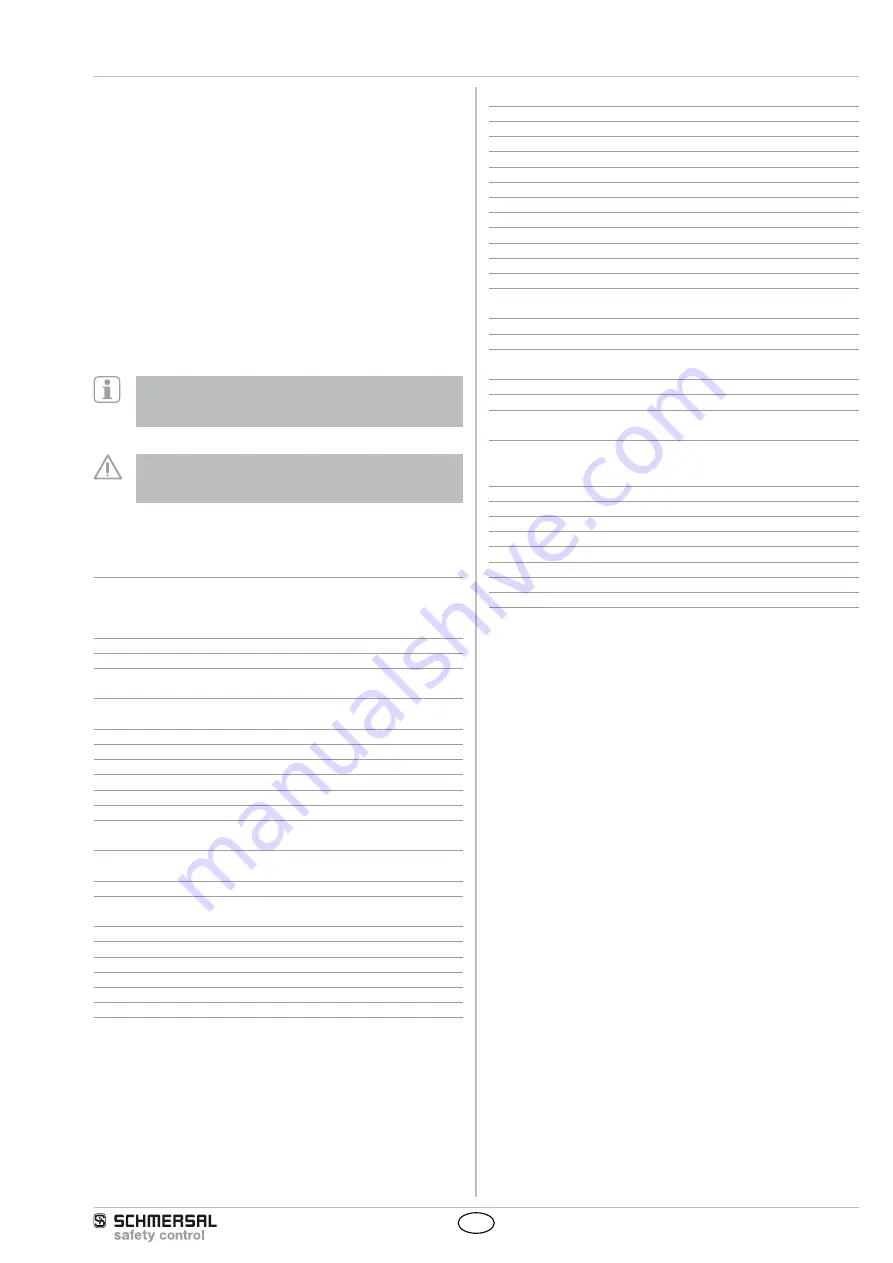
3
EN
SLC 420 IP 69 K
Operating instructions
Safety light curtain
MSD4 Vibration damper
Kit consisting of: 8 vibration dampers 15 x 20 mm, 8 M5 cylinder head
screws with hexagon socket, 8 spring washers
The MSD4 vibration damper kit must be used for damping vibrations
and oscillations on the safety light curtain SLC 420 For applications
with higher mechanical stresses, eg presses, punching machines, we
recommend the MSD4 kit In this way, the availability of the safety light
curtain SLC 420 is increased
2.4 Destination and use
The SLC 420 is a non-contact, self-testing safety guard, which is used
for the protection of hazardous points, hazardous areas and machine
accesses If one or more light beams are interrupted, the hazardous
movement must be stopped
The protective enclosure with IP 69K protection class is suitable for
applications, which need to be cleaned permanently (default cleaning
procedure) A Goretex compensating membrane prevents fogging and
the penetration of liquids during high temperature fluctuations
If liquids with aggressive ingredients are used for cleaning,
please check whether the product used is compatible with the
material of the sensor (refer to chapter "Technical data")
The user must evaluate and design the safety chain in ac-
cordance with the relevant standards and the required safety
level
2.5 Technical data
Standards:
EN 61496-1; CLC/TS 61496-2;
EN ISO 13849; EN 62061
Material of the enclosure:
Aluminium
Protective tube:
PMMA Plastic tubes
End plugs:
PA 6
Membran:
PA 6, Gore Tex Membran M12 x 15
Number of beams:
2 … 144 Beams
Protection field heights
Resolution 14 mm:
170 mm … 1450 mm,
(170, 250, 330, 410, 490)
Resolution 30 mm:
170 mm … 1450 mm,
(170, 250, 330, 410, 490)
Detection sensitivity for test bodies:
14 mm, 30mm
Range of the protection field:
03 … 70 m; (Resolution 14 mm)
0,3 … 10,0 m; (resolution 30 mm)
Response time:
1 … 48 L = 10 ms, 49 … 144 L = 20 ms without beam coding A
1 … 48 L = 15 ms, 49 … 144 L = 27 ms with beam coding A
Rated operating voltage:
24 VDC ±10% (PELV) supply unit to EN
60204 (power drop > 20 ms)
Operating current:
400 mA max + 05 A (OSSD load + output signal
quality load)
Wave length of the sensor:
880 nm
Safety outputs (OSSD1, OSSD2):
2 x PNP-type semi-conductor,
short-circuit proof
Switching voltage HIGH¹:
15 … 28,8 V
Switching voltage LOW¹:
0 … 2 V
Switching current:
0 … 500 mA
Leakage current²:
1 mA
Load capacity:
2 µF
Load inductance:
2 H
Admissible conduction resistance
between OSSD and load:
2,5 Ω
Supply cable:
1 Ω
Contactor control (EDM)
Input voltage HIGH (inactive):
17 … 29 V
Input voltage LOW (active):
0 … 25 V
Input current HIGH:
3 … 10 mA
Input current LOW:
0 … 2 mA
Input restart interlock (manual reset)
Input voltage HIGH (active):
17 … 29 V
Input voltage LOW (inactive):
0 … 25 V
Input current HIGH:
3 … 10 mA
Input current LOW:
0 … 3 mA
Function:
Protective mode, start and restart interlock (manual reset),
contactor control, beam blanking fixed and floating
Signal times
Contactor control:
50 … 500 ms, einstellbar
Restart interlock (manual reset):
50 ms … 1,0 s, signal trans-
mission in case of trailing edge
Start interlock:
250 … 1500 ms, adjustable
LED indications transmitter:
Transmitting, status
LED indications receiver:
OSSD ON, OSSD OFF, restart, signal
reception, blanking, multifunction
Connection:
screwed cable gland M16 x 15
cable connector M12 x 1; 4-pole fixed to transmitter,
M12 x 1; 8-pole fixed to receiver integrated
Ambient temperature:
−10° C … +50° C
Storage temperature:
−25° C … +70° C
Interface:
Diagnostics and function setting
Protection class:
IP 69K
Resistance to vibrations:
10 … 55 Hz to IEC 60068-2-6
Resistance to shock:
10 g; 16 ms; to IEC 60068-2-29
Year of construction:
as of 2010 version 10
¹) To IEC 61131-2
²) In case of failure, the leakage current at the most flows to the OSSD
cable The downstream control element must recognise this state as
LOW A safety PLC must detect this state