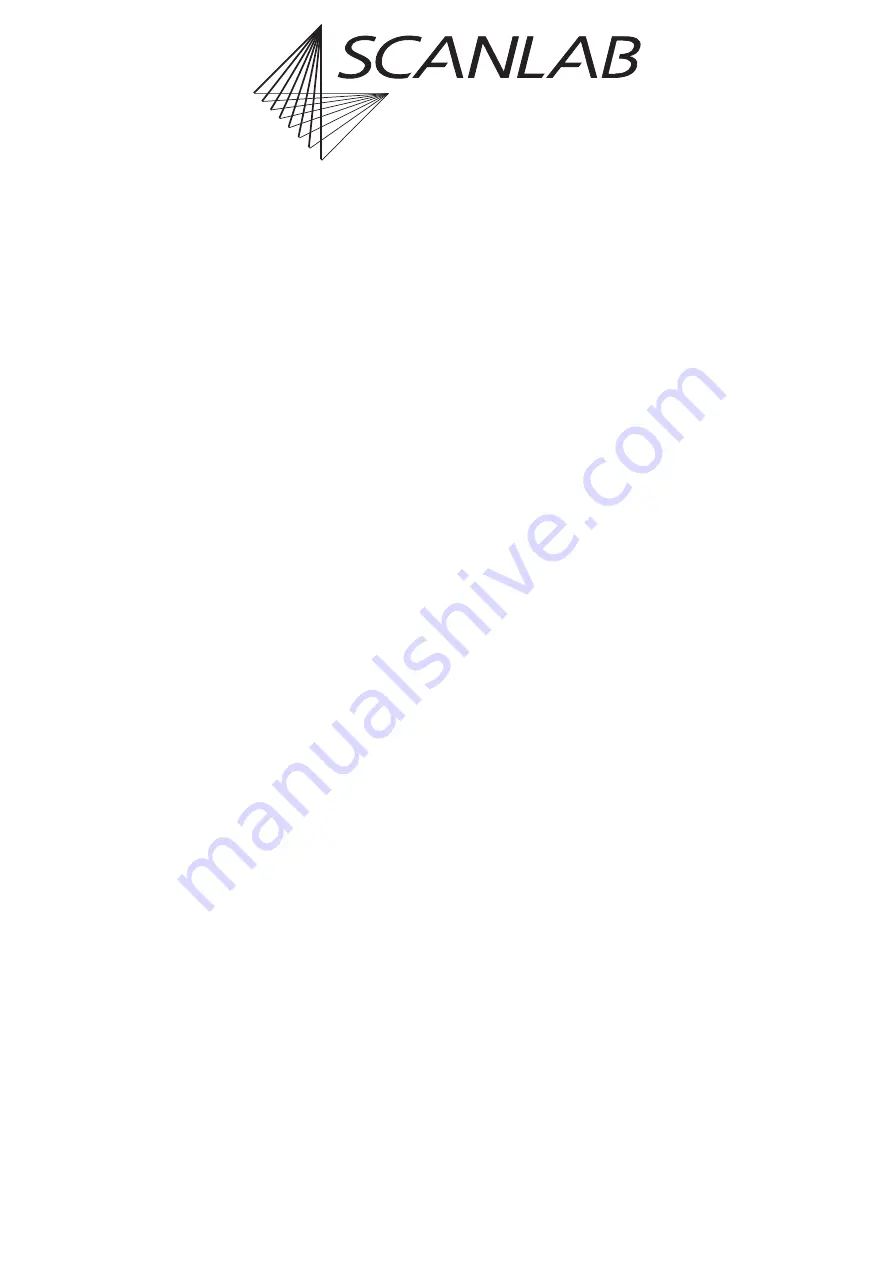
RTC
®
5 PC Interface Board
Rev. 1.9 e
7 Basic Functions for Scan Head and Laser Control
135
innovators for industry
7.4.5 Softstart Mode
For some applications it’s important to control the
laser intensity at the beginning of a marking process.
SCANLAB provides a convenient solution in the form
of the softstart mode, which can be used for all laser
modes (for “laser active” operation).
In the softstart mode, various control values
(
Level
(0) …
Level
(
Number
– 1),
Number
1024) for
as many as the first 1024 pulses (at the beginning of
a marking process) can be defined. Either pulse
length values for the laser signal at the LASER1
output (see
levels for variable laser power can be defined. Analog
voltage softstart values can be outputted either at
the ANALOG OUT1 or ANALOG OUT2 output ports
(see
).
Initialization of the softstart mode is performed via
Here, the type of softstart value is defined. If analog
voltage values are to be outputted, then the analog
output port can also be defined. Afterwards the indi-
vidual softstart control values can be defined via
or
commands.
After the laser control signals are switched on, the
defined softstart values (max. 1024) will be
outputted at the selected output port simultaneously
with the laser pulses of the LASER1 signal – always
with the leading edge of the laser pulse. The
command allows specification of a time period
(
Delay
) for which the laser must have been switched
off before softstart will be activated at the next
switch-on.
Notes
• With a large enough value for the
Delay
time,
one can avoid the softstart mode being also
activated after very short jump commands.
• As soon as the LASERON signal (the laser) remains
switched off longer than
Delay
, the value
Level
(0) is assigned to the output port, provided
the softstart mode has not been meanwhile
deactivated.
• When the LASERON signal is switched on, then
the values
Level
(0) … (
Number
– 1) will be
automatically assigned to the output port simul-
taneously with the first laser pulses.
• Analog softstart values are outputted simulta-
neously with the laser pulses of the LASER1
signal. It might be beneficial under some circum-
stances to acquire these analog softstart values
triggered by a signal shifted back 180° related to
the LASER1 signal. For this purpose, the CO
2
mode provides a LASER2 signal at the LASER2
output. And in the YAG version’s, the signal at the
LASER1 output can be phase-shifted back 180°
via
(Bit #1 = 1). For the CO
2
mode, this is equivalent to exchanging LASER1
with LASER2.
• The laser pulse frequency should not exceed a
value of approx. 308 kHz (this corresponds to a
HalfPeriod
of 104), because
the changing values cannot be transmitted faster.
However, the laser pulse frequency cannot be
automatically checked for this case.
• If Softstart values are to be outputted as analog
voltage levels, then also note that digital-to-
analog conversion of laser frequencies above
around 100 kHz (i.e. for a
-
HalfPeriod
< approx. 320) can’t always be fully
completed. For such laser frequencies, the user
must carefully verify that sufficient capability is
available.
• If Softstart mode is inactive, then values for the
• The Softstart mode is also available in
Laser Mode 4 (see
) and Laser Mode 6
). In this modes, the LASER1 output
only outputs standby pulses and therefore only
analog voltage levels can be variably defined
(
Mode
= 1, 2, 11 or 12).
Here, too, the defined softstart values are
outputted simultaneously with the pulses of an
internally-generated (but not outputted) LASER1
signal. The standby pulses cannot be phase
shifted in laser mode 4 and laser mode 6 and are
not synchronized with the internal LASER1 pulses.
If the period durations of the standby and LASER1
pulses are set (via
) to be equal, then the analog
voltage softstart values will be outputted in
parallel with the standby pulses, though they
might have a (random) constant phase shift with
respect to the standby pulses.
• The Softstart mode cannot be used simulta-
neously with the “freely definable wobbel
shapes“ wobbel mode, see