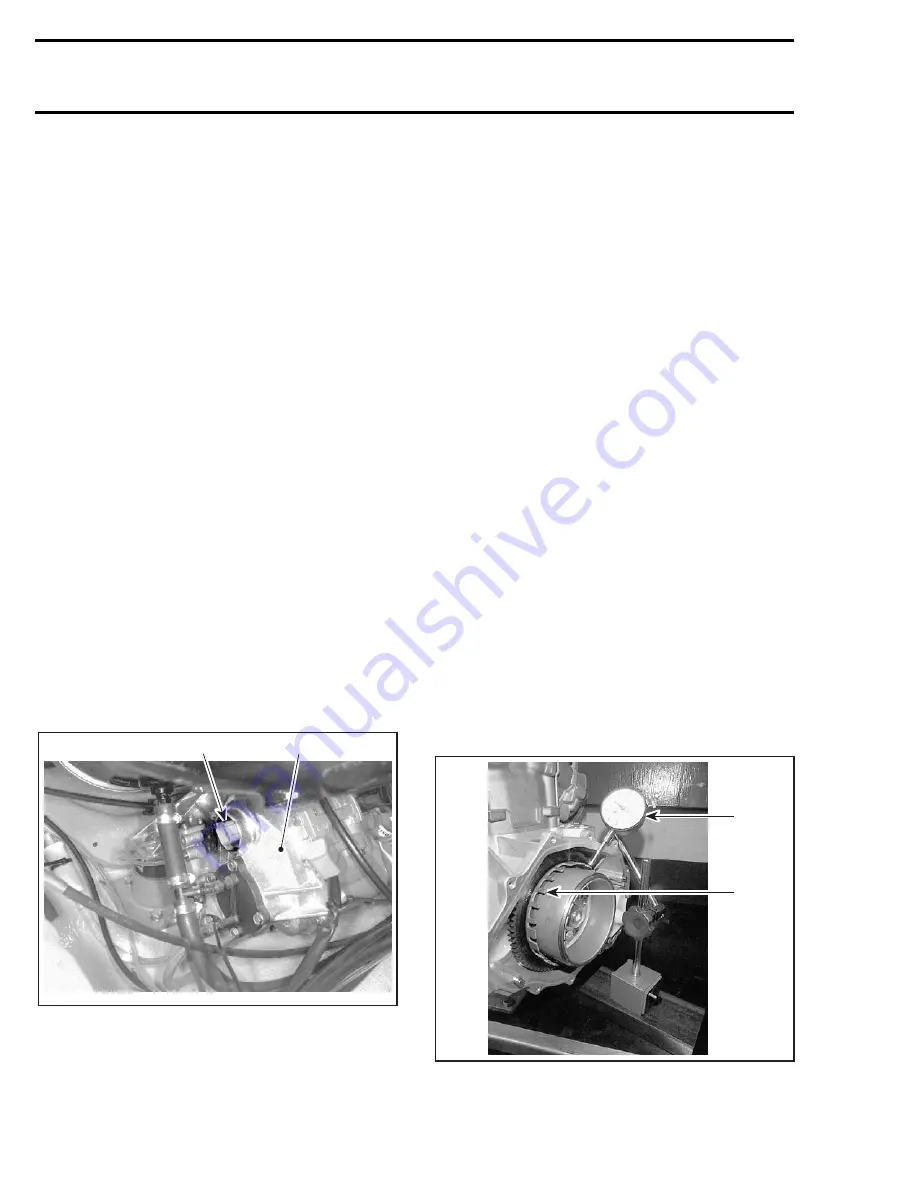
Section 07
ENGINE MANAGEMENT (DI)
Subsection 03
(COMPONENT INSPECTION AND ADJUSTMENT)
07-03-26
SMR2003_024 _07_03A.FM
CAUTION:
An improperly adjusted TPS may
lead to poor engine performance and emission
compliance could possibly be affected.
Use the vehicle communication kit (VCK) with the
B.U.D.S. software to perform this adjustment.
Ensure the throttle body plate stop lever rests
against its stopper. Open throttle approximately one
quarter then quickly release. Repeat 2 - 3 times to
settle throttle plate. If stopper does not rest against
its stop lever, perform throttle cable adjustment. Re-
fer to THROTTLE BODY in AIR INDUCTION SYS-
TEM
above.
Push the
Reset
button in the SETTING section of
B.U.D.S.
NOTE:
There is no idle speed adjustment to per-
form. The MPEM takes care of that. If TPS are not
within the allowed range while resetting the
closed TPS, the MPEM will generate a fault code
and will not accept the setting. To solve that, per-
form the
Validating TPS Synchronization
in the
MPEM REPLACEMENT section above.
Start engine and make sure it operates normally
through its full engine RPM range. If fault codes ap-
pear, refer to DI SYSTEM FAULT CODES in DIAG-
NOSTIC PROCEDURES section for more informa-
tion.
CRANKSHAFT POSITION
SENSOR (CPS)
1. Magneto cover
2. CPS connector
Check for RPM display at the information center
while cranking
engine (first ensure information
center is in tachometer mode). If it displays ap-
proximately 300 RPM, the CPS circuitry is properly
working.
Otherwise, validate the information center is
working by activating the tachometer using the
software B.U.D.S. under
Activation
(first ensure
information center is in tachometer mode). If it
does not display 3000 RPM, the information cen-
ter may be faulty and needs to be tested.
If the information center correctly displayed 3000
RPM, perform the following tests.
NOTE:
Take into account that a CPS fault can be
triggered by bent or missing encoder wheel teeth.
Check the teeth condition. Also, bad connections
in magneto connector could generate electrical
noise that would make you wrongly think the CPS
is faulty. Check terminals and wires.
Encoder Wheel Inspection
To check the encoder wheel for bent teeth, pro-
ceed as follows.
Remove magneto cover. Refer to MAGNETO SYS-
TEM in ENGINE section.
Install a dial indicator on crankcase. Position the
gauge on a tooth and set it to zero (0). Rotate fly-
wheel and check needle movement. The maxi-
mum allowed difference between teeth is 0.15
mm (.006 in). Otherwise, straighten the tooth or
replace the encoder wheel.
1. Encoder wheel
2. Dial indicator
Properly reinstall cover.
2
F12R0OA
1
F12R1HA
2
1
www.SeaDooManuals.net
Содержание 2003 GTI LE RFI
Страница 1: ...www SeaDooManuals net ...
Страница 767: ...NOTE www SeaDooManuals net ...
Страница 768: ...NOTE www SeaDooManuals net ...
Страница 769: ...F00Z0D 2003 GTI MODEL WARNING www SeaDooManuals net ...
Страница 770: ...F00Z0C 2003 GTI LE MODEL WARNING www SeaDooManuals net ...
Страница 771: ...F00Z0E 2003 GTI LE RFI MODEL WARNING www SeaDooManuals net ...
Страница 772: ...F00Z0J 2003 RX DI MODEL WARNING www SeaDooManuals net ...
Страница 773: ...F00Z0I 2003 GTX DI MODEL WARNING www SeaDooManuals net ...
Страница 774: ...F00Z0K 2003 XP DI MODEL WARNING www SeaDooManuals net ...
Страница 775: ...F00Z0F 2003 GTX 4 TEC MODEL WARNING www SeaDooManuals net ...
Страница 776: ...F00Z0G 2003 GTX 4 TEC MODEL WITH AUXILIARY DESS MODULE WARNING www SeaDooManuals net ...
Страница 777: ...F00Z0B 2003 GTX 4 TEC AND GTX 4 TEC SUPERCHARGED MODELS WARNING www SeaDooManuals net ...
Страница 779: ...www SeaDooManuals net ...