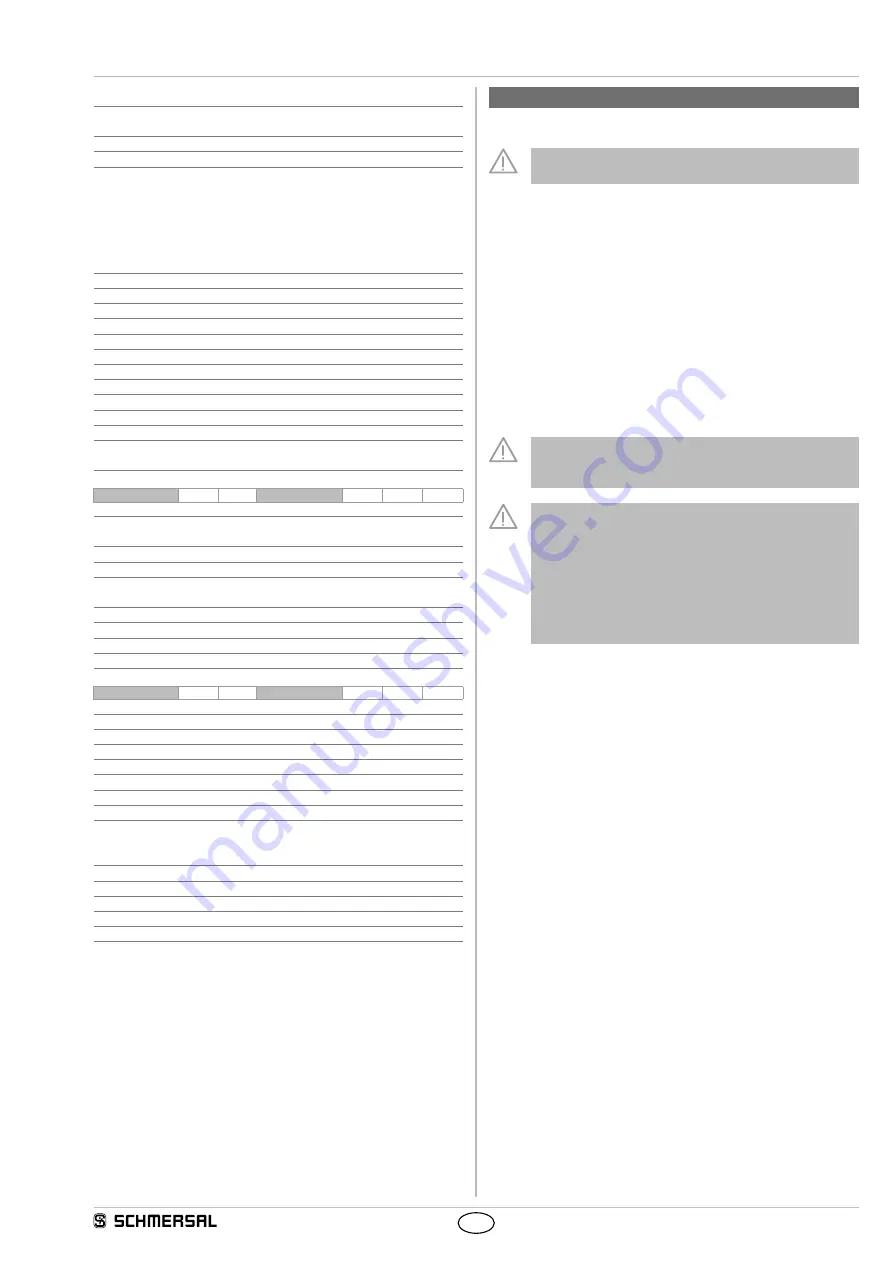
3
CSS 34
Operating instructions
Safety sensor
EN
Electrical data:
Rated operating voltage U
e
:
24 VDC −15% / +10%
(stabilised PELV to IEC 60204-1)
Rated operating current I
e
:
0.6 A
Required rated short-circuit current:
100 A
Fuse (line protection):
note the wire
diameter of continuing wire:
- for wire variants:
up to 45 °C ambient temperature: 4.0 A
up to 60 °C ambient temperature: 3,15 A
up to 65 °C ambient temperature: 2,5 A
up to 70 °C ambient temperature: 2,0 A
- for plug version:
2.0 A
Rated insulation voltage U
i
:
32 VDC
Rated impulse withstand voltage U
imp
:
800 V
No-load current I
o
:
0.1 A
Response time:
< 30 ms
Duration of risk:
< 60 ms
Protection class:
II
Overvoltage category:
III
Degree of pollution:
3
EMC rating:
according to IEC 60947-5-3
Electromagnetic interference:
according to IEC 60947-5-3
Safety inputs X1/X2:
Accepted test pulse duration on input signal:
≤ 1.0 ms
- With test pulse interval of:
≥ 100 ms
Classification:
ZVEI CB24I
Sink:
C1
Source:
C1
C2
C3
Safety outputs Y1/Y2:
normally open function, 2 channel,
p-type, short-circuit proof
Rated operating voltage U
e
1:
max. 1 V under U
e
Leakage current I
r
:
< 0.5 mA
Rated operating current I
e1
:
max. 0.25 A, dependent
on ambient temperature
Utilisation category:
DC-12, DC-13
Rated operating voltage/current U
e1
/I
e1
:
24 VDC / 0.25 A
Test pulse duration:
≤ 1.0 ms
Test pulse interval:
1,000 ms
Classification:
ZVEI CB24I
Source:
C1
Sink:
C1
Diagnostic output:
short-circuit proof, p-type
Voltage drop:
< 5 V
Rated operating voltage U
e2
:
min. (U
e
– 5 V)
Operating current I
e2
:
max. 0,05 A
Utilisation category:
DC-12, DC-13
Rated operating voltage/current U
e2
/I
e2
:
24 VDC / 0.05 A
Wiring capacitance for serial diagnostics:
max. 50 nF
2.6 Safety classification
Standards:
ISO 13849-1, IEC 61508, IEC 62061
PL:
e
Control Category:
4
PFH value:
3.6 x 10
-9
/ h
SIL:
suitable for SIL 3 applications
Mission time:
20 years
3. Mounting
3.1 General mounting instructions
Please observe the relevant requirements of the standards
ISO 12100, ISO 14119 and ISO 14120.
The component can be mounted in any position. The active surface
of the safety sensor and the actuator has to be opposite. The sensor
enclosure must not be used as an end stop. The active surface of the
safety sensor is either the lateral surface marked with the type plate or
the front, rounded surface. The safety sensor must only be used within
the assured switching distances ≤ s
ao
and ≥ s
ar
.
The safety sensor and the CST 34-.-1 or CST 34-S-2 actuators are
supplied with integrated mounting plate. With the slotted holes of the
mounting plates, possible tolerances can be horizontally and vertically
compensated. The components are fitted with M4 screws.
The safety sensors and the actuators can be clipped onto the mounting
plate with different actuating directions. Both components are fixed by
means of a locking cap.
The actuator must be permanently fitted to the safety guards
and protected against displacement by suitable measures
(tamperproof screws, gluing, drilling of the screw heads).
The mounting plates must be pinned after their fixation.
The mounting brackets also must be secured by means of
the supplied locking pin to protect them against tampering.
The CST-S-3 and CST 180 actuators must be protected by
tamper-proof screws or a tamper-proof fitting.
At an ambient temperature of over 55°C, the safety sensor
must be fitted so that it is protected against unintentional
contact with persons.
To avoid any interference inherent to this kind of system and any
reduction of the switching distances, please observe the following
guidelines:
Minimum distance between two sensors: 100 mm