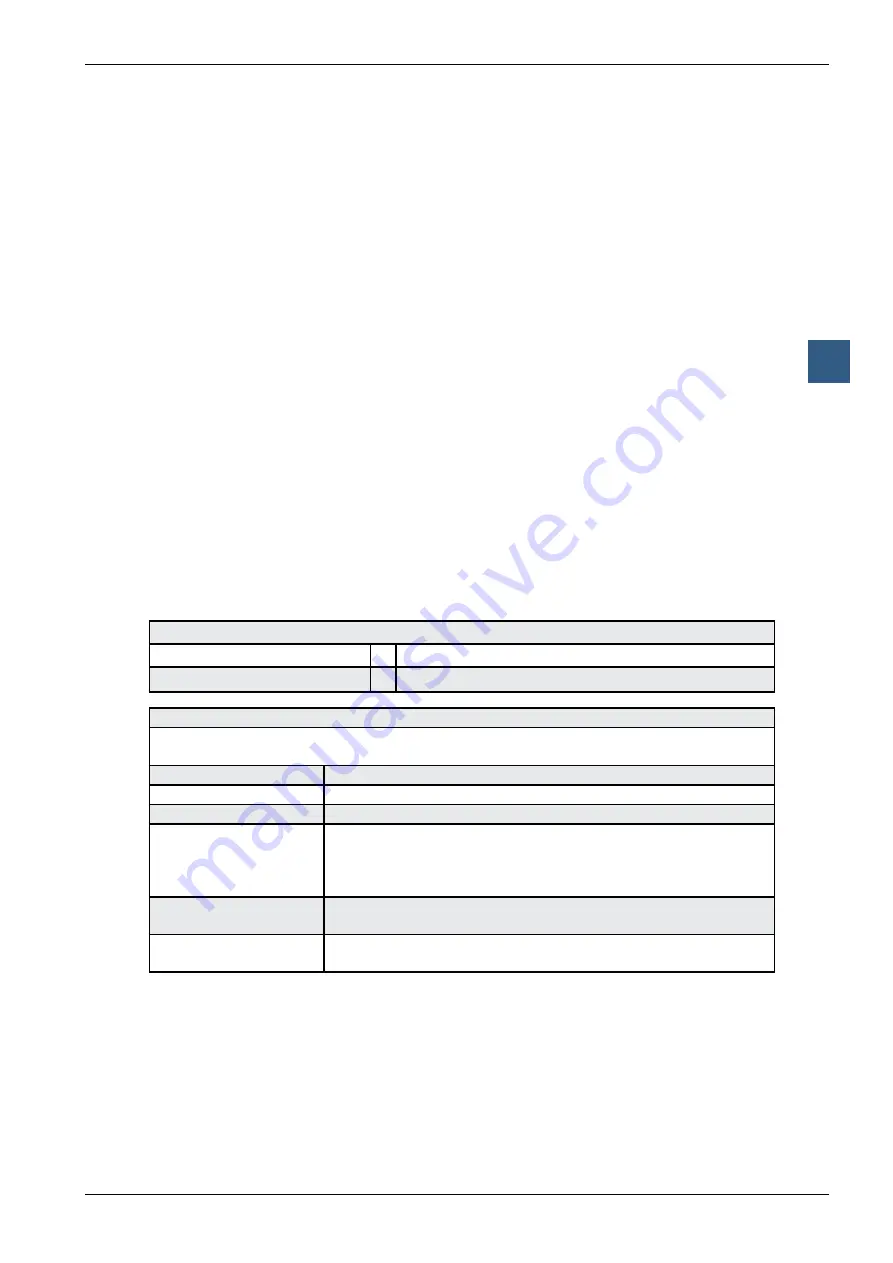
Saia-Burgess Controls AG
Manual
Manual PCD 1 / PCD 2 Series
│ Document 26
/
737 E
N22 │ 2013-11-26
5
Input/output (I/O) modules
5-127
Motion control modules for servo-motors
5.19.2 PCD2.H32x, motion control modules for servo-drives
There are four module types available:
PCD2.H320: 2 axes with 24 V encoder
PCD2.H325: 2 axes with 5 V and SSI absolute value encoder
PCD2.H322: 1 axis (slave operation) with 24 V encoder
PCD2.H327: 1 axis (slave operation) with 5 V and SSI absolute value encoder
The PCD2.H32x motion control modules are intelligent I/O modules in the PCD2
series. They are used to position two independent axes, with one variable speed AC
or DC drive (servo-motor) each, or two axes as an electronic transmission.
This requires the drive unit to have a power stage and incremental shaft encoder for
capturing position or speed. Displacement control may also be achieved with an SSI
absolute value encoder.
Each module contains a DSP processor that independently controls every movement
according to parameters supplied by the user program: velocity, acceleration and
destination position (“PID control”). This enables each axis to execute independent
movements, perform S-curve and trapezoidal motion profiles, change velocity and
acceleration, perform interrupt functions and record the current axis position during
motion.
In a PCD2 with expansion housing, up to 7 PCD2.H32x modules can be operated in
parallel.
Technical data
Function-specific data
Number of systems:
2 for H320/5
1 for H322/7 + 1 H100 counter input 4 DI + 1 DO
Motion parameters
31-bit registers are used for destination position, velocity and acceleration, numerical range
± 2
30
)
Position
Units and resolution selectable (depending on mechanical factor)
Velocity
Units and resolution selectable (depending on mechanical factor)
Acceleration
Units and resolution selectable (depending on mechanical factor)
PID controller
Sample time 100 µs / axis, programmable proportional, integral
and differential factors. Sample time for differential part can be
programmed separately. Additional velocity and acceleration feed-
forward (all 16 bit values)
Analogue controller
output
Velocity set point ± 10 V
(resolution 12 bit)
Counting frequency
max. 125 kHz for H320/5
max. 250 kHz for H322/7