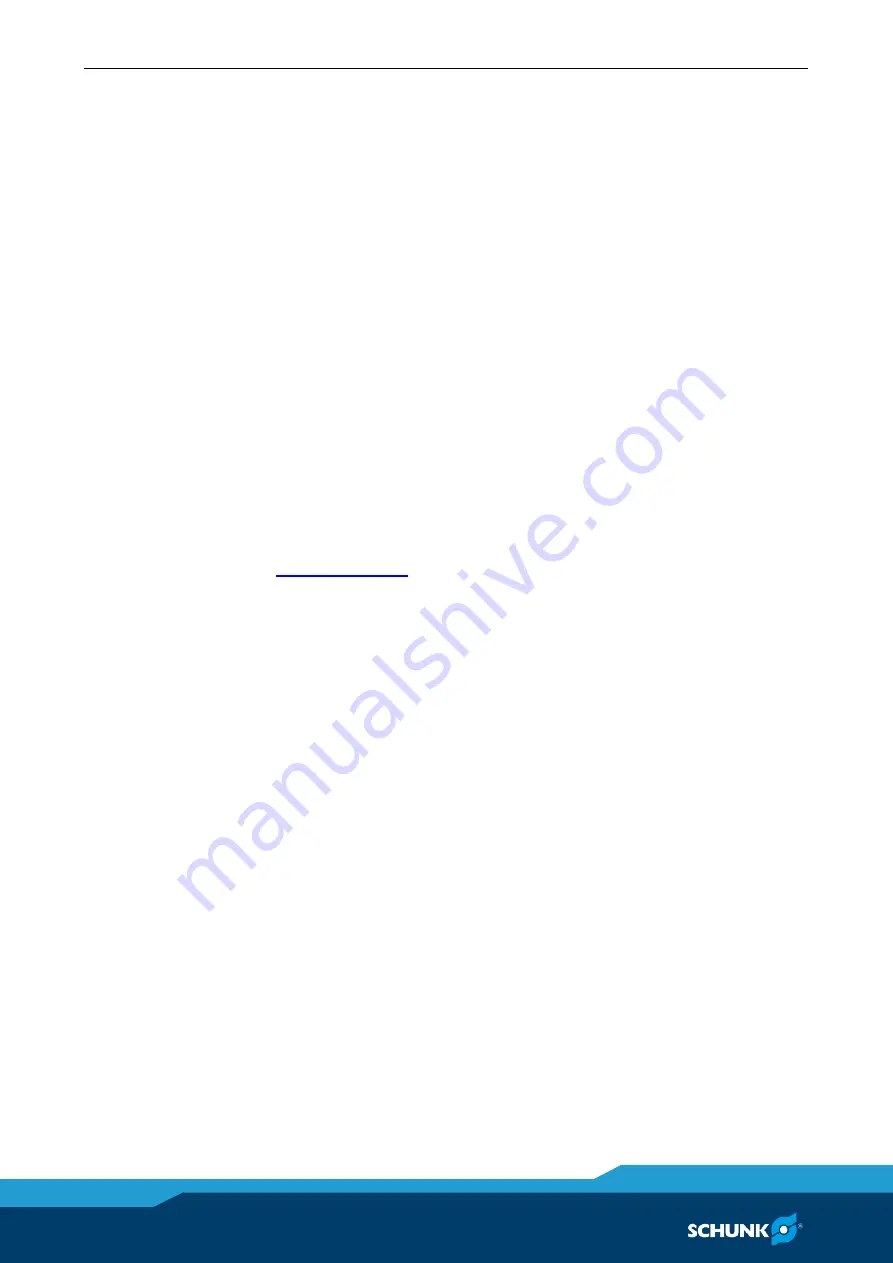
Function
34
02.00|ROTA NCR |en
Function
Function and handling
The lever chuck is actuated using a rotating solid or through-hole
cylinder. The axial tension and pressure forces are diverted into
the radial clamping force via lever action.
The clamping and opening path of the chuck jaws is determined by
the clamping cylinder. The serration of the base jaws can be used
to standard jaws as well as mount customized chuck jaws for
complicated workpiece shapes. The top jaws are moved or
changed in the open clamping position.
The 6-jaw compensation chuck has paired pendulum chuck jaws
that clamp concentrically. Two base jaws are always connected
with a compensation piece. The result is workpiece centering
between six points of contact, which are averaged in pairs. Even
raw parts can be centered without distortion of the workpiece.
For special applications, the pendulum compensation can be
disabled and all jaws simultaneously clamp concentrically.
Functional testing
Functional test
After installation of the chuck, its function must be checked prior
to start-up.
Two important points are:
•
Clamping Force!
The clamping force of the chuck must be
achieved at max. operating force/pressure.
•
Stroke control!
The stroke of the clamping piston must allow a
safety zone at the front and rear end position. The machine
spindle may only be started when the clamping piston has
passed through the safety zone. Only limit switches that meet
the requirements for safety limit switches specified in DIN EN
60204-1 may be used.
When determining the necessary clamping force to machine a
workpiece, take the centrifugal force acting on the chuck jaws into
account (according to VDI 3106).
If the chuck jaws are changed, adjust the stroke control to the new
situation.
6
6.1
6.2