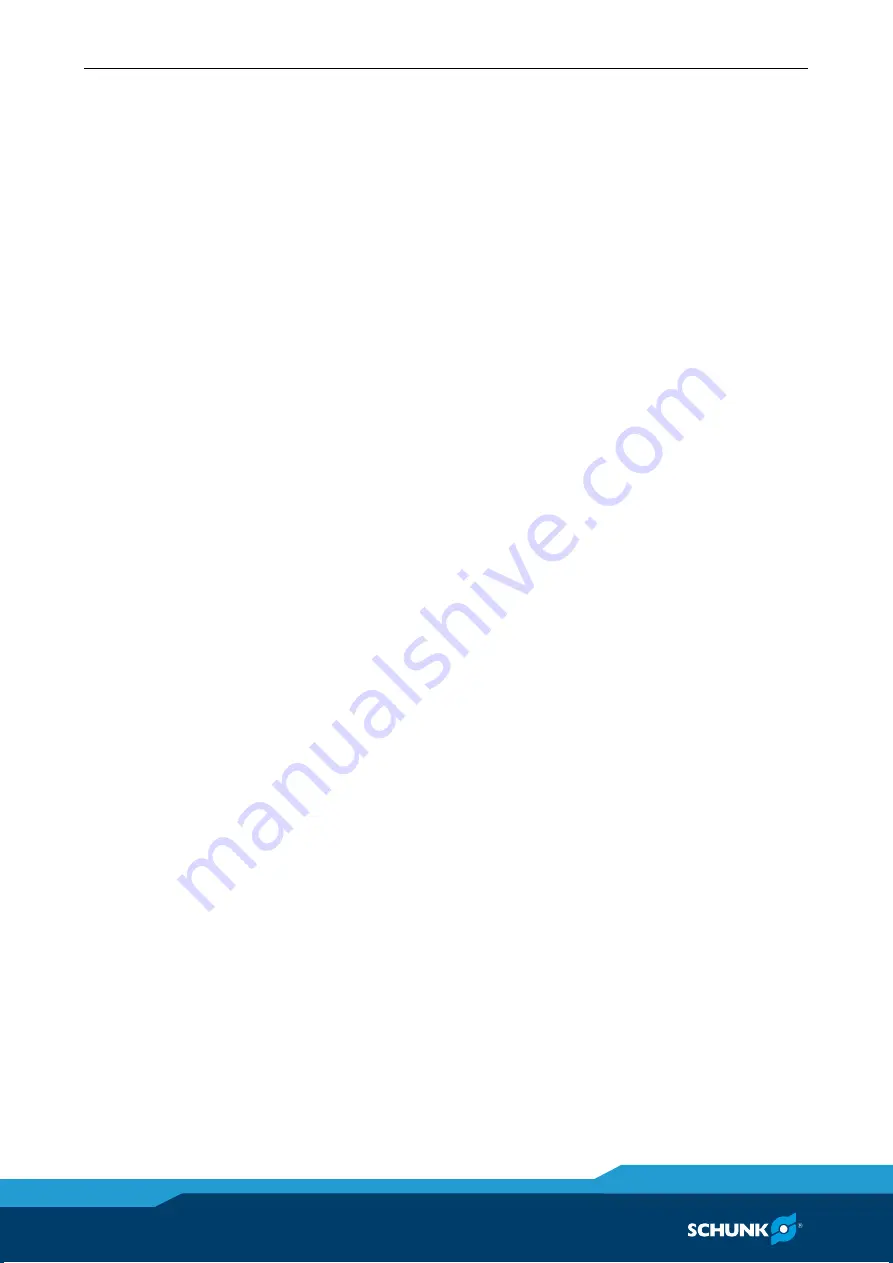
Operational Considerations
26
01.00|SWS-001 |en
Tool Locating Features
The Tool must be positively located in the Tool Stand. A variety of
methods may be used to accomplish this. Whatever method is
chosen, it is important that the required compliance or “float” be
built into the locating system.
Other Tool locating feature methods include balls and detents,
dowel pins in notched V-grooves, etc. Please consult SCHUNK for
recommendations or assistance with locating feature design for
your particular tooling.
Cylindrical (not tapered) dowel pins
should not
be used as they
provide too much surface engagement. During coupling and un-
coupling, the Tool can bind on these straight (cylindrical) pins due
to misalignment of the SWK and the SWA.
Robot programming and locational repeatability are important in
Tool pick-up and drop-off.
Tool Stands Sensors
It is suggested that the customer provide a sensor that detects the
presence of a properly seated Tool in the Tool Stand. The sensor
may be used prior to coupling to ensure there is a Tool properly
seated in the stand. Sensors may also be used as the robot starts
to move away after uncoupling. This provides a fail-safe measure
in the event that a Tool should become jammed in the stand or if
the Tool should fail to release properly from the robot.
Proximity sensors should be located so that the sensing face is ver-
tical to prevent swarf or other debris from falling on the sensor
and creating false readings.
7.3.1
7.3.2
Содержание SWS-001
Страница 35: ...Drawings 01 00 SWS 001 en 35 Drawings Tool Changer SWS 001 Tool Changer 11 11 1...
Страница 36: ...Drawings 36 01 00 SWS 001 en quick change head SWK 001...
Страница 37: ...Drawings 01 00 SWS 001 en 37 quick change adapter SWA 001...
Страница 38: ...Drawings 38 01 00 SWS 001 en E04 Electrical Module Electrical Module 11 2...
Страница 40: ...40 01 00 SWS 001 en...