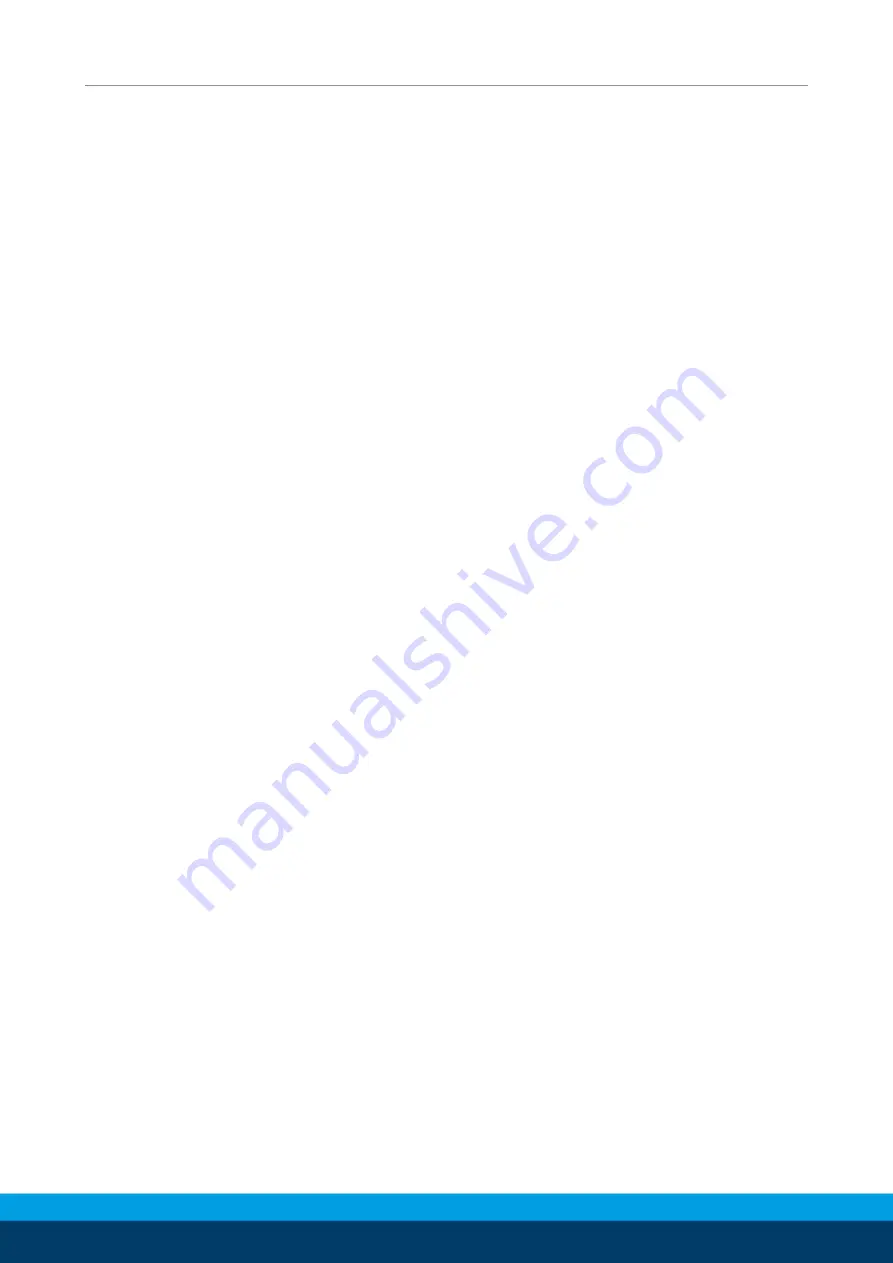
Function description and application examples
12
02.00 | FMS | Assembly and Operating Manual | en | 389074
4.2 Application example
Gripping force control
The PLC can output the automatically measured gripping force by
control signals to the proportional valve supplying the gripper.
In this way, fragile parts can be approached with a weak force until
the fingers rest against the part. Thereafter, the force is slowly
increased until it is sufficient for a secure grip.
Teaching of robots
The teaching of robots to grip firmly fixed workpieces can be done
easily and precisely.
Only when the left and right gripper jaws apply the same force
does the gripper grip symmetrically. Grippers and robots are
protected.
Static gripping force
control
• Monitoring the gripping force as the jaws close prevents the
workpiece from being dropped when movement initiates.
• Overload protection by monitoring the maximum permissible
force which can, for instance, be triggered by an unintended
increase in pressure, off-center gripping or incorrect positioning
of the workpiece.
• Preventive servicing by changing grippers in good time when
there is a decline in the gripping force. Unexpected
manufacturing down-times are avoided.
Dynamic gripping
force control
• The effect of acceleration forces on the gripper jaws can be
recorded and the motion sequence modified if necessary.
• Component monitoring during highly dynamic movements.
Measuring and
teaching processes
• Dimensional checking of the gripped component on the basis of
an inserted reference component.
• Comparing the component weight:
by measuring the weight force of the component acting on the
gripper fingers.