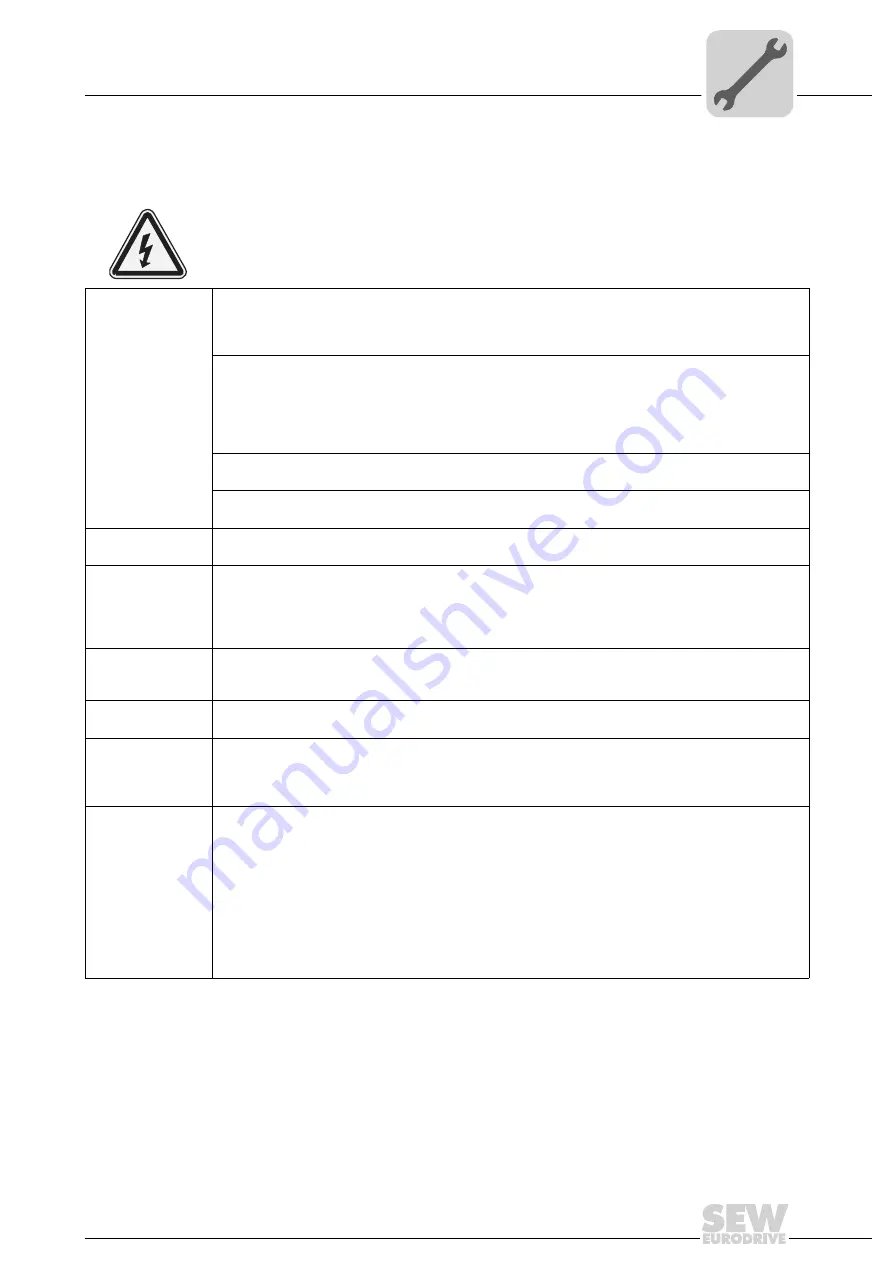
4
Installation
Installation notes
Operating Instructions Basic Unit – MOVITRAC
®
B
13
4
Installation
4.1
Installation notes
Comply with the safety notes during installation.
Tightening torques
Basic unit power terminals:
•
Only use
genuine connection elements
. Note the
permitted tightening torques
of
MOVITRAC
®
B power terminals.
– Size 0S / 0L: 0.5 Nm (4.4 lb.in)
Line choke:
•
ND020-013: 0.6 ... 0.8 Nm
•
ND027-123: 4.0 ... 4.5 Nm
•
ND035-073: 4.0 ... 4.5 Nm
•
ND010-301: 0.6 Nm
•
ND020-151: 1.5 Nm
Line filter:
•
NF009-503: 0.6 ... 0.8 Nm
Output filter:
•
HF008 / 015 / 022 / 030 / 040-503: 1.6 Nm ± 20 %
Recommended
tools
•
Use a screwdriver with a 2.5 mm wide blade for connecting the electronics terminal strip X10 /
X12 / X13.
Minimum
clearance and
mounting position
•
Leave
100 mm (4 in) clearance at the top and bottom
for optimum cooling. There is no need
for clearance at the sides. You can line up the units directly next to one another. Make sure that
the circulation of air is not disrupted by cables or other installation materials. Prevent the
heated exhaust air from other units from blowing onto this unit.
Install the units vertically
only.
You must not install them horizontally, tilted or upside down.
Line choke
•
When more than four
3-phase units
or
more than one 1-phase unit
are connected to a
supply system contactor
designed for the total current:
Insert a line choke
in the circuit to
limit the inrush current.
Separate cable
ducts
•
Route power leads and electronics leads in separate cable ducts.
Fuses and earth-
leakage circuit
breaker
•
Install
input fuses at the start of the supply system lead
after the supply bus junction.
Use D, DO, NH fuse types or power circuit breakers.
Earth-leakage circuit breaker as sole protection device:
Only use earth leakage circuit
breakers type B according to EN 61800-5-1.
PE input
connection
•
Connect the PE conductor according to the relevant regulations that are applicable in the
specific country.
Connect the protective earth connector of the motor to the PE terminal of the corresponding
inverter.
Ground all units over a large area via short ground connections with large cross-section to a
mutual earthable point or a grounding bar.
Make sure the connection between inverter and earthed metallic installation platform is conduc-
tive (large area metal-on-metal contact between the heat sink and ground, e.g. unpainted
control cabinet mounting panel). Use high-frequency compatible earthing strips if necessary).
Establish a high-frequency equipotential bonding between system / control cabinet and drive /
motor (e. g. by a continuous cable rack).