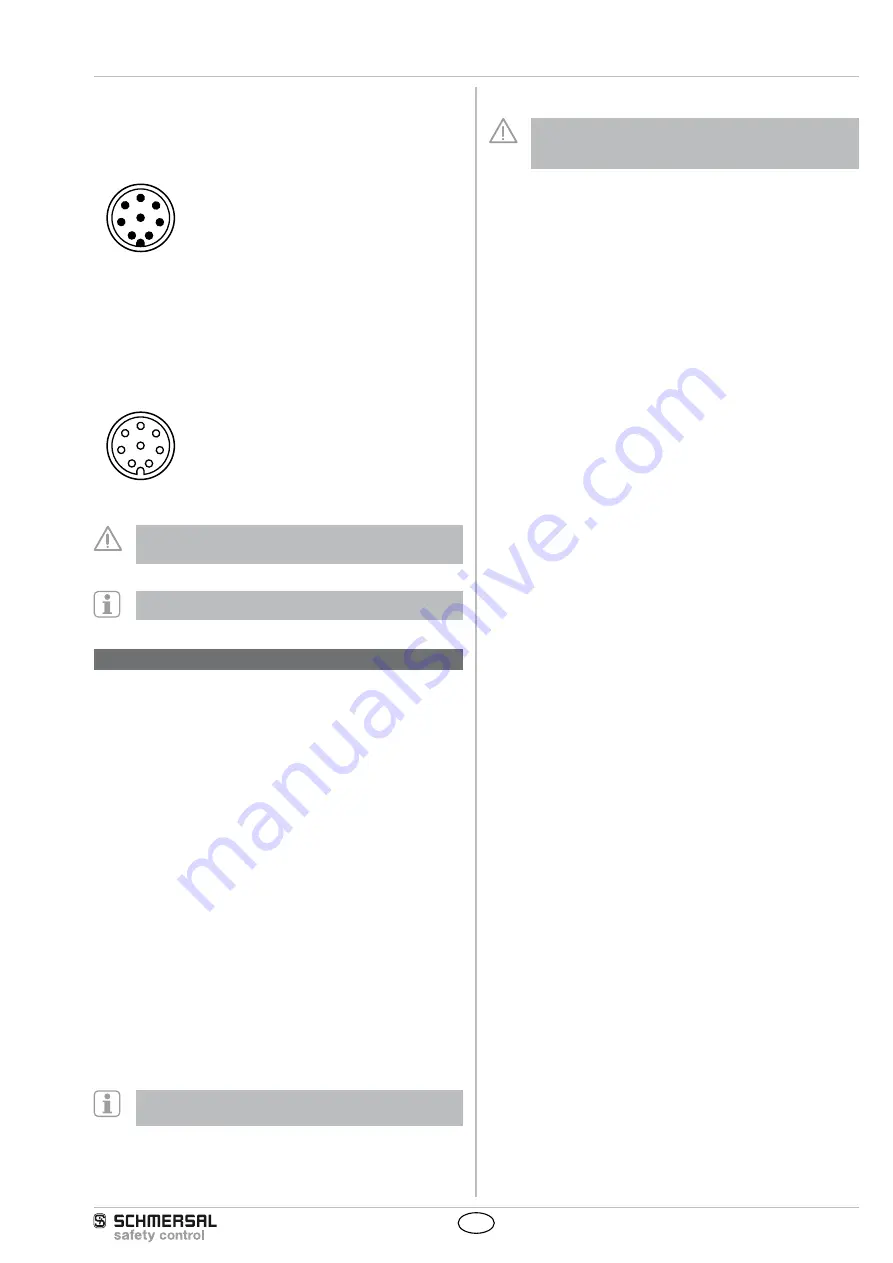
11
SLC 220
SLG 220
Operating instructions
Safety light curtain / safety light grid
EN
Connector configuration Receiver, Transmitter & Cable
SLC: Connector male
M12 / 8 pol.
Signal
Receiver
Transmitter
5
8
4
3
2
1
7
6
1 WH Signal quality
Restart interlock
(manual reset)
2 BN +24 VDC
+24 VDC
3 GN OSSD 1
Contactor control
4 YE OSSD 2
Test input
5 GY RS485 (B)
RS485 (B)
6 PK RS485 (A)
RS485 (A)
7 BU 0 VDC
0 VDC
8 RD not used /
reserved
not used / reserved
Cable: Connector female
M12 / 8 pole
5
8
4
3
2
1
7
6
The colour codes are only valid for the cable types mentioned
below "optional accessories".
Master/slave systems have the same connector configuration!
5. Set-up and maintenance
5.1 Check before start-up
Prior to start-up, the following items must be checked by the responsi-
ble person.
Wiring check prior to start-up
1. The voltage supply is a 24V direct current power supply, which meets
the CE Directives, Low Voltage Directives. A power downtime of 20 ms
must be bridged.
2. Presence of a voltage supply with correct polarity at the SLC/SLG.
3. The connecting cable of the transmitter is correctly connected to the
transmitter and the connecting cable of the receiver correctly to the
receiver.
4. The double insulation between the light curtain output and an exter-
nal potential is guaranteed.
5. The outputs OSSD1 and OSSD2 are not connected to +24 VDC.
6. The connected switching elements (load) are not connected to 24
VDC.
7. If two or more SLC/SLG are used within close range compared to
each other, an alternating arrangement must be observed. Any mu-
tual interference of the systems must be prevented.
Switch the SLC/SLG on and check the operation in the following way
The component performs a system test during approx. 2 seconds after
the operating voltage has been switched on. After that, the outputs are
enabled (if the protection field is not interrupted). The LED "OSSD ON"
of the receiver is on.
In case of incorrect functioning, please follow the instructions
listed in the chapter Fault diagnostic.
5.2 Maintenance
Do not use the SLC/SLG before the next inspection is termi-
nated. An incorrect inspection can lead to serious and mortal
injuries.
Conditions
For safety reasons, all inspection results must be archived. The operat-
ing principle of the SLC/SLG and the machine must be known in order
to be able conducting an inspection. If the fitter, the planning technician
and the operator are different persons, please make sure that the user
has the necessary information at his disposal to be able conducting the
maintenance.
5.3 Regular check
A regular visual inspection and functional test, including the following
steps, is recommended:
1. The component does not have any visible damages.
2. The optics cover is not scratched or soiled.
3. Hazardous machinery parts can only be accessed by passing
through the protection field of the SLC/SLG.
4. The staff remains within the detection area, when works are con-
ducted on hazardous machinery parts.
5. The safety distance of the application exceed the mathematically
calculated one.
Operate the machine and check whether the hazardous movement
stops under the hereafter-mentioned circumstances.
6. Hazardous machine parts do not move when the protection field is
interrupted.
7. The hazardous machine movement is immediately stopped, when
the protection field is interrupted with the test rod immediately before
the transmitter, immediately before the receiver and in the middle
between the transmitter and the receiver.
8. No hazardous machine movement when the test rod is within the
protection field.
9. The hazardous machine movement comes to standstill, when the
voltage supply of the SLC/SLG is switched off.
5.4 Half-yearly inspection
The following items must be checked every six months or when a ma-
chine setting is changed.
1. Machine stops or does not inhibit any safety function.
2. No machine modification or connection change, which affects the
safety system, has taken place.
3. The outputs of the SLC/SLG are correctly connected to the machine.
4. The total response time of the machine does not exceed the re-
sponse time calculated during the first putting into operation.
5. The cables, the connectors, the caps and the mounting angles are in
perfect condition.
5.5 Cleaning
If the optics cover of the sensors is extremely soiled, the OSSD outputs
can be disabled. Clean with a soft cloth without exercising pressure.
The use of agressive, abrasive or scratching cleaning agents, which
could attack the surface, is prohibited.