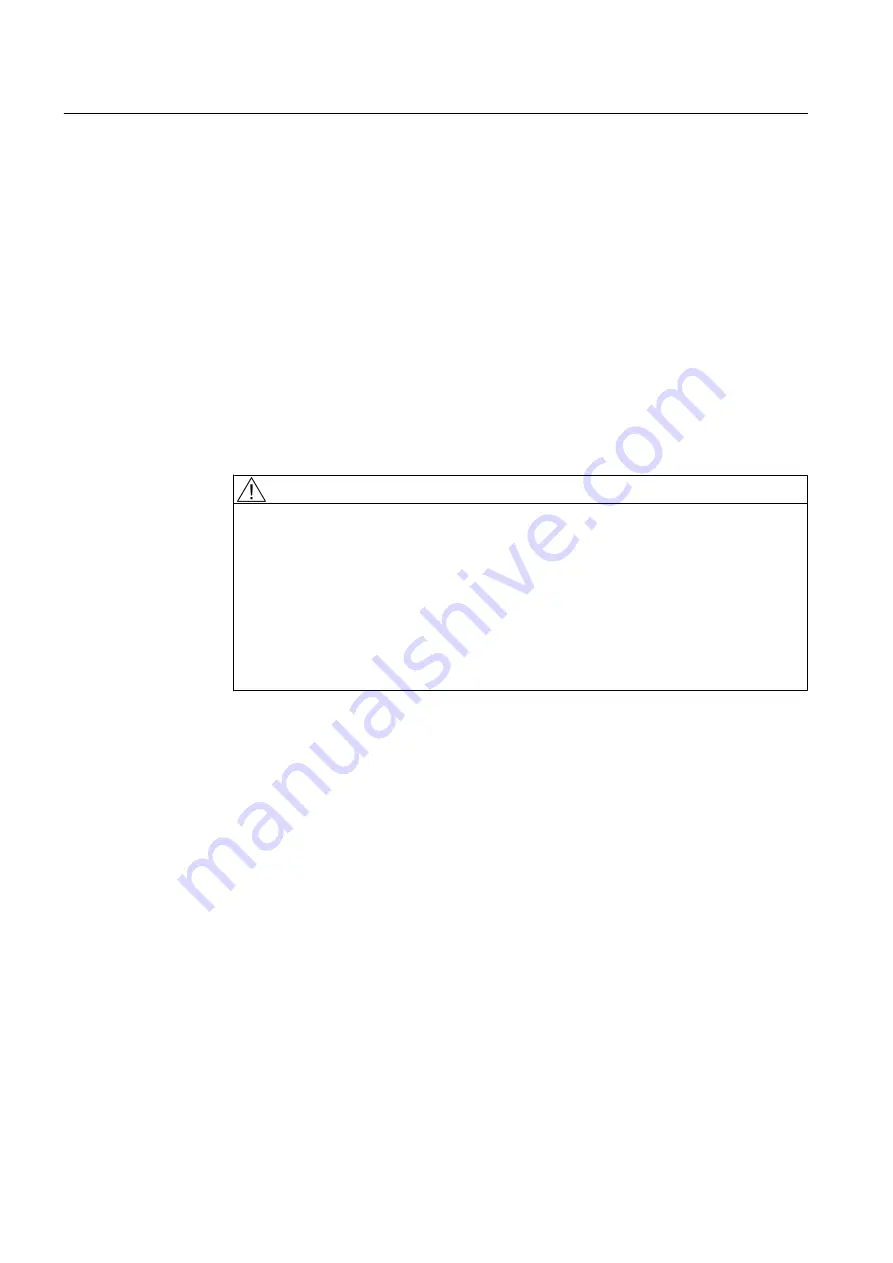
6.3.7
Finishing connection work
1. Before closing the terminal box, please check that:
– The electrical connections in the terminal box are tight and in full compliance with the
specifications above
– The motor is connected so that it rotates in the direction specified
– The inside of the terminal box is clean and free of any cable debris
– All gaskets and seals are intact
– Unused cable glands must be replaced with certified closures or closed with other
suitable closure types. Comply with the installation and operation conditions specified
in the certificate for these plug elements and check that they have been complied with.
– The pressure relief device is intact Depending on the type of terminal box being used,
the pressure relief device can be implemented either by sealing the slots or by using a
pressure relief diaphragm.
WARNING
Damaged pressure relief device
Water and foreign bodies can penetrate the enclosure if the pressure relief device is
damaged: The degree of protection of the terminal box is no longer guaranteed, a short-
circuit can occur, which can result in death, serious injury or material damage.
● Do not operate the machine with a damaged pressure relief device.
● Any damage may only be repaired after prior discussion with the person responsible
for the safety of the plant or system and only using original parts. Any damage may
only be repaired after prior discussion with the person responsible for the safety of
the installation and only by using original parts.
2. Close the terminal box.
See section "Tightening torques for screw and bolt connections (Page 113)" for the
tightening torque of the fixing bolts for the cover.
6.4
Connecting the auxiliary circuits
6.4.1
Selecting cables
Take the following criteria into account when selecting the connecting cables for the auxiliary
circuits:
● Rated current
● Rated voltage
● System-dependent conditions, such as ambient temperature, routing type, etc.
● Requirements according to IEC/EN 60204‑1
● Requirements according to GB 3836.15
Electrical connection
6.4 Connecting the auxiliary circuits
SIMOTICS HV C 1NB1402-2AA84-4CA0-Z
64
Operating Instructions 06/2018
Содержание 1NB1402-2AA84-4CA0-Z
Страница 2: ...26 06 2018 15 34 V3 00 ...
Страница 10: ...Table of contents SIMOTICS HV C 1NB1402 2AA84 4CA0 Z 10 Operating Instructions 06 2018 ...
Страница 22: ...Description SIMOTICS HV C 1NB1402 2AA84 4CA0 Z 22 Operating Instructions 06 2018 ...
Страница 84: ...Operation 8 9 Faults SIMOTICS HV C 1NB1402 2AA84 4CA0 Z 84 Operating Instructions 06 2018 ...
Страница 110: ...Disposal 11 4 Disposal of components SIMOTICS HV C 1NB1402 2AA84 4CA0 Z 110 Operating Instructions 06 2018 ...
Страница 112: ...Service and Support SIMOTICS HV C 1NB1402 2AA84 4CA0 Z 112 Operating Instructions 06 2018 ...
Страница 117: ...117 ...
Страница 118: ...118 ...
Страница 119: ...119 ...
Страница 120: ...120 ...
Страница 121: ...121 ...
Страница 122: ...122 ...
Страница 123: ...123 ...
Страница 124: ...124 ...
Страница 125: ...125 ...
Страница 126: ...126 ...
Страница 127: ...127 ...
Страница 128: ...128 ...
Страница 129: ...129 ...
Страница 130: ...130 ...
Страница 131: ...C 2 Declaration of conformity SIMOTICS HV C 1NB1402 2AA84 4CA0 Z Operating Instructions 06 2018 131 ...
Страница 132: ...Quality documents C 2 Declaration of conformity SIMOTICS HV C 1NB1402 2AA84 4CA0 Z 132 Operating Instructions 06 2018 ...
Страница 133: ...133 ...
Страница 148: ...148 ...
Страница 150: ...Additional documents SIMOTICS HV C 1NB1402 2AA84 4CA0 Z 150 Operating Instructions 06 2018 ...
Страница 154: ...Index SIMOTICS HV C 1NB1402 2AA84 4CA0 Z 154 Operating Instructions 06 2018 ...
Страница 155: ...AF Einbauerklärung Loher LDX U157 AJ EC Declaration of Conformity U161 ...