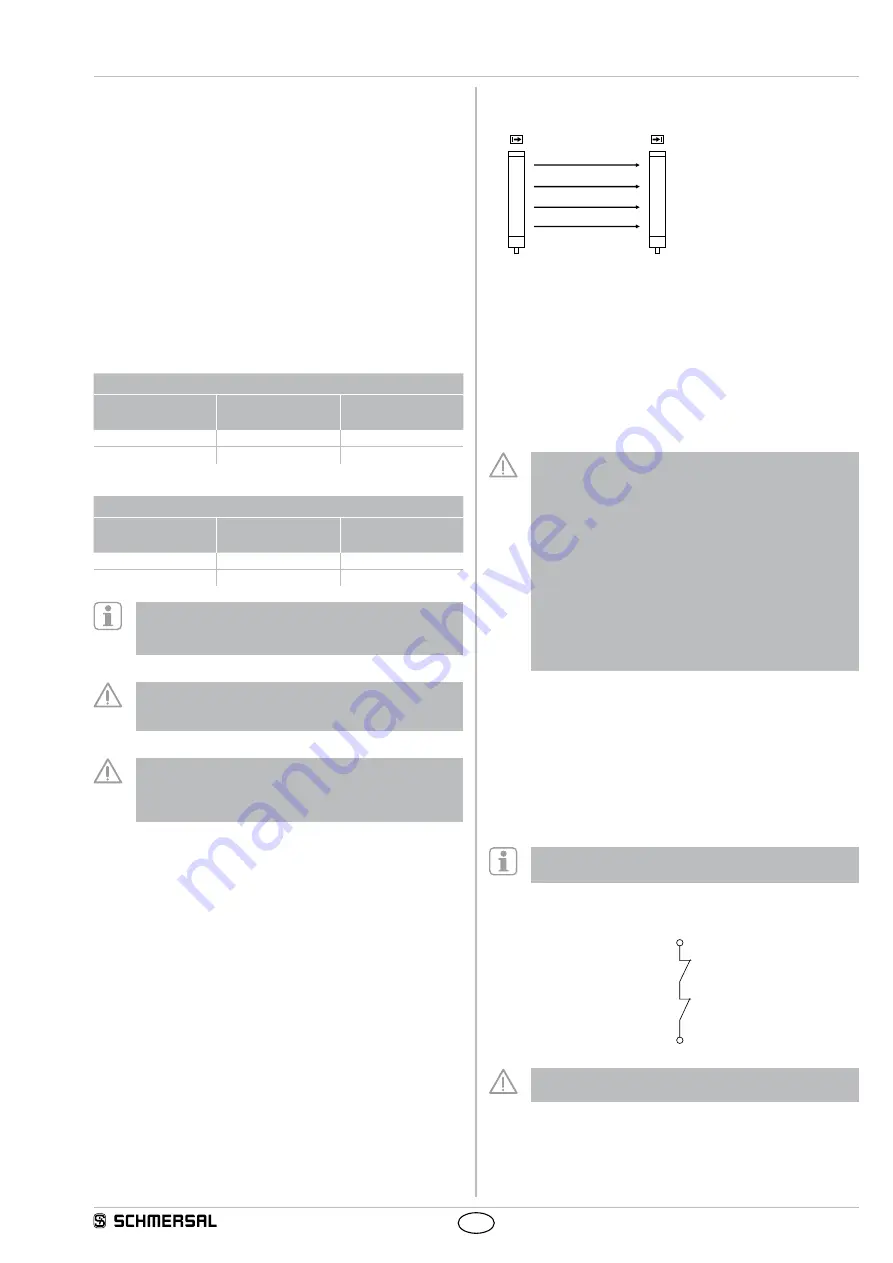
7
SLC440 Series
SLG440 Series
Operating instructions
Safety light curtain / safety light grid
EN
With this extension of the object detection the resolution is increased
Therefore the physical resolution is changed to an effective resolution
This effective resolution must be used to calculate the safety distance
Use formula (1) in the chapter "Safety distance" to calculate the safety
distance with the effective resolution if a maximum of 2 light beams are
blanked
The number of light beams to be blanked is limited, see table "Effective
resolution"
A system with a physical resolution of 14 mm will have an increased
effective resolution of 34 mm in case of floating blanking of two beams
The effective resolution must be permanently and clearly visible
labelled at the receiver
Effective resolution
The effective resolution in case of activated blanking can be found in
the following table
Resolution 14 mm
Blanked
beams
Physical
resolution
Effective resolution
1
14
24
2
14
34
Resolution 30 mm
Blanked
beams
Physical
resolution
Effective resolution
1
30
48
2
30
68
The function is activated in parameter setting mode (P 3) If
the function is activated, the LED blanking in the diagnostic
window of the receiver starts flashing
Perform a new calculation of the safety distance with the
effective resolution Adjust the safety distance in accordance
with your calculation
The standard IEC/TS 62046 includes information, which
describe possibly required additional measures to prevent a
person from reaching a hazard through the blanking areas of
a protection field
2.9.7 Blanking of moving objects (SLG440)
The SLG440 can blank movable objects in the protection field
4
3
2
1
R1
E1
The floating blanking range is authorised for individual beams in case of
obstacles, taking the protective function into account
The function enables an arbitrary floating blanking of partial areas in the
protection field The first beam, which is located immediately behind
the diagnostic window, cannot be blanked
This function allows for an interruption of maximum 1 light beam
without the outputs being disabled in case of material movement in the
protection field, eg ejection of material or process-controlled material
movement
The operating mode is only available, when the parameter setting P 3 is
activated See chapter Parameter setting
• The variable blanking of one beam is not authorised with the
2-beam SLG440!
• The blanking of one beam at the most in the SLG440
3-beam version or the SLG440 4-beam version is
authorised, provided that the protective function is taken into
account
• The restart interlock (manual reset) function of the safety
light grid or the machine must be activated
• The protection field must be checked by a qualified person
after the configuration
• The standard IEC 62046 includes information, which
describe possible required additional measures to prevent a
person from reaching a hazard through the beam blanking
of a protection field
2.9.8 Contactor control (EDM)
The contactor control monitors the controlled switching elements
(auxiliary contacts of the contactors) of both outputs This monitoring
is realised after each interruption of the protection field and prior
to the restart (enabling) of the outputs In this way, malfunctions of
the contactors are detected, eg contact welding or contact spring
breakage If the light curtain detects a malfunction of the switching
elements, the outputs are locked
After elimination of the error, a power reset is required
The contactor control is not activated upon delivery The
function is activated in parameter setting mode (P 4)
Connection EDM
Wiring of the receiver
- Kn1, Kn2 = auxiliary contact of
the last switching relay
+24VDC
Kn1
Pin 8
Kn2
The auxiliary contacts must only be connected, when the
function is activated!