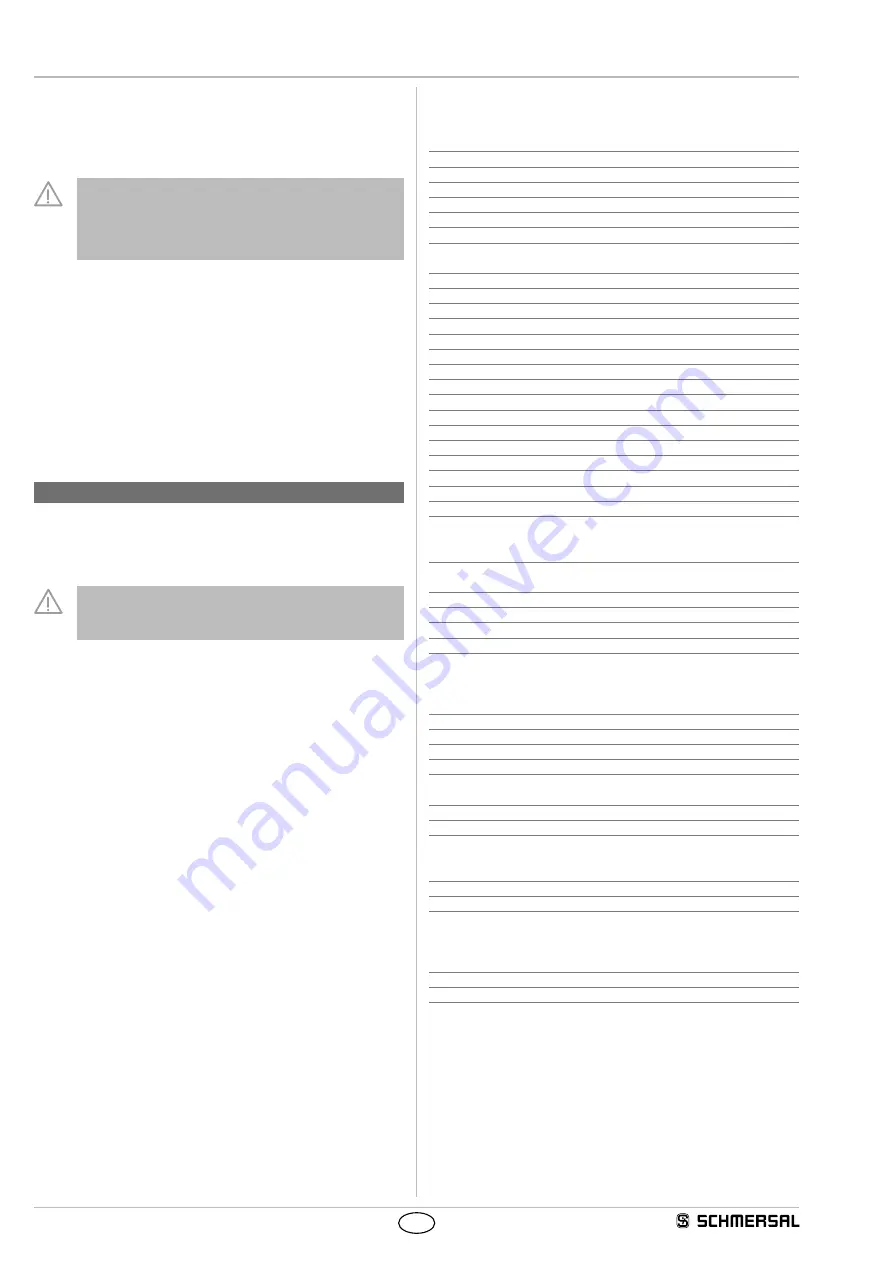
2
Operating instructions
Safety-monitoring module
AES 3075
EN
There are no residual risks, provided that the safety instructions as well
as the instructions regarding mounting, commissioning, operation and
maintenance are observed.
1.6 Warning about misuse
In case of inadequate or improper use or manipulations of
the safety-monitoring module, personal hazards or damages
to machinery or plant components cannot be excluded. The
relevant requirements of the standard EN 1088 must be
observed.
1.7 Exclusion of liability
We shall accept no liability for damages and malfunctions resulting from
defective mounting or failure to comply with this operating instructions
manual. The manufacturer shall accept no liability for damages
resulting from the use of unauthorised spare parts or accessories.
For safety reasons, invasive work on the device as well as arbitrary
repairs, conversions and modifications to the device are strictly
forbidden; the manufacturer shall accept no liability for damages
resulting from such invasive work, arbitrary repairs, conversions and/or
modifications to the device.
2. Product description
2.1 Ordering code
This operating instructions manual applies to the following types:
AES 3075
Only if the information described in this operating instructions
manual are realised correctly, the safety function and therefore
the compliance with the Machinery Directive is maintained.
2.2 Special versions
For special versions, which are not listed in the order code below 2.1,
these specifications apply accordingly, provided that they correspond to
the standard version.
2.3 Purpose
The safety-monitoring module for integration in safety circuits is
designed for fitting in control cabinets. It is used for the safe evaluation
of the signals of magnetic safety sensors on sliding, hinged and
removable safety guards. In conjunction with two positive-guided
external contactors, a protection of up to four safety guards can be set
up.
Design
The safety-monitoring module has a redundant structure. Two
microprocessors build the heart of the safety-monitoring module. The
enabling outputs for connecting the external positive-guided contactors
as well as all inputs of the safety-monitoring module are monitored
and evaluated by both microprocessors. The five additional transistor
outputs are short-circuit proof and can be used for signalling purposes.
2.4 Technical data
Standards:
IEC / EN 60204-1; EN 60947-5-3;
EN ISO 13849-1; IEC 61508;
BG-GS-ET-14; BG-GS-ET-20
Start conditions:
Automatic or start button
Feedback circuit available:
yes
Start-up test:
no
Pull-in delay for automatic start:
adjustable 0.1 / 1.0 second
Drop-out delay:
< 50 ms
Rated operating voltage U
e
:
24 VDC ± 15%
Rated operating current I
e
:
0.3 A without external contactors
and additional outputs
Rated insulation voltage U
i
:
50 V
Rated impulse withstand voltage U
imp
:
500 V
Internal electronic fuse:
yes
Power consumption:
< 8 W
Monitored inputs:
Cross-wire short detection:
yes
Wire breakage detection:
yes
Earth connection detection:
no
Number of NC contacts:
4
Number of NO contacts:
4
Outputs:
Stop category 0:
2
Stop category 1:
0
Number of safety contacts:
2
Number of auxiliary contacts:
0
Number of signalling outputs:
4
Switching capacity of
the safety contacts:
Semi-conductor outputs p-type
24 VDC, 700 mA, short circuit proof
Switching capacity of the signalling outputs:
24 VDC, 250 mA,
short circuit proof
LED display:
ISD
Ambient conditions:
Operating temperature:
0 °C ... +55 °C
Storage and transport temperature:
−25 °C ... +70 °C
Protection class:
Enclosure: IP40
Terminals:
IP20
Clearance: IP54
Degree of pollution:
2
Mounting:
Snaps onto standard DIN rail to EN 60715
Connection type:
Screw connection
Min. cable section:
0.25 mm²
Max. cable section:
4.0 mm², solid strand or multi-strand
lead (including conductor ferrules)
Weight:
300 g
Dimensions (H x W x D):
100 x 75 x 110 mm
2.5 Safety classification
Standards:
EN ISO 13849-1; IEC 61508
PL:
up to d
Control category:
up to 3
PFH-value:
1.0 x 10
-7
/ h; applicable for applications
with up to max. 50,000 switching
cycles / year and max. 80 % contact load.
Diverging applications upon request.
SIL:
up to 2
Service life:
20 years