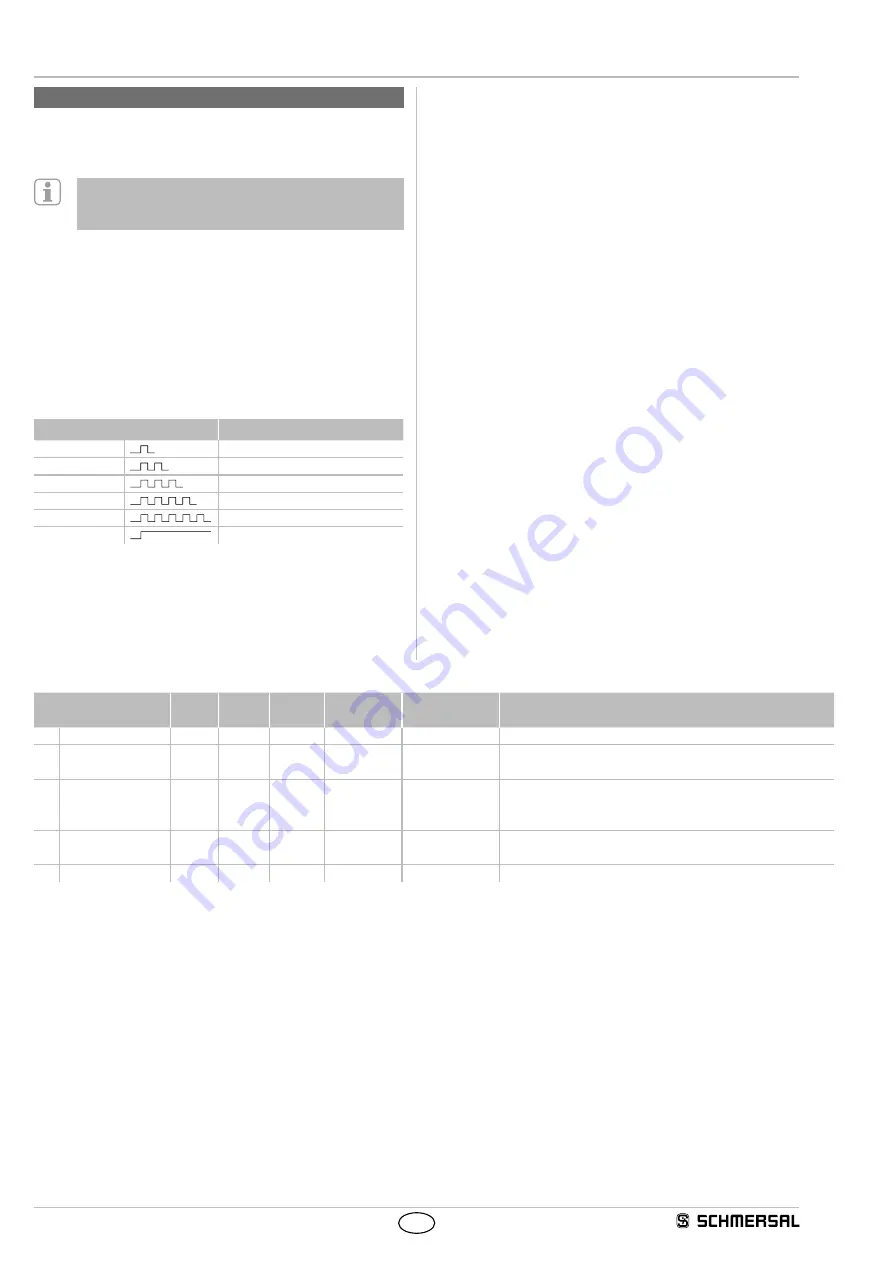
6
Operating instructions
Safety sensor
CSS 34
EN
5. Diagnostic functions
5.1 Operating principle of the diagnostic LEDs
The safety sensor indicates the operating condition and faults by means
of three-colour LEDs located in the lateral surfaces of the sensor.
The following LED indicators are the same for safety sensors
with conventional diagnostic output as for those with a serial
diagnostic function.
The green LED indicates that the safety sensor is ready for operation.
The sensor is not actuated.
The yellow LED indicates the switching condition of the safety outputs.
The flashing can be used to prematurely detect variations in the
clearance between the sensor and the actuator (e.g. sagging of a safety
guard). The sensor must be adjusted before the distance to the actuator
increases and before the safety outputs are disabled, thus stopping the
machine. If an error is detected, the red LED will be activated.
Flash codes red diagnostic LED
LED indication (red)
Error cause
1 flash pulse
Error output Y1
2 flash pulses
Error output Y2
3 flash pulses
Cross-wire Y1/Y2
4 flash pulses
ambient temperature too high
5 flash pulses
Wrong or defective actuator
Continuous red
Internal error
5.2 Operating principle of the electronic diagnostic output
Table 1: Examples of the diagnostic function of the safety-sensor with conventional diagnostic output
Sensor function
LED
green red
yellow
Diagnostic
output
Safety outputs
Y1, Y2
Note
I.
Supply voltage
On
Off
Off
0 V
0 V
Voltage on, no evaluation of the voltage quality
II. actuated
On
Off
On
24 V
24 V
The yellow LED always signals the presence of an actuator
within range
III. Actuated, actuator
in limit area
On
Off
Flashes
(1Hz)
24 V pulsed
24 V
The sensor must be adjusted before the distance to the
actuator increases and before the safety outputs are disabled,
thus stopping the machine
IV. Error warning,
sensor actuated
On
Flashes
On
0 V
24 V
After 30 minutes if the error is not rectified
V. Error
On
Flashes
On
0 V
0 V
Refer to table with flash codes
The short-circuit proof diagnostic output can be used for central
visualisation or control functions, e.g. in a PLC.
The electronic diagnostic output signals faults before the safety outputs
are disabled, thus enabling a controlled shutdown.
The diagnostic output is not a safety-relevant output!
The closed condition of the safety guard, i.e. the sensor is actuated,
is indicated through a positive signal. If the sensor is operating near
the limit of its switching distance, e.g. due to the sagging of the safety
guard, the sensor will emit a 1 Hz cyclic signal before the safety outputs
are disabled.
The diagnostic output can also be used to detect clearance variations
between the sensor and the actuator in the same way as the yellow
LED.
An active fault causes the diagnostic output to be disabled. The safety
outputs are disabled after max. 30 minutes if the fault is not rectified.
The signal combination, diagnostic output disabled and safety channels
still enabled, can be used to stop the production process in a controlled
manner.
Error
Any error that does not immediately affect the functionality of the safety
sensor (e.g. the ambient temperature being too high, interference
potential at a safety output, cross-wire short) will lead to a delayed
shut-down.
After fault rectification, the error message is reset by opening and re-
closing the corresponding safety guard. The safety outputs enable and
allow a restart.
Error warning
The safety outputs are disabled after 30 minutes if the error is not
rectified. The signal combination, diagnostic output disabled and
safety channels still enabled, can be used to stop the production
process in a controlled manner.