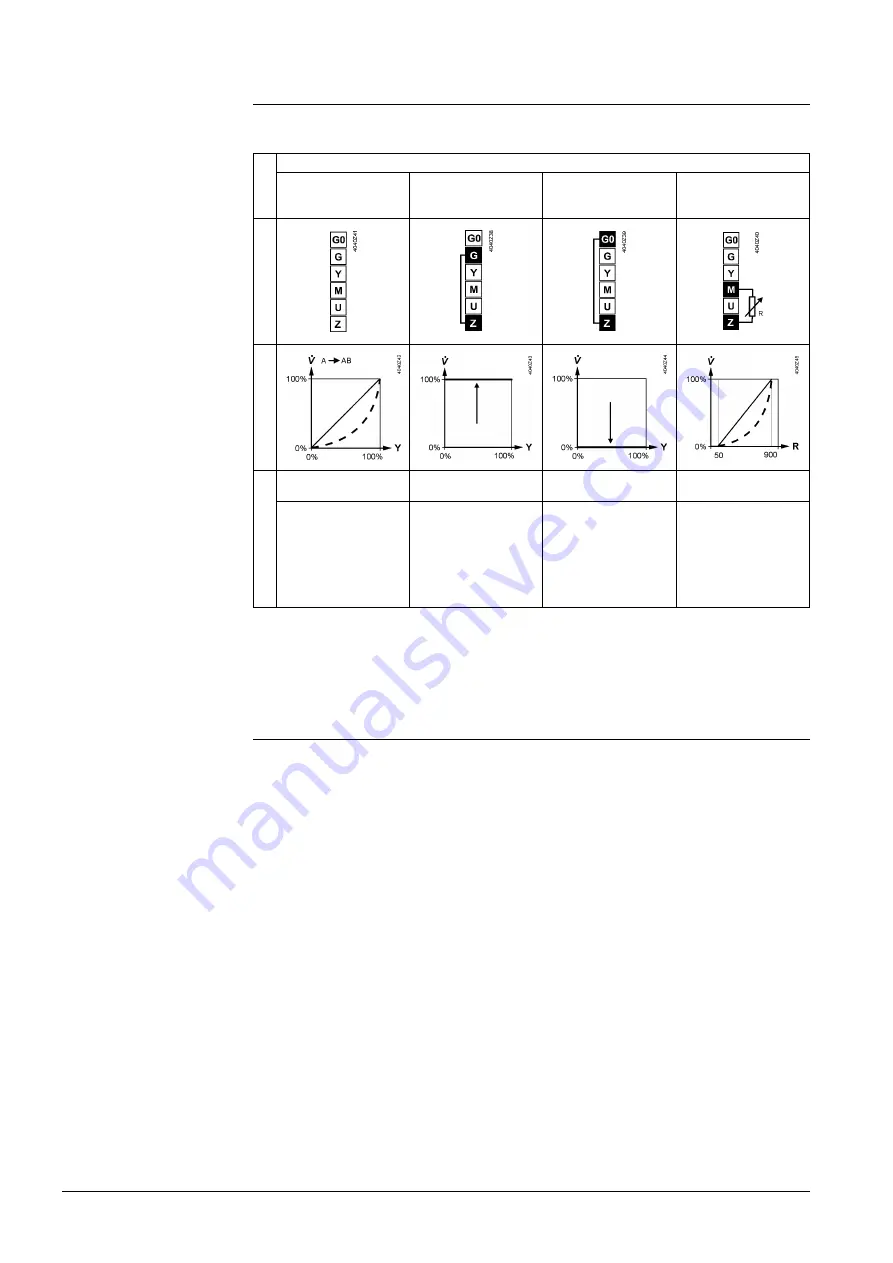
36 / 60
Siemens
Actuators SAS.., SAT.. for valves
CE1P4041en
Smart Infrastructure
Functions
and control
2019-04-09
4.2.7
Forced control Z
Forced control uses the following operating modes:
Z mode
No function
Fully open
Fully closed
Overriding
positioning signal “Y“
by 0…1000
Ω
Conn
ec
tion
s
T
ran
s
mi
s
si
on
Equal-percentage or
linear characteristic
Equal-percentage or
linear characteristic
Contact “Z“ not
connected,
valve follows
positioning signal ”Y”
Contact “Z“ is
connected directly to
“G“,
positiong signal ”Y”
has no impact
Contact “Z“ is
connected directly to
“G0“,
positiong signal ”Y” has
no impact
Contact “Z“ is
connected to “M“ via
resistor “R“,
starting point at 50
Ω
,
end point at 900
Ω
,
positioning signal ”Y”
has no impact
4.3
Communicating actuators Modbus RTU
4.3.1
Detection of valve seat
The actuators feature force-dependent valve seat detection. After calibration, the
exact valve stroke is filed in the actuator’s memory.
If no force is built up in the calculated end position (e.g. in the event of temperature
effects for instance), the actuator continues to operate at a reduced positioning
speed until the nominal positioning force is restored. This ensures that the valve
always fully closes.
After a power failure, valve seat identification is not active – the actuators without
fail safe function define their stroke position upon return of power at 50%. And sets
its internal setpoint in register 1 to 0%. The actuator closes at this setting. There is
a short-term deviation between the setpoint and the internal stroke position that
results in an error message in register 769 “Mechanical error, device blocked”. The
error message disappears after just a few seconds.
When the valve plug reaches its seat for the first time, the actuator readjusts its
stroke mode.
Setpoint prior to power outage 35%, no manual adjustment during the power
outage. Internal stroke position value after return of power 50%. Internal setpoint
after return of power 0%. There is an error message for a brief time prior to the
actuator moving since the setpoint of 0% is not equal to the position feedback of
SAS..
Example