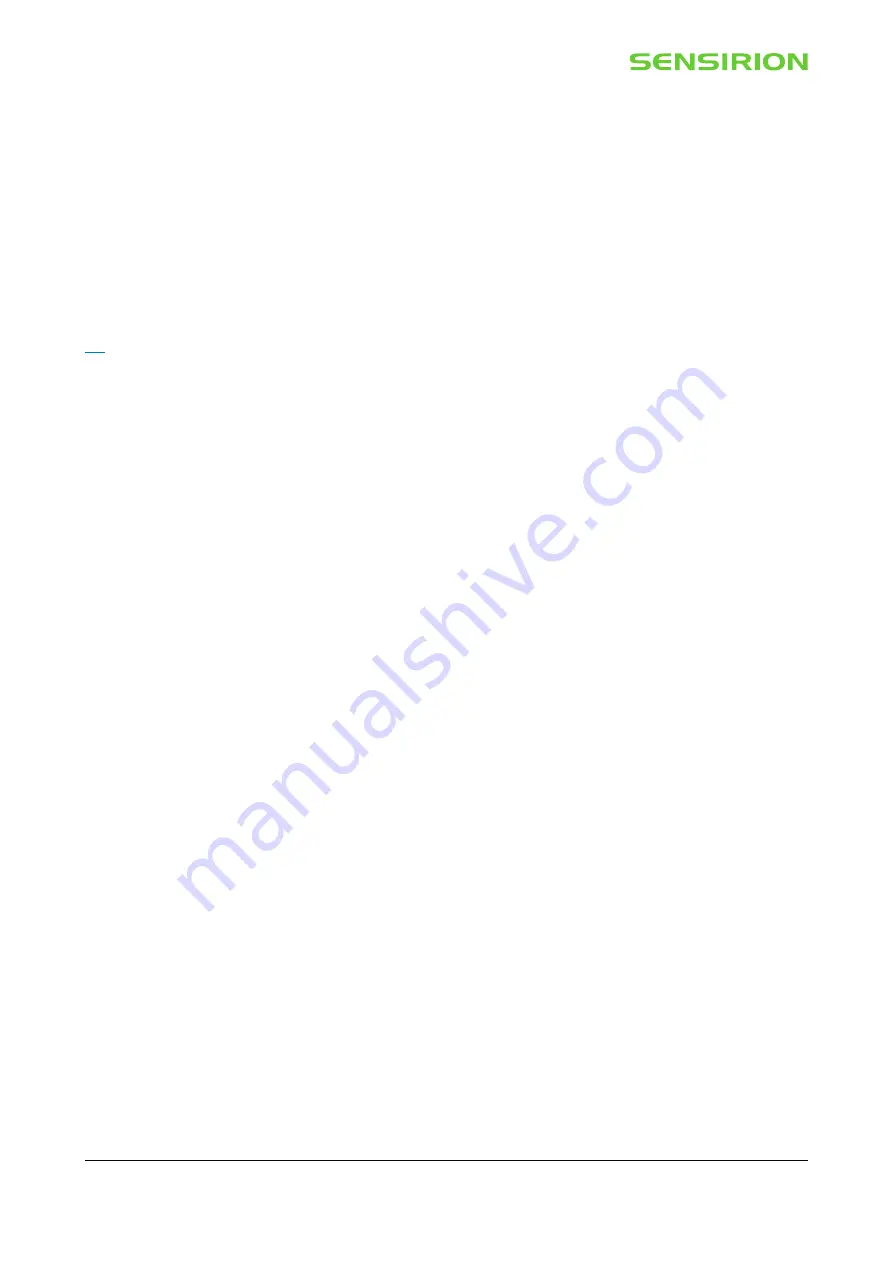
www.sensirion.com
Version 1.0
–
Aug 2022
5 / 11
Copyright © Sensirion AG 2022.
4.
Common pitfalls
4.1.
Flow appears to be off by several %
If the flow appears to be off by several % (especially around 7%) against your reference, there are good chances the flow
units of the two devices are not the same. Sensirion’s Mass Flow Controllers ca
n be factory calibrated for different units:
e.g. standard or norm litres. The conversion difference between the two is around 7%, due to the different reference
temperatures used for standard and norm litres. Please make sure that the Mass Flow Controller and your reference are
using the same units when testing. Further information about the flow unit conversion can be found in a dedicated
application note, “
Reference and Flow Conversions between mass and volumetric flow
”,
in the “Useful resources”
Section
4.2.
Settling time is longer than specified
The most common cause for observing longer than expected settling time is trying to verify it from a position of fully closed
valve. Solenoid valves are commonly affected by so-
called “stiction effect”.
To open the valve from closed position (setpoint
0), a certain overvoltage is required to overcome the stiction effect. This can lead to a spike in the flow (especially for low
setpoints) or a longer than expected settling time. By adjusting the “user gain”
of the Mass Flow Controller, the behaviour
can be tuned to the specific requirements.
The settling time of Sensirion’s Mass Flow Controllers is specified for a s
tep answer from 10% to 100% of full scale within
5% of setpoint. When testing the settling time, do not do so from a position of zero flow.
5.
Design recommendations
To achieve best accuracy, it is recommended to use a design where the Mass Flow Controller is mounted horizontally.
The valve used in the Mass Flow Controllers (proportional valve) is an oscillating system. Try to avoid sources of vibrations
or decouple these sources mechanically from the Mass Flow Controller. They can interfere with the proper function of the
valve.
The operation of the valve produces a significant amount of heat. The Mass Flow Controller should therefore not be placed
in a hermetically sealed space. It is recommended to design a cooling flow over the Mass Flow Controller in order to
counteract the heating from the valve. Large temperature gradient between the Mass Flow Controller and the gas it is used
to control, may adversely influence the accuracy of the device.
5.1.
Pressure drop and input pressure
Pressure drop is generated when gas passes through the valve of a mass flow controller. The magnitude of the pressure
drop is proportional to the flow rate and the density of the gas.
It is important to verify that at the maximum required flow rate, for a given gas, the inlet pressure is higher than the pressure
drop. If this cannot be achieved, contact Sensirion
–
it might be possible to order a similar mass flow controller with larger-
sized valve. Larger valves offer a lower pressure drop at the cost of a decreased accuracy/resolution at low flows.