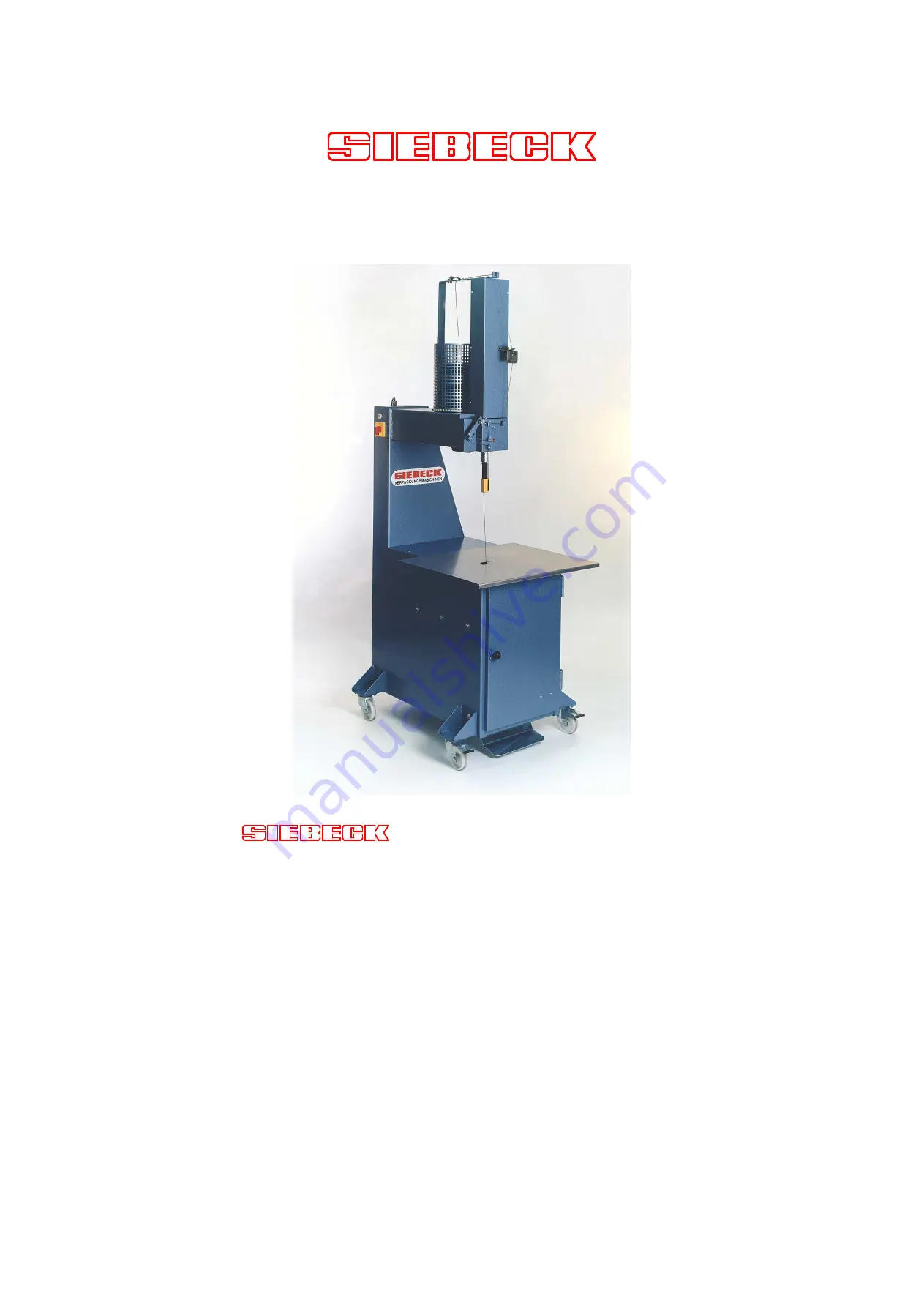
Translation of the original operating manual
Nr.: rbm_bed_0910
JET 2000 tying machine
Model JET - RBM
GMBH
D - 69412 EBERBACH
Tel49(0)6271 / 9208 0
Fax +49(0)6271 / 9208 88
E-mail: [email protected]
Internet: www.siebeck.de