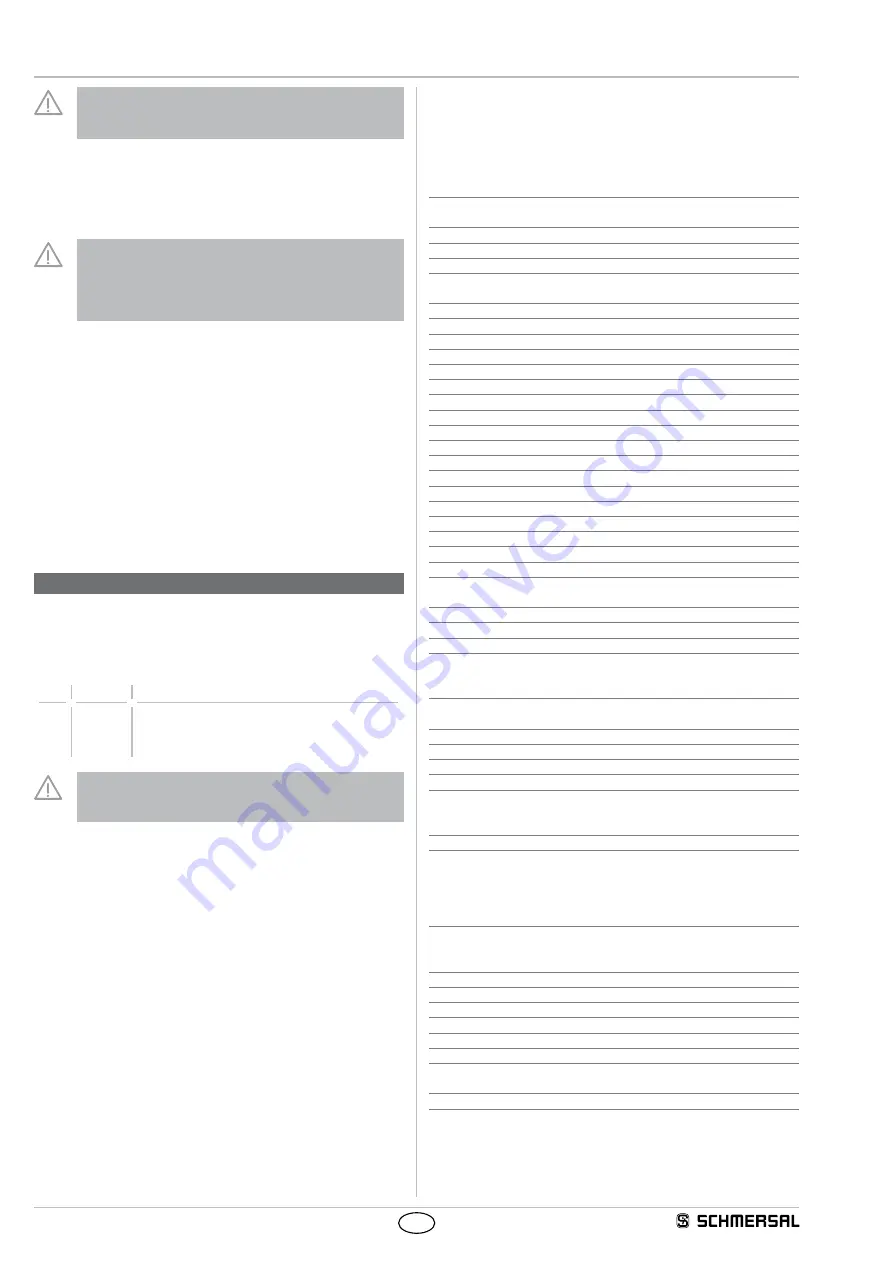
2
Operating instructions
Safety-monitoring module
SRB301STV.2 /CCV.2 /PCV.2
SRB301STV.3 /CCV.3 /PCV.3
EN
The entire concept of the control system, in which the
safety component is integrated, must be validated to
EN ISO 13849-2.
There are no residual risks, provided that the safety instructions as well
as the instructions regarding mounting, commissioning, operation and
maintenance are observed.
1.6 Warning about misuse
In case of inadequate or improper use or manipulations of the
safety-monitoring module, personal hazards or damage to
machinery or plant components cannot be excluded. The re-
levant requirements of the standards EN 81-1/-2, ISO 14119
and EN ISO 13850 must be observed.
1.7 Exclusion of liability
We shall accept no liability for damages and malfunctions resulting from
defective mounting or failure to comply with this operating instructions
manual. The manufacturer shall accept no liability for damages result-
ing from the use of unauthorised spare parts or accessories.
For safety reasons, invasive work on the device as well as arbitrary re-
pairs, conversions and modifications to the device are strictly forbidden;
the manufacturer shall accept no liability for damages resulting from
such invasive work, arbitrary repairs, conversions and/or modifications
to the device.
The safety-monitoring module must only be used when the enclosure is
closed, i.e. with the front cover fitted.
2. Product description
2.1 Ordering code
This operating instructions manual applies to the following types:
SRB301ST
➀
V.2
SRB301ST
➀
V.3
No.
Option
Description
➀
Plug-in screw terminals 0.25…2.5 mm²
/CC
Plug-in cage clamps 0.25 … 1.5 mm²
/PC
Screw terminals 0.25…2.5 mm²
Only if the information described in this operating instructions
manual are realised correctly, the safety function and therefo-
re the compliance with the Machinery Directive is maintained.
2.2 Special versions
For special versions, which are not listed in the order code below 2.1,
these specifications apply accordingly, provided that they correspond to
the standard version.
2.3 Destination and use
The safety-monitoring modules for integration in safety circuits are
designed for fitting in control cabinets. They are used for the safe
evaluation of the signals of positive break position switches or magnetic
safety sensors for safety functions on sliding, hinged and removable
safety guards as well as emergency stop control devices and AOPD's.
The safety function is defined as the opening of the enabling circuits
13-14, 23-24 and 33-34 when the inputs S11-S12 and/or S21-S22 are
opened. The safety-relevant current paths with the outputs contacts 13-
14, 23-24 and 33-34 meet the following requirements under observation
of a PFH value assessment (also refer to chapter 2.5 "Safety classifi-
cation"):
– Control category 4 – PL e to DIN EN ISO 13849-1
– corresponds to SIL 3 to DIN EN 61508-2
– SILCL 3 to DIN EN 62061
To determine the Performance Level (PL) of the entire safety function
(e.g. sensor, logic, actuator) to DIN EN ISO 13849-1, an analysis of all
relevant components is required.
In addition to that, the requirements of EN 81-1/-2 are met.
2.4 Technical data
General data
Standards:
IEC/EN 60204-1, EN 60947-5-1,
EN ISO 13849-1, IEC 61508, EN 81-1/-2
Climate resistance:
EN 60068-2-78
Mounting:
Snaps onto standard DIN rail to EN 60715
Terminal designations:
EN 60947-1
Material of the housings:
Plastic, glass-fibre reinforced
thermoplastic, ventilated
Material of the contacts:
AgSnO, self-cleaning, positive drive
Weight:
240 g
Start conditions:
Automatic or start button (monitored)
Feedback circuit (Y/N):
yes
Pull-in delay for automatic start:
typ. 100 ms
Pull-in delay with reset button:
typ. 15 ms
Drop-out delay in case of emergency stop:
typ. 25 ms / max. 32 ms
Drop-out delay on "supply failure":
typ. 100 ms
Bridging in case of voltage drops:
typ. 80 ms
Mechanical data
Connection type:
refer to 2.1 Ordering code
Cable section:
refer to 2.1 Ordering code
Connecting cable:
rigid or flexible
Tightening torque for the terminals:
0.6 Nm
With removable terminals (Y/N):
refer to 2.1 Ordering code
Mechanical life:
10 million operations
Electrical life:
Derating curve available on request
Resistance to shock:
10 g / 11 ms
Resistance to vibrations to EN 60068-2-6:
10 … 55 Hz,
amplitude 0.35 mm
Ambient conditions
Ambient temperature:
– 25 °C … +60 °C
Storage and transport temperature:
– 40 °C … +85 °C
Protection class:
Enclosure: IP40
Terminals: IP20
Clearance: IP54
Air clearances and creepage
distances to IEC/EN 60664-1:
4 kV/2 (basic insulation)
EMC rating:
to EMC Directive
Electrical data
Contact resistance in new state:
max. 100 mΩ
Power consumption:
max. 2,0 W / 4,9 VA
Rated operating voltage U
e
:
24 VDC –15% / +20%,
residual ripple max. 10%,
24 VAC –15% / +10%
Frequency range:
50 / 60 Hz
Fuse rating for the operating voltage:
Internal electronic trip,
tripping current > 500 mA,
Internal electronic trip, tripping
current > 50 mA (S11, S21),
Reset after disconnection of supply voltage
Current and voltage at:
S11-S12, S21-S22: 24 VDC / 10 mA
X2: 24 VDC, start impulse 2.5 mA / 25 ms
X3: 24 VDC, start impulse 35 mA / 25 ms
Monitored inputs
Cross-wire detection (Y/N):
Yes
Wire breakage detection (Y/N):
Yes
Earth leakage detection (Y/N):
Yes
Number of NO contacts:
0
Number of NC contacts:
2
Cable length:
1,500 m mit 1.5 mm²
2,500 m mit 2.5 mm²
Conduction resistance:
max. 40 Ω