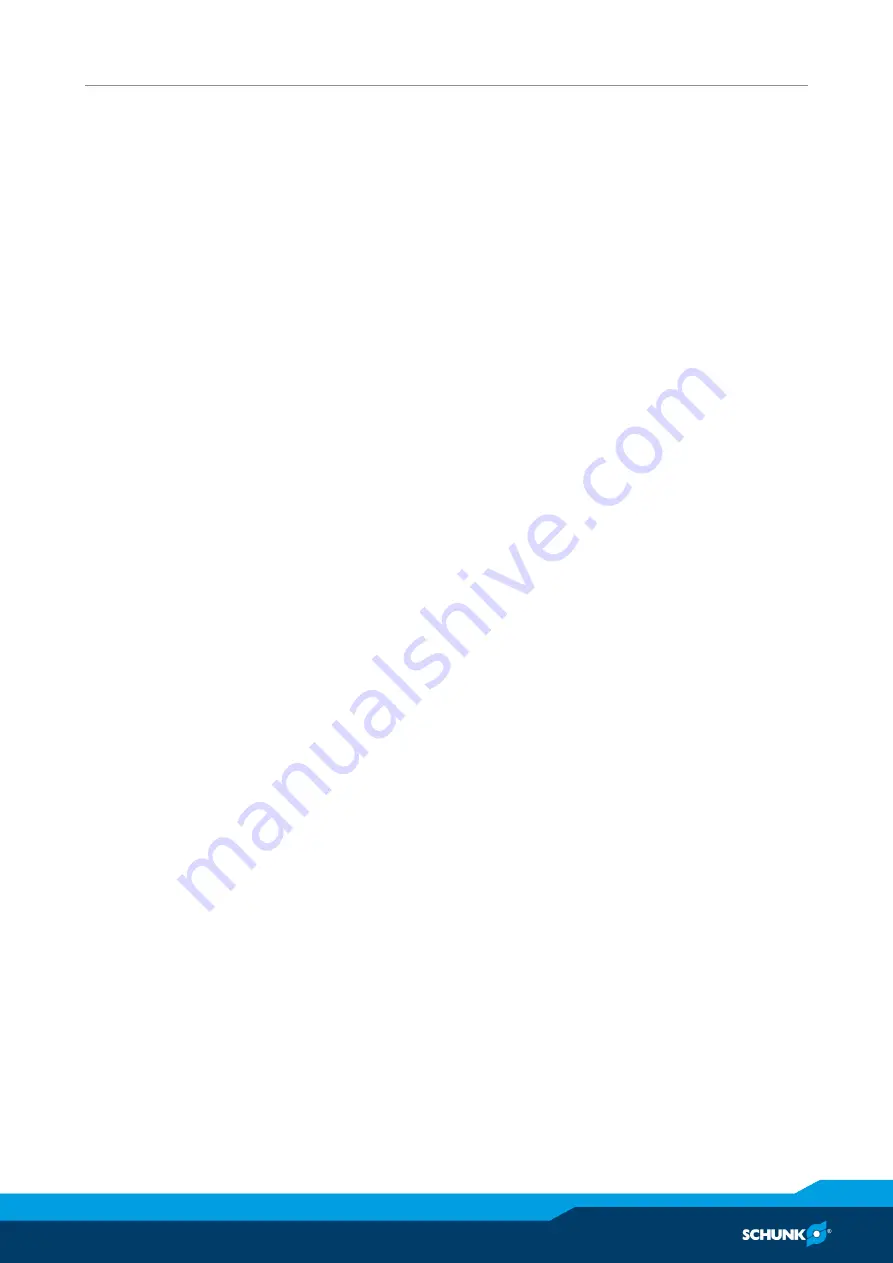
Basic safety notes
3.00 | PRH | Assembly and Operating Manual | en | 389327
19
2.12.5 Protection against magnetic and electromagnetic fields
Work in areas with magnetic and electromagnetic fields
Magnetic and electromagnetic fields can lead to serious injuries.
• Persons with pace-makers, metal implants, metal shards, or
hearing aids require the consent of a physician before entering
areas in which components of the electric drive and control
systems are mounted, started up, and operated.
• Persons with pace-makers, metal implants, metal shards, or
hearing aids require the consent of a physician before entering
areas in which magnetic grippers or motor parts with
permanent magnets are stored, repaired, or assembled.
• Do not operate high-frequency or radio devices in the proximity
of electric components of the drive system and their feed lines.
If the use of such devices is necessary:
When starting up the electric drive and control system, check
the machine or automated system for possible failures when
such systems are used at different intervals and in different
states of the control system. A special additional EMC test may
be necessary if the system has a high risk potential.